Constat : la cogénération fonctionne très peu d’heures !
Lorsque la cogénération fonctionne un nombre d’heures nettement inférieur à ce que l’étude de faisabilité de cogénération prévoyait, on s’en rend compte souvent trop tard lorsque la période de garantie est terminée. En effet, il faut régulièrement tabler sur un voire un an et demi pour pouvoir établir la rentabilité énergétique, environnementale et financière de l’ensemble de la chaufferie, en ce compris la cogénération. Malgré tout, un diagnostic doit être réalisé. En effet, le problème peut être mineur et facile à résoudre.
Voici quelques pistes de pré-diagnostic avant de faire appel à l’installateur initial ou à un bureau d’étude en audit énergétique.
On pointera principalement :
- Les profils des besoins de chaleur et d’électricité sont différents de ceux imaginés lors de l’étude de faisabilité.
- La régulation de chaque équipement et de l’ensemble de la cascade des équipements, à savoir :
- l’ordre de priorité de la cogénération par rapport à la ou les chaudières ;
- la régulation individuelle de la cogénération ;
- la régulation individuelle de chaque chaudière.
- L’hydraulique de l’installation.
Évolution des profils des besoins
Le temps entre l’étude de faisabilité et la mise en service d’une installation de cogénération peut être important dans certains cas. En effet, pendant cette période, les profils des besoins de chaleur et d’électricité peuvent changer. Le gestionnaire de bâtiments peut très bien mener des actions URE, voire entreprendre des actions importantes :
- d’isolation des parois, de la toiture, … ;
- de remplacement de vitrage simple par des doubles vitrages à basse émissivité ;
- de récupération de chaleur sur la ventilation hygiénique ;
- de limitation des consommations d’eau chaude sanitaire ;
- de réduction des consommations électriques sur l’éclairage, la bureautique, les moteurs de ventilation, … ;
- …
C’est vrai que l’on (doit ?) peut tenir compte des actions URE dans les études de faisabilité ! Mais il reste difficile d’évaluer exactement dans quelle proportion les profils de consommations vont évoluer.
Toujours est-il que c’est une des causes possibles de manque de rentabilité énergétique de la cogénération. En effet, une diminution des besoins de chaleur fera en sorte que la cogénération s’arrêtera plus rapidement avec pour effet retardé de réduire le nombre d’heures de fonctionnement sur une année.
Pour pouvoir objectiver la part de réduction due aux actions URE, il est nécessaire d’avoir mis une comptabilité énergétique performante sur base des relevés des compteurs de chaleur et électriques.
Régulation et commande des équipements
Régulation de l’ensemble
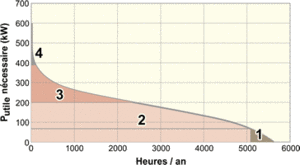
Dans l’association d’une cogénération avec une ou plusieurs chaudières, l’objectif, comme on l’a déjà précisé, est que la cogénération fonctionne un maximum d’heures sur l’année. Elle devrait donc être « en tête » de cascade ! Attention toutefois qu’une cogénération ne peut, en général, moduler qu’entre 60 et 100 % de son taux de charge thermique. En dehors des périodes de fonctionnement de la cogénération dans sa zone de modulation en puissance, il est nécessaire d’assurer les besoins de chaleur par les chaudières.
Suivant le schéma ci-dessus on établit la logique de cascade suivante :
Zone 1
Pour un besoin inférieur à 24 % de la puissance totale, ce sont les autres chaudières qui doivent être en « tête » de cascade. Si la chaufferie est équipée d’une chaudière à condensation, pour autant qu’elle soit dans des bonnes conditions de condensation, c’est elle qui doit assurer le besoin de chaleur. Avec sa capacité à moduler de 10 % à 100 % de son taux de charge, avec un excellent rendement à faible charge, la chaudière à condensation est tout indiquée.
Zone 2
Dans la plage de 24 à 40 % de la puissance totale nécessaire, la cogénération doit fonctionner en permanence. Si ce n’est pas le cas, le premier réflexe est de regarder au niveau de la régulation propre à la cogénération.
Zone 3
Pendant les périodes de grands froids, la cogénération ne sera pas suffisante pour assurer les besoins de chaleur du bâtiment considéré. Il sera nécessaire de lui adjoindre une chaudière afin de lui donner le « coup de pouce sauveur ». Cette opération est délicate en fonction du type de chaudière qui vient faire l’appoint. Un développement trop important de puissance de la part de la chaudière peut faire en sorte que la cogénération s’arrête.
Pour différents besoins de chaleur, on peut évaluer si la cascade est correcte. Naturellement, il est nécessaire de choisir correctement les périodes pendant lesquelles on peut évaluer le fonctionnement de la régulation générale. Pendant ces périodes, sur base de la logique de régulation de cascade et en la croisant avec le taux de charge des différents équipements, on peut évaluer la bonne régulation de l’ensemble :
- En mi-saison et en début d’été, le régulateur général doit privilégier la ou les chaudières à condensation. Si le régulateur général affiche la valeur de puissance des chaudières, une bonne régulation donnera un taux de charge (Puissance affichée / Puissance nominale de la ou des chaudières) compris entre 10 et 24 % de la puissance totale.
- En hiver, lorsque la température externe n’est pas trop froide, la cogénération doit fonctionner seule. Une régulation correcte donnera un taux de charge (Puissance affichée / Puissance nominale du cogénérateur) compris entre 24 et 40 % de la puissance totale.
- En période très froide, le taux de charge du cogénérateur doit être de 100 % pendant de longue période de fonctionnement et le taux de charge d’une voire deux chaudières comprit entre 10 et 100 %.
Régulation interne de la cogénération
La régulation interne de la cogénération est assez complexe en soi. Sans rentrer dans les détails, on donne ici quelques pistes de réflexion. Le nombre d’heures de fonctionnement et le nombre de démarrages de la cogénération associée à un ballon tampon peut être influencé par la régulation :
- Selon le rapport entre le besoin instantané de chaleur (en kWth) et la puissance nominale de la cogénération en dessous duquel la cogénération reste à l’arrêt. Pratiquement, cette régulation s’exprime par sa capacité à gérer la modulation de puissance thermique de la cogénération. Une cogénération classique peut en général avoir une modulation de puissance entre 60 et 100 %.
- Du taux de charge du ballon associé. En dessous d’une certaine valeur de taux de charge maximum, la cogénération module en puissance. Plus ce taux de charge maximum est élevé, plus la cogénération commence à « pomper » (marche/arrêt important). Ce qui nuit naturellement à longévité du cogénérateur.
Des indicateurs de bon fonctionnement de l’ensemble ballon tampon/cogénérateur sont :
- Un écart de température entre le bas et haut du ballon suffisant pour permettre une modulation de puissance de la cogénération (de l’ordre de 20 K), autrement dit, une bonne stratification du ballon.
- Pour éviter le pompage de la cogénération :
- un différentiel suffisant entre la température donnée par la sonde du haut du ballon et la valeur de consigne de redémarrage de la cogénération (de l’ordre de 5 K) ;
- un différentiel suffisant entre la température donnée par la sonde du bas du ballon et la valeur d’arrêt de la cogénération (de l’ordre de 5 K) ;
En première approche, on pourrait conseiller aux gestionnaires, lorsque la cogénération fonctionne seule, (période pas trop froide), d’évaluer de manière régulière le temps de fonctionnement de la cogénération et surtout le nombre d’arrêts- redémarrages, de démarrage :
- un nombre trop important de démarrages ;
- un temps de fonctionnement court ;
- une mauvaise stratification dans le ballon ;
- …
devront décider les gestionnaires à faire appel soit à l’installateur, à la société de maintenance ou soit à un auditeur.
Régulation individuelle des chaudières d’appoint par rapport à la cogénération
Lorsqu’une ou plusieurs chaudières existantes sont en appoint de la cogénération, les régulations individuelles de chaque chaudière doivent être adaptées par rapport au cogénérateur. Souvent, on observera que lorsque le besoin de chaleur devient supérieur à la puissance thermique des cogénérateurs, on démarre une chaudière d’appoint sans modulation de puissance au niveau du brûleur. Le « boost » de puissance de la chaudière va tout de suite « affoler » la régulation du cogénérateur qui risque de s’arrêter rapidement. Il en résulte un risque non négligeable de « pompage » de la cogénération altérant ainsi :
- la rentabilité de la cogénération ;
- la durée de vie de la cogénération tout en augmentant le risque de panne.
Immanquablement, la chaudière d’appoint devra démarrer :
- pour les anciens modèles en petite flamme ;
- pour les modèles récents au minimum de la plage de modulation (à 10 % pour une chaudière à condensation par exemple).
Hydraulique de l’installation
Le regroupement des équipements de production de chaleur en amont du collecteur principal est primordial pour que le fonctionnement conjoint des chaudières et des cogénérateurs permette une optimisation énergétique de l’ensemble.
Une source de perturbation que l’on peut rencontrer sur des installations existantes est le placement d’une cogénération sur un départ/retour existant du collecteur. C’est en général la solution de facilité pour les raisons suivantes :
- La modification hydraulique est réduite.
- Il n’y a pas d’interruption dans le fonctionnement de l’installation de chauffage. Dans le cas où, par exemple, l’installation de chauffage doit produire en permanence de l’ECS. C’est le cas dans les hôpitaux où l’installation d’ECS n’a pas sa production propre. Ceci dit, il est toujours possible de trouver un compromis.
Les conséquences de cette configuration pourraient être les suivantes :
- problème d’équilibrage des circuits;
- difficulté de réguler correctement l’association des chaudières avec les cogénérateurs.
Dans ce cas de figure, il y aura lieu de reconsidérer l’hydraulique en faisant appel à un auditeur spécialisé.
Exemple de configuration délicate :
Le schéma ci-dessous montre que l’installation du cogénérateur s’est réalisée à postériori. Probablement parce qu’un départ/retour était disponible en bout de collecteur, le circuit de l’installation de cogénération a été placé à l’opposé de la production de chaleur des chaudières.
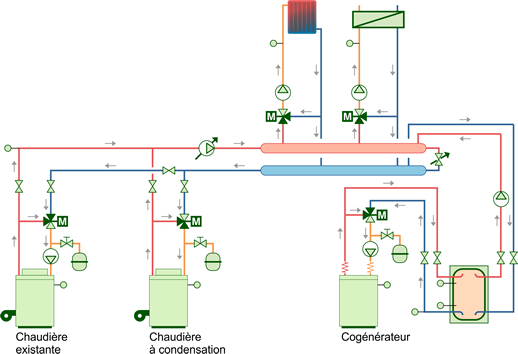
Exemple de configuration correcte :
On voit ci-dessous que le cogénérateur et les chaudières sont placés d’un même côté par rapport à la distribution de chaleur.
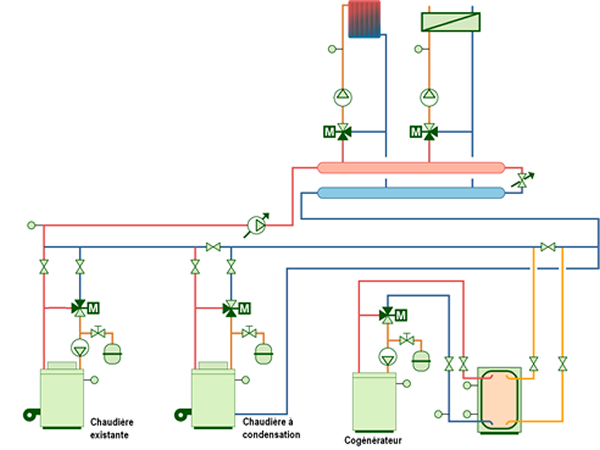
S’assurer que les retours sont froids
Lorsque la chaudière d’appoint est une chaudière à condensation, en période de grand froid la cogénération fonctionnera en même temps que la chaudière à condensation. L’hydraulique de l’installation a toute son importance dans le sens où le retour d’eau chaude vers la chaufferie doit être :
- le plus froid possible pour favoriser la condensation de la chaudière à condensation ;
- adapté aux spécifications de température de retour minimale exigées par le constructeur de cogénération.
On se retrouve ici dans le même cas de cohabitation que celui de chaudières classiques avec une chaudière à condensation, avec une différence de taille : c’est la cogénération qui doit fonctionner un maximum d’heure par an et accessoirement la chaudière à condensation qui doit condenser en support de la cogénération en période froide ou en remplacement de la cogénération lorsque celle-ci ne fonctionne pas.
Cependant, énergétiquement parlant, l’idéal est que l’hydraulique soit conçue pour favoriser à tout moment des retours froids quitte à le réchauffer par un by-pass au niveau des chaudières classiques et du cogénérateur. L’inverse ne fonctionne pas !
Ce cas de figure peut arriver lorsqu’une chaudière classique, faisant partie d’un ensemble chaudières classiques/cogénération a été remplacée par une chaudière à condensation sans modification de l’hydraulique. Dans cette configuration, il y a des chances pour que la chaudière à condensation en appoint de la cogénération ne puisse pas condenser.
On pointera principalement :
- un collecteur bouclé ;
- une bouteille casse-pression pas ou mal régulée;
- …