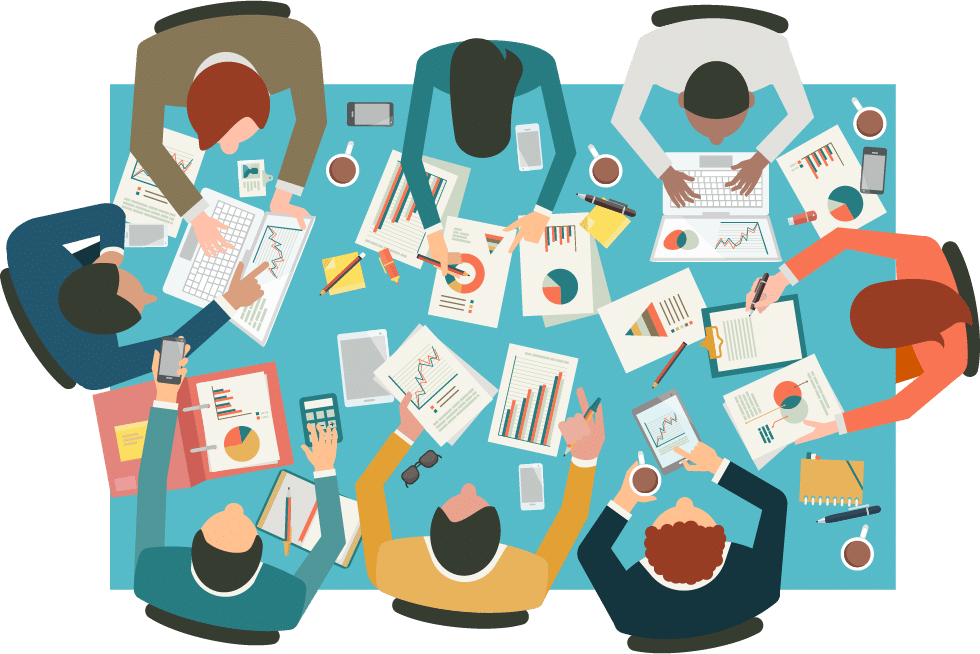
La POE peut être ressentie comme intrusive ou une forme de contrôle, voire de test de la part de sa hiérarchie. Pour que la démarche soit réussie, il est primordial que la neutralité et l’absence de pression soit de mise. Il est également essentiel que la démarche soit introduite, présentée et suggérée plutôt qu’imposé au sein de l’établissement.
La POE aura dès lors de bonnes chances d’être un processus riche et enthousiasmant pour tous si :
- Avant la réalisation de la POE :
- chacun a été informé du sens de la démarche
- chacun a pu s’exprimer sur les thématiques qu’il veut intégrer dans l’évaluation.
- Pendant la réalisation de la POE :
- Chacun peut s’exprimer,
- Les enquêtes sont rendues anonymes pour celles et ceux qui le souhaitent
- Aucune prise de mesure intrusive non souhaitée n’est réalisée (respect de la vie privée…)
- Après la POE :
- Les données brutes sont converties en infographies circonstanciées, claires et lisibles.
- Des actions sont listées et prises en réaction aux résultats de la POE.
- Une date ultérieure de réévaluation est définie.
- Un rapport final comprenant les infographies, les actions prises et la date de réévaluation est diffusé à chacun le plus rapidement possible.
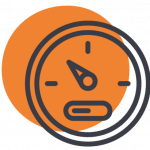
Pour qu’une démarche de POE soit la plus efficiente possible, celle-ci devrait :
- Être reconduite à intervalles réguliers: en effet, tous les problèmes ne peuvent être identifiés ou expliqués du premier coup. Il faudra mettre en place de nouvelles actions puis relancer une campagne d’évaluation plus tard pour savoir si les actions vont dans le bon sens. De plus, l’activité pratiquée dans le bâtiment et les occupants changent avec les temps, c’est pourquoi l’opération gagne à être répétée régulièrement. Dans l’idéal, le feedback devrait s’effectuer en continu et être compilé régulièrement à la suite des campagnes de POE.
- Être le plus détaillé et « sur-mesure » possible: des informations brutes riches et précises permettent une interprétation plus fine des résultats. Un équilibre est bien entendu à trouver pour limiter le niveau d’intrusion, respecter la vie privée et ne pas induire une charge de travail trop importante pour la réalisation de la POE. Il faudra donc veiller à calibrer le niveau de détail en fonction de l’intérêt et de l’implication qu’il implique.
- Une bonne pratique consiste à commencer par une première campagne un peu plus généraliste qui permettra de cerner les grands enjeux. Les campagnes suivantes pourront alors s’attarder sur les détails, mais uniquement sur les sujets qui posent des soucis.
- Être sans équivoques et pratique à réaliser pour les occupants : des enquêtes difficiles à remplir, des questions floues avec des doubles/triples négations, des questions identiques, mais simplement reformulées dans un même questionnaire sont autant d’éléments qui suscitent le désintérêt et parfois la méfiance envers la démarche. Là aussi il faudra faire court, clair et convivial.
- Permettre une visualisation des résultats rapide et parlante pour les propriétaires et les occupants afin de maintenir la dynamique en marche.
- Faire partie intégrante de la gestion générale du bâtiment. Plus la démarche fait l’objet de mesures quotidiennes et s’intègre aux pratiques habituelles déjà en place plus la POE pourra être un outil disponible et réactif pour l’ensemble des parties prenantes.
Comment recueillir l’information ?
Il existe beaucoup de moyens différents pour évaluer le bon fonctionnement de son édifice.
Chaque technique aura des avantages et des inconvénients et sera plus ou moins adapté à un type d’information que l’on souhaitera recueillir. Il faudra alors évaluer au cas par cas la ou les- méthodes les plus adaptées. Dans la plupart des cas il faudra combiner plusieurs méthodes.
De façon générale on tendra à brasser large au début pour très rapidement se concentrer sur les thématiques essentielles. Rien ne sert de rentrer dans les détails lorsque tout va bien. De la même manière, on cherchera à recueillir l’avis de tous sur tout dans un premier temps puis on se concentrera sur les zones, les individus et les problèmes qui méritent d’être investigués plus en profondeur.
Pour que la POE soit efficace, il faut que l’ensemble des occupants adhèrent avec la démarche et soient proactifs. Il faut donc à tout prix éviter de les bombarder avec des questionnaires et des interviews interminables sur des sujets peu intéressants.
On tentera donc d’être rapide, to-the-point et d’éviter les répétitions.
Les différentes façons d’obtenir de l’information sont présentées dans un ordre chronologique, méthodique, comme des étapes successives, mais rien n’empêche de sauter des étapes, de les intervertir ou de n’en réaliser que l’une ou l’autre.
POE – Recueillir des informations : La visite
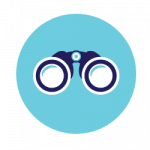
La façon la plus rapide et qui ne demande aucun effort de la part des occupants est la visite. La visite se fait idéalement en présence d’une responsable ou gestionnaire des aspects techniques du bâtiment, mais aussi de la personne en charge des occupants (RH…). En faisant le tour du bâtiment, la personne en charge de l’évaluation peut déjà de façon informelle préparer et expliquer la démarche en cours aux occupants curieux, mais également et surtout prendre connaissance du lieu et d’un grand nombre de données bien utiles pour se faire une idée des problèmes potentiels et ajuster une éventuelle future enquête, interview… :
- La localisation et l’orientation du bâtiment,
- La disposition des espaces,
- Les installations techniques présentes, leur état, leur répartition,
- Récupérer au vol des commentaires d’occupants en circulant dans le bâtiment, Ressentir ou relever rapidement les ambiances en se munissant d’un thermomètre, luxmètre, anémomètre…
La visite permet également de s’entretenir avec les personnes en charge de la gestion technique et humaine pour relever l’historique du bâtiment, ses défauts connus et tout simplement laisser l’opportunité aux responsables de s’exprimer et pointer les points qui lui semblent importants pour la suite.
À ce stade, les seules personnes impliquées sont l’évaluateur et les personnes en charge des techniques et du personnel (RH…). En plus des précieuses données obtenues, cette visite permettra à l’évaluateur de mieux mettre en contexte les futures informations qu’il recevra.
POE – informer TOUS les occupants concernés par la démarche : la brochure
Pour diverses raisons (télétravail, temps-partiel, absence, réunion…), la visite ne permet pas de prévenir/sensibiliser/toucher, même informellement, l’ensemble des occupants du bâtiment.
Or, pour mobiliser le maximum de personne pour les prochaines étapes, il est plus qu’utile de réaliser une courte brochure explicative de l’intérêt pour tout un chacun.
À cet égard, undocument type a été réalisé. Celui-ci pourra servir de base à l’élaboration de votre document informatif ! C’est cadeau. 😉
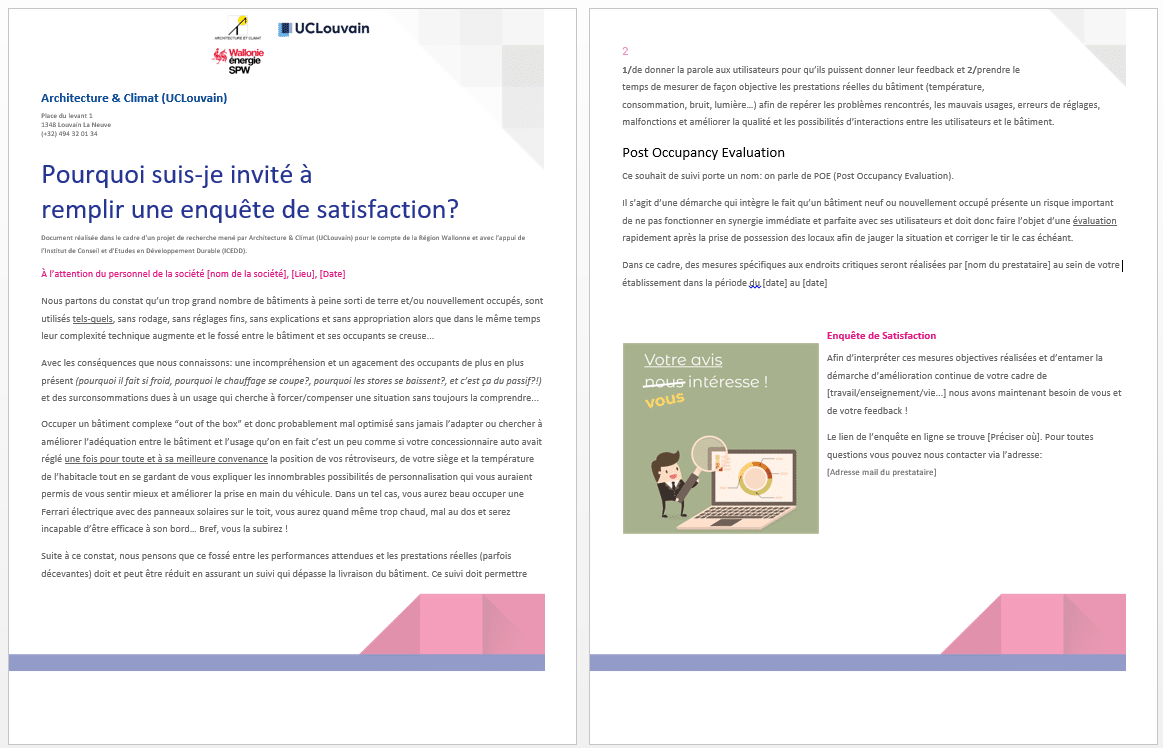
Cette brochure, permettra aussi d’alimenter les discussions autour de la machine à café dans les jours suivants : parler du bâtiment, ses atouts et défauts et, qui sait, déjà permettre aux occupants de découvrir au fil de leurs échanges des choses qu’ils ne savaient pas sur le fonctionnement du bâtiment ou encore des choses plus anodines au premier regard « Mais au fond, qui mets systématiquement les vannes thermostatiques sur 2 le matin ? ».
La brochure est aussi l’occasion de mettre des mots et un contexte autour de la démarche. Ceci devrait éveiller la curiosité de certains qui pourraient être tentés de d’ores et déjà se renseigner et préparer leur feedback.
Via la brochure, les occupants obtiennent également un lien de contact direct vers le prestataire externe à la société (téléphone ou Email) ce qui est de nature à rassurer et favoriser l’adhésion des occupants. En effet, si la démarche est positive, externe et neutre, l’employé de bureau, parfois moins à l’aise avec sa hiérarchie, pourra s’exprimer plus librement, éventuellement anonymement. Il y verra une vraie opportunité d’être acteur de l’amélioration de son cadre de travail.
Rappelons toutefois qu’au moment d’écrire ses lignes, ce marché est presque inexistant et que cette démarche peut tout à fait se dérouler en interne à condition que le processus puisse avoir lieu sereinement, sans générer de tensions, ce qui serait un échec. Les chances d’échec sont toutefois très faibles, car tout le monde sort gagnant d’une POE : un employé épanoui, bien au bureau et en bonne santé dans un bâtiment qui consomme moins est un employé productif dans un bâtiment aux charges réduites !
POE – Recueillir des informations : Le brainstorming
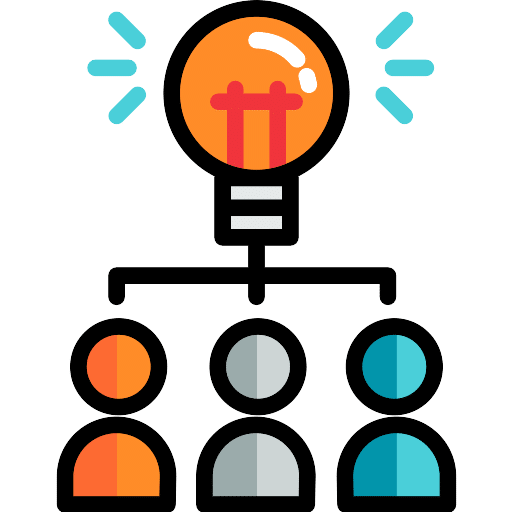
Le brainstorming est rapide et dynamique. Il permet de monter une petite délégation d’occupants que désire s’impliquer dans le processus évaluatif. Leur intégration permet ensuite de faciliter l’adhésion au processus pour les autres occupants. Le brainstorming est principalement utile avant et après l’enquête.
Avant, il permet à un nombre limité d’occupants volontaires, gestionnaires et responsables de s’exprimer librement et suggérer des questions supplémentaires et pertinentes à poser lors de l’enquête générale que l’évaluateur leur aura préalablement présentée. L’évaluateur profite également de cette première rencontre physique avec les occupants pour réexpliquer le sens et le but de la démarche ainsi que répondre aux éventuelles questions.
Le Brainstorming est également un outil génial d’analyse participative. Après l’enquête, l’évaluateur peut présenter les résultats bruts au groupe (éventuellement complétée par des interviews). En dévoilant les résultats, il permet de confronter les expériences et les expertises diverses d’un nombre limité de volontaires afin de comprendre les raisons et les causes de certains résultats de l’enquête. Cet outil permet ensuite de fixer collégialement de nouveaux objectifs à atteindre pour le futur en réaction au bilan de la POE.
POE – Recueillir des informations : L’enquête
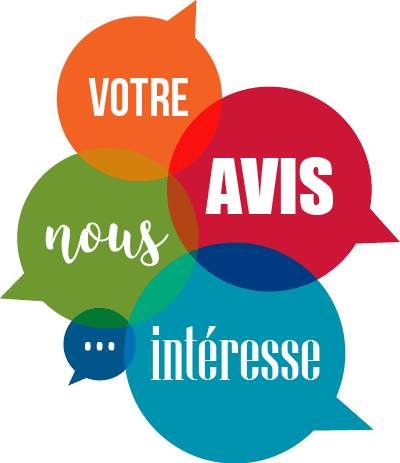
L’enquête est la méthode la plus systématiquement utilisée pour obtenir le feedback des occupants dans le cadre de la POE. L’enquête permet d’interroger un public large avec une panoplie de questions très variées pour un coût relativement réduit. Ce type de méthode permet en outre de comparer facilement les réponses des répondants entre eux dans le cas de questions fermées tout en laissant le champ libre aux commentaires là où une explication complémentaire est souhaitable.
Pour réaliser ce type d’enquêtes, vous trouverez plus d’informations sur la page dédiée !
POE – Recueillir des informations : le relevé, la mesure ponctuelle
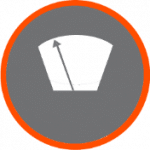
Le relevé consiste à mesurer à un moment précis, à un ou plusieurs endroits, plusieurs grandeurs qui suite à la visite, aux premiers échanges ou à l’enquête semblent pertinentes. (Qualité de l’air, humidité, qualité de l’éclairage…)
La mesure instantanée permet de récolter une information objective très rapidement, pour un coût réduit tout en étant beaucoup moins intrusive qu’un monitoring sur le long court.
Relever ou mesurer les données objectives du bâtiment à un instant « T » permet:
- De limiter la durée, l’intrusion et les sollicitations auprès des occupants.
- De mettre en regard le ressenti des occupants avec une mesure
- De détecter des anomalies ou des irrégularités importantes
- De cibler les éléments à monitorer plus en profondeur
- De conforter ou confronter l’occupant par rapport à son ressenti
Mais ne permets pas de comprendre l’enchaînement de certains phénomènes, ou d’avoir une vision générale sur les 4 saisons. La mesure ne vaut en effet que pour un certain instant, à un certain endroit, dans certaines conditions précises ; éventuellement biaisée par la présence de l’évaluateur (le gestionnaire qui remonte en vitesse le thermostat, l’employé que retire fissa le t-shirt qu’il avait coincé dans la ventilation ou encore le chauffage électrique d’appoint qu’il branche en cachette… (Véridique !).
POE – Recueillir des informations : Le monitoring
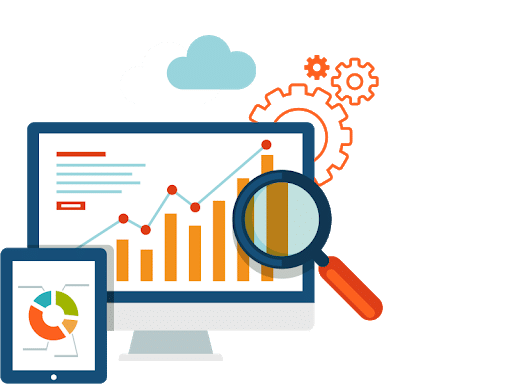
Contrairement au relevé ponctuel, le monitoring consiste à enregistrer un ou plusieurs types de mesures, dans un ou plusieurs endroits, à intervalles réguliers durant une période plus ou moins longue. Plus la durée est longue, plus l’intérêt et l’apprentissage que l’on pourra tirer des mesures seront importants.
Avec des mesures sur une semaine, on peut déjà se faire une idée :
- De l’inertie du bâtiment
- De la capacité de relance des systèmes après un weekend au ralenti
Avec des mesures sur un mois à trois moins on pourra en plus :
- Mieux comprendre l’évolution des ambiances au fil de la journée pour différentes conditions météo (ensoleillées, pluvieuses, venteuses, plus chaudes, plus froides)
- Détecter ce qu’il se passe les jours fériés
Et pour les monitorings d’un an ou plus, nous pourrons finalement :
- Découvrir ce qu’il se passe lors d’évènements plus exceptionnels (canicule, vague de froid, tempête…)
- Découvrir la vie du bâtiment selon les saisons
- Observer l’adéquation ou non du fonctionnement du bâtiment durant les périodes de moindre occupation (grandes vacances…)
Remarquer des tendances générales du bâtiment : la qualité de l’air se dégrade avec le temps (filtres ?), le bâtiment ne se met plus en régime réduit le weekend depuis une certaine date (réglage ?), les radiateurs peinent de plus en plus à atteindre la température souhaitée (entretien ? Panne ?)
Cette source riche d’information est plus complexe à mettre en place, demande une certaine préparation et un temps d’installation plus important.
Les instruments sont parfois visibles et enregistrent en « continu » les paramètres, ce qui peut parfois être ressenti comme intrusif par les occupants, et peut également biaiser leurs comportements. Ne se comporte-t-on pas différemment devant une caméra ? Et bien… Il en va de même face à un thermomètre qui enregistre nos petits excès !
Le principal défaut de cette méthode est donc son coût élevé et son caractère parfois intrusif. Il n’en demeure pas moins que cette méthode est extrêmement efficace.
Relever ou mesurer les données objectives du bâtiment en continu pendant une période plus ou moins longue permet:
- De ne pas passer à côté d’un évènement spécifique
- De mettre en regard le ressenti des occupants à chaque instant avec des mesures
- De détecter plus finement des anomalies ou des irrégularités
- D’identifier des moments critiques pendant l’année (canicule…), les tendances générales et les enchaînements. Ce qui aide beaucoup dans le diagnostic.
- De fournir plus d’information sur la cause éventuelle d’un problème de confort, de surconsommation…
- De permettre dans certains cas à l’occupant qui ressentirait une gêne ou un inconfort de (demander à) consulter ce que disent les instruments afin de l’aider à construire sa propre compréhension du bâtiment et de ses sensations. Cette compréhension sera utile pour poursuivre la démarche d’amélioration du bâtiment lors de prochains brainstormings, interviews, enquêtes…
POE – Recueillir des informations : L’interview
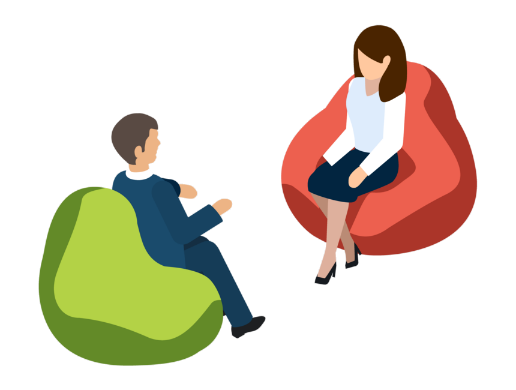
L’interview d’occupants et autres acteurs de la vie du bâtiment est également un excellent outil pour aider l’évaluateur à mettre en contexte les résultats obtenus.
Elle permet principalement de donner la parole à certaines personnes sur des sujets précis après la réalisation de l’enquête afin de nuancer et de mieux comprendre ce qui se cache derrière certains résultats peu détaillés. Bien que les champs libres de l’enquête permettent déjà de mettre les réponses en perspective, l’enquête – en raison de son format – n’est pas toujours le support le plus propice pour apporter des éléments de contexte et de la nuance.
En fonction des résultats de l’enquête et des présuppositions de l’interviewer sur les réponses à chercher, l’interview peut-être plus ou moins dirigée. Soit le fil des questions est rigoureusement préparé et on s’y tient, soit l’interviewer dispose d’une liste de question sans ordre précis pour nourrir le débat ; il se contente alors de rebondir en fonction des réponses reçues. Cette dernière façon de faire permet à l’interlocuteur de se sentir libre dans son expression tandis que l’interview plus rigoureuse permet à l’évaluateur d’obtenir une réponse claire et structurée à ses questions.
De façon moins dogmatique, dans la plupart des cas, une interview en deux phase : d’abord cadrée puis libre permet d’offrir le meilleur des deux mondes. Mais il vaut mieux respecter cet ordre sous peine de ne pas arriver à recadrer l’interview.
De cette façon, l’évaluateur se concentre d’abord sur ses questions préparées et permet à l’interlocuteur d’être guider, de trouver ses marques dans la discussion, se mettre à l’aise. Quand l’évaluateur à l’esprit libéré de ses questions et que l’interlocuteur a pris ses repères, l’interview peut alors, et seulement à ce moment-là, sortir de son cadre et évoluer naturellement, plus informellement en fonction des préoccupations de l’occupant sur lesquels l’évaluateur ne manquera pas de réagir.
Dans tous les cas, une interview :
- Permet d’obtenir une information précise, circonstanciée et complète.
- Prends énormément de temps : entre la préparation, l’interview, la retranscription, la synthèse…
- Est sujette à plus d’émotion, implication et donc des éventuelles minimisations ou exagérations.
- Ne permet pas un feedback représentatif : Tout le monde n’est pas égal face à ce type d’échange, certains prendront plus de place que d’autre ou pourraient se montrer plus persuasifs que d’autres.
POE – Recueillir des informations subjectives en continu : Le journal de bord de l’occupant
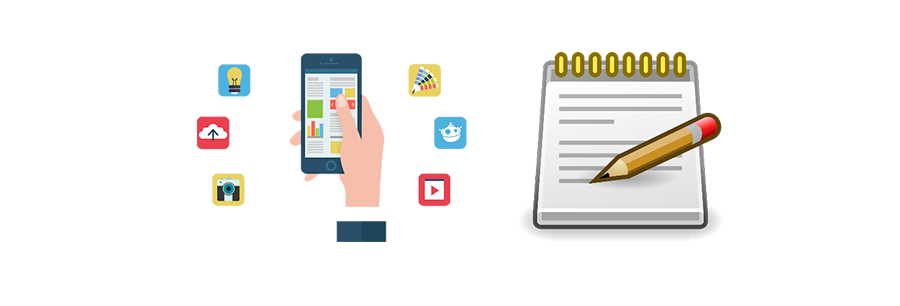
De la même façon que pour les relevés des sondes : le ressenti des occupants peut se recueillir : soit à un moment précis en faisant éventuellement appel aux souvenirs pour parler de ressentis passés (dans le cas d’une enquête ou d’une interview), soit en continu, tout au long de l’année.
Pour se faire, le support peut varier : en ligne via un document ou une application ou sur papier dans un agenda ou un cahier dédié. Éventuellement, si des réunions d’équipe régulière intègrent la démarche, le rapportage pourrait être oral avant d’être retranscrit dans un PV.
La dynamique peut quant à elle être de deux natures : soit l’occupant le fait de son côté lorsqu’il a des choses à noter [« Jeudi 28/01/2020 à 14h32 : il fait vraiment chaud dans les couloirs, pourtant dehors il gèle »] et en fin de trimestre ou d’année, au passage de l’évaluateur ou d’un groupe d’occupants qui assure le relais vers l’évaluateur, ces notes sont partagées. Soit ce rapportage fait partie de la dynamique de groupe et est systématiquement mis à l’ordre du jour des réunions d’équipe régulières avant de finir dans des PVs.
Le choix de la manière dépendra fortement d’un établissement à l’autre, en fonction de la philosophie et des dynamiques internes. La méthode individuelle demande plus de travail, mais permet de conserver des informations plus brutes et personnelles des sensations. À l’inverse, la méthode de groupe demande moins de travail, mais le regard des autres peut tronquer notre façon de restituer ou non notre (in)satisfaction. L’influence de la manière avec laquelle le rédacteur du PV va résumer, paraphraser et agréger ces informations n’est également pas à négliger.
Il reste que cette méthode propose un coût réduit et permet d’obtenir des informations très précises tout au long de l’année. Le revers de la médaille est évidemment la forte sollicitation demandée aux occupants et/ou au rédacteur des PVs. Cette forte sollicitation devra être souhaitée par les occupants au risque de perdre l’adhésion et la motivation pour le processus entier.
Pour conserver une bonne dynamique, il faudra, et c’est primordial que les occupants qui partagent régulièrement leur ressenti aient des feedbacks réguliers.
Pour résumer : demander aux occupants de noter à intervalles réguliers ou à chaque « évènement » son ressenti sur divers aspects permet à moindre coût de récupérer une information précieuse. Cela permet:
- De ne pas passer à côté d’un évènement spécifique
- D’éviter d’être biaisé par ses souvenirs, mais de s’en tenir à la somme des ressentis du moment.
- D’impliquer les occupants, mais attention à la surcharge.
- La mise en regard de ces informations avec un monitoring des ambiances et des installations est la méthode la plus complète et précise pour évaluer le bon fonctionnement de l’occupation d’un bâtiment … Mais aussi la plus difficile à mettre en place.