Remplacer une chaudière d’un ensemble de chaudières de puissance moyenne
À l’heure actuelle, lorsqu’une chaudière traditionnelle dans un ensemble de chaudières doit être remplacée quelle qu’en soit la raison, on privilégiera une chaudière à condensation. D’une part, la technologie des chaudières à condensation est au point par rapport à tous les problèmes de corrosion liée à l’agressivité des condensats dans l’échangeur de la chaudière, d’autre part, le prix a sensiblement diminué.
D’un point de vue énergétique, on ne présente plus l’intérêt de la chaudière à condensation. L’objectif du remplacement d’une chaudière classique par une chaudière à condensation est donc bien de privilégier le fonctionnement de cette dernière pendant un maximum de temps. Dans cette configuration, la chaudière classique n’a plus qu’un rôle d’appoint en période froide lorsque la puissance de la chaudière à condensation n’est plus suffisante ou de « backup ».
Le remplacement d’une chaudière classique par une chaudière à condensation ne se fait pas en un coup de baguette magique ! Il est nécessaire la plupart du temps :
- D’adapter l’hydraulique de l’installation tant au niveau de la production que de la distribution ;
- De prévoir une régulation capable de concilier le fonctionnement de l’ensemble des chaudières.
Revoir la puissance de chaudière à la baisse
Comme développé ci-avant le surdimensionnement des anciennes chaudières est un fait avéré. Indépendamment du surdimensionnement « naturel » de la plupart des installations de chauffage, le projet de rénovation d’une partie de la chaufferie implique une réévaluation des besoins thermiques du bâtiment. En effet, différentes mesures de réduction des besoins ont pu être prises comme :
- L’isolation partielle ou totale de l’enveloppe du bâtiment (remplacement des simples vitrages par des vitrages à basse émissivité isolation de la toiture, des murs, …) ;
- Des actions URE sur des équipements comme la ventilation hygiénique par exemple.
Cette réévaluation peut être réalisée :
- De manière simple, mais avec une bonne approximation, comme le calcul statique des déperditions (calcul du U*S*ΔT) ;
- De manière plus sophistiquée, mais plus précise au moyen d’une simulation thermique dynamique déterminant les besoins de chaleur heure par heure tout au long de l’année.
Dans les deux cas, il est conseillé de faire appel à un bureau d’étude spécialisé en technique spéciale.
Si la rénovation se réalise sur des chaudières de faible puissance, faire appel à un bureau d’étude se justifie difficilement au niveau financier. Il n’empêche, c’est dans votre intérêt de sensibiliser l’installateur par rapport à ce surdimensionnement.
Une règle d’or : signalez-lui toutes les améliorations qui ont été réalisées sur l’enveloppe du bâtiment au cours des années ! C’est vous qui connaissez le mieux le bâtiment !
L’exemple ci-dessous montre qu’énergétiquement et financièrement parlant, le remplacement d’une chaudière classique à brûleur pulsé par une chaudière à condensation à brûleur modulant est intéressant.
Exemple 3 : dans un immeuble de bureaux, on décide de remplacer une des deux chaudières de 600 kW par une chaudière gaz à condensation en intégrant la notion de surdimensionnement :
> Situation de départ :
- 2 chaudières à brûleur à air pulsé (2 allures) de 600 kW de 1983, soit 1 200 kW installés pour un besoin réel maximal de 600 kW
- fonctionnement en parallèle des chaudières
- pertes à l’arrêt des chaudières : 0.2 %
- rendement de combustion : 94 % en 1ère allure et 92 % en deuxième
- rendement saisonnier de production calculé : 92.3 %
- consommation annuelle : 155 000 litres de fuel par an
> Situation projetée :
- 1 chaudière existante est conservée
- 1 chaudière à condensation de 360 kW avec brûleur modulant
- fonctionnement en cascade des chaudières
- pertes à l’arrêt des chaudières : 0,2 %
- rendement de combustion de la chaudière conservée : 94 % en 1ère allure et 92 % en deuxième
- rendement de combustion de la chaudière à condensation : 108 % à 60 % de taux de charge et 106 % à 100 % de taux de charge
- rendement saisonnier de production calculé : 105.6 %
- consommation annuelle : 155 000 [litres/an] x 92.3 [%] / 105.6 [%] = 135 478 [litres/an]
- gain énergétique : 19 521 [litres/an] (soit 15 %)
- gain financier (à 0,8 €/litre en 2012) : 15 619 [€/an]
|
Adapter l’hydraulique de l’installation
Cas de chaufferie avec ECS préparée séparément
L’insertion d’une chaudière à condensation dans un ensemble composé de plusieurs chaudières de technologie ancienne risque immanquablement de perturber le fonctionnement des autres chaudières et des circuits secondaires.
À moins de remplacer à l’identique (déconseillé), ce n’est que trop rarement du « plug and go » ! Hydrauliquement parlant, il faut donc être très prudent et, en règle générale, faire appel à un bureau d’étude spécialisé.
Quel que soit le cas envisagé, l’objectif de l’adaptation du circuit hydraulique sera toujours le même : ramener de l’eau la plus froide possible au niveau de la chaudière à condensation !
Indépendamment de l’hydraulique, il est obligatoire, pour arriver à optimiser l’installation, de passer à une régulation de température de sortie chaudière GLISSANTE et variable en fonction de la demande et/ou de la température extérieure ! Il n’y a plus de limite inférieure puisque la chaudière est à condensation. La distribution de chaleur à température plus modérée améliore également les pertes de distribution !
De nombreuses installations existantes sont équipées :
- soit d’un bouclage à l’extrémité du collecteur entre le départ et le retour (boucle A-B) ;
- soit d’une bouteille casse-pression.
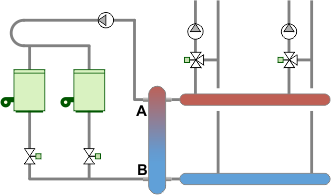
Collecteur bouclé et bouteille casse-pression.
Dans le cas d’un bouclage, celui-ci permet un retour chaud au niveau des chaudières. Ce bouclage est indispensable :
Lorsqu’on envisage de remplacer une des chaudières classiques par une chaudière à condensation, il est indispensable :
- de maintenir une température de retour au-dessus de la température de condensation dans la chaudière existante ;
- de continuer à garantir un équilibre hydraulique entre les circuits primaires et secondaires d’une part et, d’autre part, les circuits secondaires entre eux ;
- de favoriser un retour froid au niveau de la chaudière à condensation.
Bref, on peut parler d’un casse-tête … belge ! Mais comme nous sommes les champions du compromis, il existe des solutions capables de répondre aux différentes exigences tout en garantissant le respect des exigences de fonctionnement de chaque équipement.
Dans ce qui suit, une méthode de modification de l’installation est proposée. Ce n’est certes pas la seule, mais elle permet de rassembler pratiquement tous les impératifs liés au fonctionnement conjoint d’une association de chaudières de générations différentes avec un circuit hydraulique existant. On notera toutefois qu’il est toujours nécessaire de vérifier l’implémentation hydraulique chez le fabricant.
Étape 1 : enlèvement du bouclage
Le bouclage n’est pas favorable au retour froid vers la chaudière à condensation. Par contre, le fait de vouloir le supprimer comme dans un collecteur ouvert risque de perturber l’équilibre hydraulique entre le circuit primaire et les circuits secondaires,
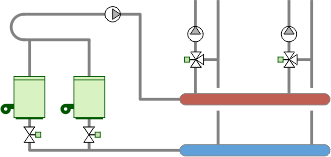
Bouclage enlevé.
Étape 2 : placement d’une bouteille casse-pression
Le placement d’une bouteille casse-pression évite les perturbations hydrauliques, mais ne garantit pas, quelle que soit la demande des circuits secondaires :
- Un retour chaud pour l’ancienne chaudière ;
- Un retour froid pour favoriser la condensation de la nouvelle chaudière ;
- Un débit contrôlé dans chaque chaudière, dû au fait que le débit de la pompe primaire est fixe.
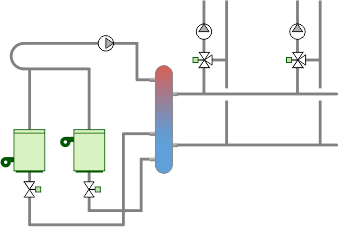
Placement d’une bouteille casse-pression : variante 1 et 2.
Étape 3 : individualisation des débits des chaudières
Le remplacement de la pompe primaire unique par une pompe individuelle à débit variable au niveau de chaque chaudière permet de les irriguer de manière totalement autonome vu que leur technologie est rarement la même (ancienne chaudière à grand volume d’eau ⇐⇒ nouvelle chaudière à faible volume d’eau). Le bouclage sur la chaudière existante permet d’assurer, quelle que soit la température de retour primaire à la sortie de la bouteille casse-pression la température minimale nécessaire à la non-condensation des fumées de combustion nécessaire à cette technologie de chaudière.
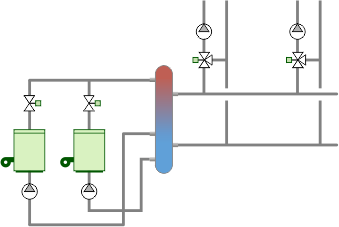
Individualisation des débits des pompes : variante 1 et 2
Cette configuration de l’hydraulique de la chaufferie est suffisante pour garantir la pérennité de l’installation, mais ne garantit toujours pas le contrôle de la température de retour à la sortie de la bouteille casse-pression.
Étape 4 : adaptation de la régulation
Une manière intéressante de garantir une température de retour froide à la sortie de la bouteille casse-pression est d’adapter en permanence les débits des pompes primaires de manière à respecter à tout moment la règle suivante : débit primaire Qp < débit secondaire Qs.
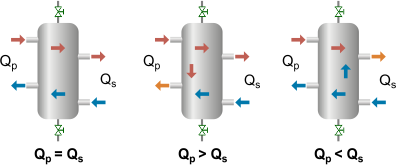
Lorsque le débit primaire < débit secondaire de la bouteille casse-pression, le retour côté primaire reste froid et garantit au niveau de la chaudière à condensation un retour froid. Cette disposition implique que la régulation de cascade des chaudières soit adaptée. Une manière d’y arriver est de contrôler la différence de température comme le propose la figure suivante : on régule le débit de la chaudière à condensation pour une maintenir une différence de température entre l’entrée côté primaire (Tp) et la sortie côté secondaire (Ts) de la bouteille casse-pression de l’ordre de 2°C. (Tp > Ts). Lorsque l’écart de température augmente, il faut augmenter le débit de la pompe de circulation de la chaudière, et inversement).
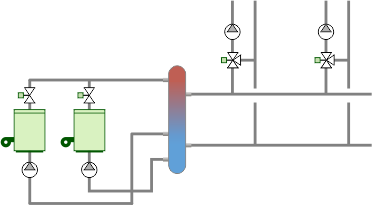
Adaptation de la régulation : variante 1 et 2.
- Lorsque la demande de chaleur diminue, les vannes 3 voies ont tendance à se fermer et, par conséquent, le débit secondaire à diminuer, la température Ts augmente. Sans changer le débit de la pompe primaire de la chaudière à condensation, l’écart entre les températures Tp et Ts diminue. La régulation prévoira de diminuer le débit primaire de manière à respecter la loi selon laquelle le débit primaire < débit secondaire ;
- À l’inverse, lorsque la demande de chaleur augmente, l’écart entre Tp et Ts augmente, nécessitant d’augmenter le débit de la pompe de la chaudière à condensation pour ramener cet écart à 2°C.
Cas où l’ECS est combinée avec le chauffage
Le remplacement d’une chaudière classique par une chaudière à condensation dans un ensemble de chaudières qui alimente à la fois des circuits statiques, des batteries chaudes de centrales de traitement d’air (CTA) et de l’ECS risquent de poser un problème si on n’y prend pas garde ! En réalité, tout est conditionné par le profil de besoin de chaleur :
> Une école, un immeuble de bureaux ont des consommations d’ECS généralement faibles et discontinues. L’adaptation de l’hydraulique peut être envisagée comme présenté ci-dessous. Pendant la production d’ECS, la chaudière à condensation ne travaillera pas dans des conditions optimales. Mais cette période est brève, ou la quantité de chaleur est faible.
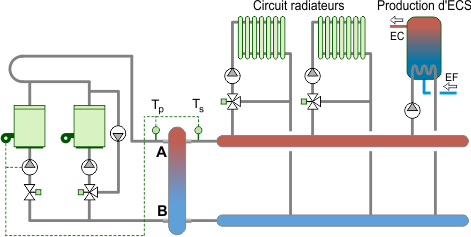
Consommation faible d’ECS.
> Un hôpital, un hôtel, un magasin alimentaire, … ont un besoin d’ECS qui peut être important et relativement continu. Dans ce cas, l’exploitation optimale de la condensation de la chaudière devient difficile en considérant le schéma hydraulique envisagé jusqu’à maintenant. Une solution réside dans le choix d’une chaudière à condensation à un seul retour et à un surdimensionnement de l’échangeur de production ECS pour avoir des retour ECS les plus froids possible !! D’autre part, il y a lieu d’envisager dans ce cas de séparer la production ECS du chauffage !
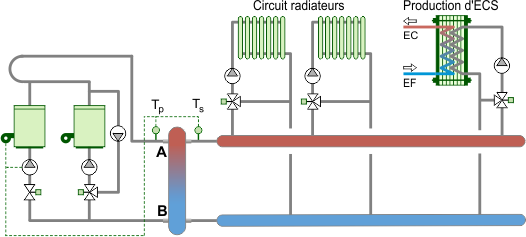
Consommation faible d’ECS.
Adapter les régimes de température
Lors d’une rénovation de la chaufferie, le réglage des courbes de chauffe d’une installation de chauffage est naturellement dépendante de la performance énergétique de l’enveloppe du bâtiment :
> Sans changement de la performance de l’enveloppe, le besoin de chaleur reste le même et les régimes de température des circuits secondaires restent inchangés Le remplacement d’une chaudière classique par une chaudière à condensation risque d’être moins intéressant. Cependant, comme le montre le graphique suivant, pour un régime de température classique dans des bâtiments peu isolés de 90/70°C (100 % de charge) et sachant que, durant 75 % du temps de la saison de chauffe, les besoins en puissance de chauffage se situe en dessous de 60%, les températures de retour vers la production de chaleur sont sous 55°C ; ce qui implique qu’une nouvelle chaudière sur un tel circuit condense théoriquement pendant 75 % de la période de chauffe. Il est donc intéressant d’envisager la chaudière à condensation même sans ambition d’amélioration de la performance de l’enveloppe du bâtiment.
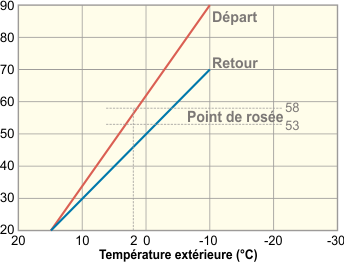
Courbe de chauffe : régime 90-70°C.
> En changeant la performance de l’enveloppe (remplacement des châssis vitrés, isolation des parois, placement d’un récupérateur de chaleur sur une ventilation hygiénique à double flux, …), le besoin de chaleur doit être revu à la baisse. Il n’est plus nécessaire de maintenir un régime de température de 90/70°C. Un régime de 80/60°C voire 70/50°C est plus approprié. En analysant le graphique ci-dessous, on constate que la plupart du temps la chaudière à condensation condense. Attention toutefois de ne pas trop réduire le régime de température sous peine de voir la chaudière traditionnelle condenser lorsqu’elle fournit un faible appoint à la chaudière à condensation. On « pourrait » observer ce phénomène lorsque les températures externes sont aux alentours des 0°C.
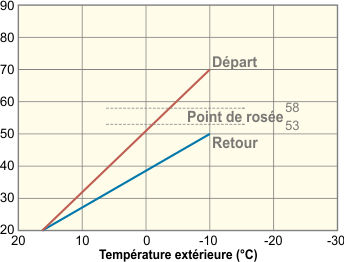
Courbe de chauffe : régime 90-70°C.
Adapter le conduit de cheminée
Vu que les températures de fumée à la sortie de la chaudière à condensation sont plus basses, le risque de condensation résiduelle dans la cheminée risque de la détériorer. Le coût du gainage du conduit de cheminée devra être pris en compte dans l’étude. Suivant la configuration de la chaufferie il peut être non négligeable.
Et les autres chaudières ?
Quand la décision est prise de remplacer une chaudière, il faut s’attendre à devoir investir dans le remplacement de la ou des autres chaudières composant l’ensemble. Si le remplacement de la première chaudière intervient suite :
- À la vétusté de la chaudière, il est clair que la ou les autres chaudières risquent d’être dans le même état. Il s’ensuit qu’il sera nécessaire à terme de prévoir financièrement le remplacement de la ou des chaudières restantes.
- À une étude énergétique et financière favorable, le remplacement de la ou des autres chaudières peut être envisagé de manière plus posée et sereine. On l’envisagera plutôt dans le cadre de l’utilisation rationnelle de l’énergie.
Traiter les condensats
En régime permanent, une chaudière gaz à condensation de 250 kW produit en moyenne environ 37.5 litres/h de condensats.
Ces condensats sont légèrement acides (H2O + CO2). Le degré d’acidité est du même ordre de grandeur que celui de l’eau de pluie (pH : 3,8 .. 5,2). De plus l’acidité de ceux-ci est souvent compensée par le caractère plutôt basique des eaux d’entretien ménager. Ceci explique qu’il ne soit pas obligatoire de traiter les condensats avant leur évacuation à l’égout. Il sera fortement conseillé dans les grandes chaufferies de traiter quand même ces condensats en raison de leur importance relative par rapport au volume d’eau usée globalement traitée.
Dans le cas d’une chaufferie en toiture, il est recommandé de ne pas faire couler les condensats sur la toiture ou directement dans les gouttières (légère acidité, risque de gel et de bouchage des évacuations). Un conduit en matière synthétique raccordé directement à l’égout est indiqué.
Pour une chaudière à mazout à condensation, la neutralisation des condensats est obligatoire (ph 2,5, pratiquement de l’acide sulfurique…).