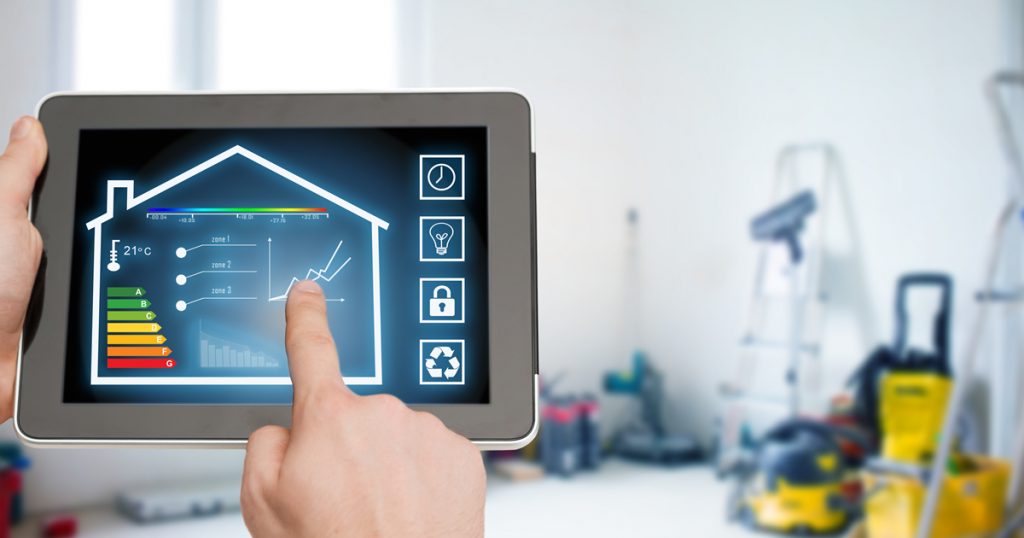
Définition
Un bâtiment intelligent ou « Smartbuilding » est un bâtiment qui cherche à répondre aux enjeux généraux de confort, de bien-être, de sécurité et de performance énergétique et environnementale par l’exploitation des technologies liées au monde numérique.
Architecture et Climat – Janvier 2019

Pour chacun de ces enjeux, le Smartbuilding poursuit 4 objectifs majeurs :
- La flexibilité énergétique,
- La commodité et l’ergonomie,
- L’optimisation et l’efficacité,
- La maintenance et la prévention des pannes.
Le bâtiment intelligent cherche à atteindre ces 4 objectifs pour chacun des enjeux en faisant communiquer et coopérer les systèmes du bâtiment entre eux tout en incluant l’occupant.
Le bâtiment, désormais smart, dispose ainsi de nouveaux outils numériques pour (s’)informer, contrôler, prévoir, optimiser et simplifier la gestion du bâtiment.
Le Building Performance Institute Europe [BPIE] ajoute qu’un bâtiment intelligent :
- « Conduit à une décarbonisation plus rapide des systèmes énergétiques par l’utilisation du stockage d’énergie et l’amélioration de la flexibilité de la demande énergétique ;
- Habilite et responsabilise ses usagers et occupants en leur offrant le contrôle des flux d’énergie ;
- Reconnait et réagit aux besoins des occupants et des usagers en termes de confort, de santé, de qualité de l’air intérieur, de sécurité mais aussi d’exigences pratiques. «
Mais cette « surcouche SMART » présente également des risques et de nouveaux défis pour le secteur du bâtiment. Principalement, ces risques sont : l’échec de la symbiose avec les occupants, la cybersécurité, l’obsolescence des équipements, le surcoût économique et environnemental à rentabiliser (voir plus loin).
Quelle différence avec la GTC ?
Le smartbuilding se différencie de la GTC (Gestion Technique Centralisée) :
- par son champ d’application plus large, allant bien au-delà de la HVAC en intégrant d’autres systèmes (accès, ascenseur, renouvelable, sécurité, …)
- Par son niveau d’interaction plus élevé et plus complexe entre les différentes techniques. Ceci permet à la HVAC, l’éclairage, les protections solaires, le contrôle d’accès,… de fonctionner de concert pour améliorer le confort et la performance du bâtiment.
- par sa philosophie et son caractère beaucoup plus flexible et ouvert. Ces qualités se manifestent vers l’utilisateur qui dispose désormais d’interface conviviales pour configurer ses systèmes à souhait mais également entres les différents systèmes techniques. Dans un Smartbuilding, les éléments ne sont liés entre eux que par un réseau et de la programmation : un détecteur ou un interrupteur n’est pas structurellement relié à une lampe plutôt qu’à une autre. La manière dont les différents éléments d’un smartbuilding interagissent entre eux est désormais flexible et modifiable à souhait.
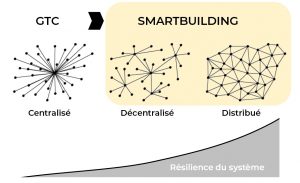
Finalement, alors que le « cerveau » de la GTC est centralisé dans un centre de gestion, celui d’un Smartbuilding est réparti entre les différents systèmes et est présent à plusieurs échelles dans chaque sous-système.
Par exemple, chaque ampoule embarque un logiciel métier mais c’est également le cas de la passerelle qui gère les interactions entre les interrupteurs, les ampoules et le réseau. Un cloud peut également intervenir sur la gestion du système et constituer une source de service supplémentaire. Cette configuration décentralisée et parfois distribuée de la gestion améliore la résilience des systèmes.
Quels sont les systèmes intégrés dans le bâtiment intelligent ?
Concrètement, grâce à l’interopérabilité et à la standardisation lente mais croissante des protocoles de communication, les Smartbuildings sont capables de monitorer, analyser et faire coopérer une variété de systèmes techniques de plus en plus large. La seule limite étant la créativité du concepteur et/ou de l’intégrateur pour répondre aux besoins de l’occupant.
La liste des sous-systèmes pouvant coopérer au sein d’un smart building est sans limite. Nous citerons donc à titre non exhaustif les systèmes principaux les plus souvent intégrés que sont :
- Le système de raccordement au réseau et les compteurs intelligents,
- Le système de production de chaleur,
- Le système de refroidissement,
- Le système de production d’ECS,
- Le système de ventilation,
- Le système de production et d’intégration d’énergie renouvelable,
- Le système de stockage d’énergie,
- Le système d’éclairage,
- La motorisation des parties mobiles de l’enveloppe (stores, fenêtres motorisées…),
- Le système de protection incendie,
- Le système de gestion des eaux,
- Les ascenseurs,
- Le système d’accès et de sécurité,
- La recharge et l’intégration des véhicules électriques,
- Le monitoring et le contrôle du bâtiment,
- Les appareils électroménagers.
Mais aussi, pourquoi pas : la détection de fuites, les livraisons, les déchets (poubelles connectées), l’inventaire, l’agenda partagé (peut coopérer avec les systèmes des salles de réunion, etc…), l’arrosage automatique, …
Gadget ou vraiment « smart » ?
Dans la vie de tous les jours, qu’est-ce qu’un bâtiment intelligent, qu’a-t-il de vraiment smart ?
Gadget : Objet, appareil, dispositif, projet etc…, qui séduit par son caractère nouveau et original, mais qui n’est pas d’une grande utilité.
Smart : Se dit d’un bien dont la maintenance ou le fonctionnement sont assurés par un dispositif automatisé capable de se substituer, pour certaines opérations, à l’intelligence humaine.
LAROUSSE – 2018
Si le concept et l’imaginaire qui entoure le smartbuilding peut sembler un peu « geek » ou gadget au premier abord, la différence entre un bâtiment « non-smart » des années 60’ et un bâtiment intelligent correspond à peu près à la différence qu’on peut retrouver entre un tracteur « full manuel » des années 60 et une voiture hybride semi-autonome d’aujourd’hui !
Le tracteur est composé d’une série d’éléments (phares, moteur, direction, freins…) actionnés et régulés indépendamment par des commandes individuelles, directes et manuelles.

À contrario, et même si nous y sommes habitués et que nous ne le remarquons peut-être plus, nos voitures actuelles sont en réalité des « smartcars » avec tout ce que cela comporte d’aspects positifs, ou pas.
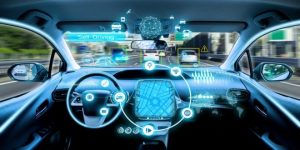
Rendez-vous compte : la voiture hybride choisi seule si c’est le moteur électrique ou thermique qui doit être utilisé en fonction de l’état de la batterie, du réservoir, de la vitesse et du type de conduite ; la voiture ne se déverrouille que lorsque la clé se trouve à proximité, la lumière intérieure s’allume à l’ouverture de la porte ; les phares s’allument automatiquement quand la nuit tombe ; les vitesses passent automatiquement et de manière adaptée à notre conduite du moment ; le volume de la musique baisse lorsque le GPS s’exprime, l’alarme pour la ceinture sonne dès que le siège détecte la présence d’un passager non ceinturé ; le moteur s’éteint au feu rouge, etc…
Tiens, tiens, … entre notre tracteur et notre voiture dernier cri, tout ne serait-il pas devenu interconnecté via un réseau d’information et partiellement automatisé pour faciliter la vie à bord, améliorer le confort, la sécurité et économiser de l’énergie ?
Dans le secteur automobile comme dans le bâtiment, pour être réellement smart, il est important de trouver le bon équilibre entre automatisation et suggestion en fournissant de l’information exploitable par l’utilisateur (entretien à venir, limitation de vitesse, pression des pneus, bouchons, présence d’un obstacle, …) lui suggérant telle ou telle action.
Ainsi, nous ne sommes pas à l’abri de certaines fonctions « gadget » mais, dans leur ensemble, les bâtiments intelligents le sont vraiment et ont un impact mesurable sur l’efficacité énergétique, le confort, le bien-être, la santé et la sécurité des occupants((Vincent Bonneau & Tiana Ramahandry, I. a.-A. (2017, 10). Commission Européenne. (E. Union, Éd.) Consulté le 06 2019, sur https://ec.europa.eu: https://ec.europa.eu/growth/tools-databases/dem/monitor/sites/default/files/DTM_Smart%20building%20-%20energy%20efficiency%20v1.pdf)).
Dans la littérature, nous pouvons observer des réductions de consommation des bâtiments allant de 5-15% pour la HVAC et jusqu’à 60% pour l’éclairage((Vincent Bonneau & Tiana Ramahandry, I. a.-A. (2017, 10). Commission Européenne. (E. Union, Éd.) Consulté le 06 2019, sur https://ec.europa.eu: https://ec.europa.eu/growth/tools-databases/dem/monitor/sites/default/files/DTM_Smart%20building%20-%20energy%20efficiency%20v1.pdf)) en fonction du niveau (très variable) d’intelligence, d’automatisation et d’intégration des systèmes.
Pour conclure, tout n’est évidemment pas mauvais ou inutile dans le smartbuilding mais, comme dans les autres secteurs, il vaudra toujours mieux privilégier les alternatives passives et la sobriété énergétique, plutôt que consommer de manière « Smart ».
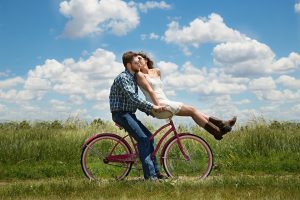
Quels sont les risques liés au smartbuilding ?
Les risques inhérents à la mise en œuvre sont au nombre de 4 :
- Risque d’échec de la symbiose avec les occupants,
- Risque de faille informatique, cybersécurité,
- Risque d’obsolescence des équipements et softwares,
- Risque de surcoût économique et environnemental non rentabilisé.
Échec de la symbiose avec les occupants :
Si le projet va trop loin dans l’automatisation, l’optimisation et la prédiction tout en réduisant les possibilités de déroger et d’interagir avec les systèmes, alors l’occupant perd la maitrise de son bâtiment. Il pourrait se retrouver sans levier d’action et ne plus comprendre pourquoi en plein hiver les stores se ferment au premier rayon de soleil alors que lui, en plein « blue monday », est à la recherche de Vitamine D !
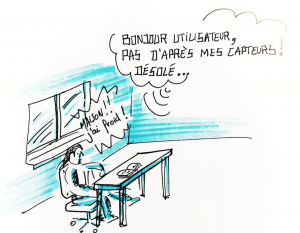
Il faudra à tout prix éviter ce décalage entre d’un côté, une sombre optimisation énergético-économique opérée par une machine et de l’autre, les envies et besoins impulsifs éminemment humains des occupants. Pour éviter ce clash, la « machine » devra fait preuve de transparence, flexibilité, interactivité et convivialité !
Plus généralement, pour qu’un projet de smartbuilding soit positivement adopté par les utilisateurs, celui-ci devra répondre de façon proche et avec tact aux besoins de ces derniers. Pour donner toutes ses chances au projet de Smartbuilding, le concepteur et l’intégrateur (qui sont parfois une même entité) devraient être impliqués dans le projet et échanger avec les occupants et les acteurs de la construction (Architecte, entrepreneur, électricien, …) dès les premières esquisses puis tout au long du projet.
C’est notamment lors de ces discussions que les « fourchettes » d’action (borner le chauffage entre 16°C et 22°C par exemple) et que les limites de la paramétrisation laissées à l’occupant via les diverses interfaces sont définies. À l’issue de ces discussions, un équilibre devra être trouvé entre, d’une part :
- garantir la robustesse du système et éviter que l’occupant puisse toucher à trop d’éléments techniques, ce qui risque d’engendrer des dysfonctions
- et, d’autre part, lui permettre d’ajuster, de déroger sur suffisamment de paramètres pour qu’il conserve le contrôle et la maitrise de son bâtiment.
Risque de faille informatique, la cybersécurité
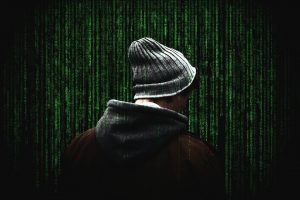
L’autre risque qui survient quant on mandate des machines pour prendre des décisions à notre place et qu’on les interconnecte entre elles est celui de la cybersécurité : « Et si quelqu’un s’infiltre et prend les commandes de mon bâtiment ? Ou pire, s’il utilise la connection d’une ampoule comme passerelle pour s’infiltrer sur mon serveur d’entreprise et voler mes données ? »
Bien que les inquiétudes soient légitimes, bien que la vigilence soit de mise, il n’y a pas de raison de s’en inquiéter irrationnelement ou, en tous cas, plus que nous le faisons déjà avec notre réseau Wifi, notre smartphone, mots de passes ou nos clés d’appartement.
Étant donné qu’aucun système de sécurité n’est fiable à 100%, que ce soit les serrures de votre bâtiment ou son alarme, la bonne pratique en matière de (cyber)sécurité est d’agir proportionnellement. Cela commence en évaluant la valeur des données et/ou des biens que renferme le bâtiment pour définir un niveau de sécurité adapté à atteindre et l’appliquer partout : à son smartbuilding, au réseau wifi, aux serrures physiques du bâtiment, aux mots de passes des adresses mail, …
Par analogie : « Installer une porte blindée ne sert à rien si la fenêtre reste ouverte. »
Il faut donc prendre la question de la cybersécurtié au sérieux et faire réaliser un audit pour définir le niveau de protection à atteindre mais également garder à l’esprit que d’importants progrès en la matière sont réalisés jour après jour et que les cas de cyberattaques directement liées à une faille d’un Smartbuilding sont relativement rares. Si les données que renferment le bâtiment ont de la valeur, il est toujours possible d’étanchéifier le réseau « smartbuilding » du/des réseaux qui renferment des données sensibles.
Si, au départ, le cloud avait une place importante dans le smartbuilding, suite à la révélation de certaines failles informatiques conséquentes, il est de moins en moins utilisé. Aujourd’hui, le remote controling du smartbuilding est réalisé par réseau privé virtuel ou VPN. Sans entrer dans les détails, un VPN fonctionne comme un tunnel temporaire et étanche qui permet de se connecter directement à distance à un ordinateur situé dans le bâtiment. Contrairement au Cloud qui « discute » tout le temps avec le bâtiment, ici un tunnel n’est ouvert qu’en cas de besoin et l’ensemble se déconnecte quand il n’y a plus d’échanges.
Le risque d’obsolescence des équipements et des softwares.
Les premiers smartbuilding sont relativement récents de sorte que les retours sont peu nombreux et ne permettent pas de déterminer avec certitude si ces bâtiments feront face à un phénomène d’obsolescence ou non. Néanmoins, quelques éléments de réponses peuvent être apportés.
Tout d’abord, l’interopérabilité et la structure du réseau « plug and play » décentralisé ou parfois distribué des systèmes du smartbuilding est un gage de résilience et donc de durabilité. Dans ces systèmes peu hiérarchisés et non-linéaires, chaque élément ou presque peut-être remplacé ou retiré individuellement. D’autres éléments peuvent éventuellement être ajoutés. C’est un système évolutif, ce qui facilite grandement les réparations, adaptations, remplacements.
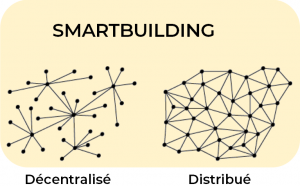
Cependant, qui dit systèmes évolutifs, dit également systèmes qu’on aura envie de faire évoluer. La tentation de compléter son système avec des équipements « gadgets » superflus ou par la nouvelle version de l’un ou l’autre équipement peut indirectement être source de gaspillage et d’obsolescence.
Si la GTC appartient progressivement au passé, celle-ci avait la qualité de pouvoir accompagner un bâtiment plus de 15 ans sans modification ou encombre majeure.
Quand nous observons les durées de vies couramment observées des softwares, objets connectés et autres tablettes, nous pouvons légitimement douter de la pérennité de l’ensemble des composants du smartbuilding.
- >30-50 ans pour un bâtiment,
- >15-20 ans pour un équipement de technique,
- ±8-10 ans pour un objet connecté,
- ±4-6 ans pour un système d’exploitation
- Et ±2-4 ans pour une application
Risque de voir le surcout économique et environnemental non rentabilisé sur la durée de vie
La Smartbuilding poursuit, entre autres, un objectif d’efficacité environnementale et de rationalisation de la consommation d’énergie. Le Maitre d’ouvrage cherche de surcroit à réaliser des économies en réduisant la consommation et l’empreinte environnementale de son bâtiment.
Le premier risque d’un smartbuilding est d’observer une optimisation énergétique et une baisse de la facture énergétique insuffisamment conséquente pour compenser le surcoût « smart » lors de la construction du bâtiment.
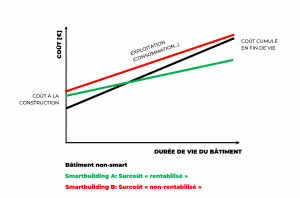
Ensuite, comme les nombreuses sondes, équipements, puissances de calcul, … sont sous-tension et communiquent 24h/24, 7j/7, ils engendrent une consommation d’électricité non négligeable. Ces équipements supplémentaires ont également une empreinte en énergie grise liée à leur fabrication dont il faut tenir compte. Le second risque serait que cet « investissement environnemental supplémentaire » ne soit pas au moins compensé par l’économie et la rationalisation énergétique que ces équipements génèrent au cours de leurs vies.
On estime qu’en 2025 les objets connectés auront une consommation équivalente à un pays comme le Canada.
Basé sur les chiffres de l’AIE (Agence Internationale de l’Énergie) – 2013
Le « smart » : un progrès (in)contournable ?
Un faisceau d’incitants directs et indirects comme le « SRI », l’intégration croissante du renouvelable, l’encouragement à l’autoconsommation, le choix européen d’orienter la mobilité vers l’électrique, des attentes et des normes de confort et de commodité croissantes vont pousser chaque jour un peu plus à « smartiser » nos bâtiments.
Si la volonté est de se doter des dernières technologies pour profiter des fonctionnalités et services les plus à la pointe, alors le Smart et l’interconnexion deviendront incontournables.
L’automatisation de certaines tâches et l’optimisation du bâtiment nous permet alors de multiplier les fonctionnalités, les services, rationnaliser la consommation d’énergie et améliorer le confort tout en nous soulageant d’une partie de la gestion et de la programmation.
Néanmoins, nous observons également combien la course au progrès se fait régulièrement au détriment du bon sens et de la maitrise de son environnement. C’est pourquoi nous pensons qu’il nous revient, au cas par cas, de définir si un tel progrès est de nature à répondre à un besoin réel ou non. Plutôt que d’offrir des solutions à un problème qui n’existe pas, le smartbuilding se devra de répondre sur-mesure aux besoins et aux attentes propres à chaque groupe d’occupant.
D’un point de vue uniquement énergétique, si nous devions positionner l’intégration du « smart » dans une stratégie de conception telle que la trias-energetica, elle trouverait assurément sa place en queue de peloton :
- lorsque les besoins sont réduits au maximum rationnel (Optimisation de l’enveloppe, des comportements…),
- que la plus grande part possible des besoins est couverte par des énergies renouvelables,
- et que le complément (fossile) est produit avec le meilleur rendement possible
Alors seulement, comme dernier effort, le smartbuilding devrait être envisagé et intégré au bâti de manière à rationnaliser toujours plus les besoins, optimiser l’autoconsommation, perfectionner le confort et améliorer l’efficacité et la gestion énergétique.
Il serait hautement souhaitable que l’utilisation de cette force de calcul puisse, paradoxalement (?), se mettre au service des solutions Low-Tech et passives en les rendant plus autonomes et intelligentes de manière à les rendre aussi efficaces que certains systèmes actifs complexes, lourds et consommateurs d’énergie.
En effet, des éléments architecturaux « basiques » comme les fenêtres ouvrantes ou les volets sont des composants formidablement simples et efficaces pour refroidir ou ventiler un bâtiment. Leur unique « défaut » réside éventuellement dans leur mauvaise utilisation : faute d’information et de capacité d’anticipation de l’occupant mais également dans l’impossibilité d’être actionné en dehors des horaires d’occupation.
Avec un peu d’IA et quelques sondes simples, l’utilisateur peut, par exemple, être informé anticipativement par une simple diode LED de l’intérêt ou non d’actionner tel ou tel dispositif de manière à adapter et optimiser son utilisation des ouvrants.
Dans certains cas judicieux, pour aller plus loin, ces éléments peuvent être connectés et motorisés de sorte que, lorsque l’utilisateur est absent, le smartbuilding pourra prendre le relais et actionner ces systèmes simples avec très peu de moyens techniques et énergétiques.
Architecture et Climat – Janvier 2019