Description du principe
La technologie des PAC sur boucle d’eau s’établit autour des trois composantes du système :
- les PAC ou climatiseurs réversibles (Eau/Air) assurent le chauffage ou le refroidissement des locaux suivant les besoins thermiques de ceux-ci,
- la boucle d’eau, circuit d’eau fermé raccordé aux climatiseurs réversibles et aux échangeurs de chaleur, assure la circulation d’énergie thermique dans le bâtiment,
- une chaudière et une tour de refroidissement assurent le maintien en température de la boucle d’eau en apportant ou en évacuant les calories suivant le bilan thermique global du bâtiment.
La boucle d’eau assure ainsi le transport d’énergie entre l’ensemble des locaux et le transfert de chaleur des zones aperditives du bâtiment (zones internes, salles de réunion, locaux informatiques, locaux sur façade ensoleillée) vers les zones déperditives (locaux périphériques, locaux sur façades à l’ombre).
Elle permet donc d’effectuer en permanence le calcul simultané des besoins thermiques globaux du bâtiment et, en contrôlant sa température, de puiser ou de rejeter, sur l’extérieur, l’énergie nécessaire à l’équilibre thermique de l’immeuble.
Consommation
Comme tout système avec échangeur direct (l’air du local passe directement dans l’évaporateur), la très basse température de l’échangeur génère un supplément de consommation non négligeable lié à la déshumidification de l’air ambiant (à ce titre, le ventilo-convecteur dont l’échangeur est dimensionné sur base d’un régime 12 °C – 17 °C est nettement plus performant).
L’évacuation des condensats est d’ailleurs un point délicat. Si elle ne peut être gravitaire, elle est confiée à une pompe de relevage intégrée dans l’appareil. Généralement, les pompes prévues par le constructeur sont moins bruyantes que celles ajoutées sur place par l’installateur. Autant donc le prévoir dès la sélection de la machine.
Régulation
Au niveau des pompes à chaleur, une zone neutre de 2 à 3 °C doit être prévue dans la consigne entre chauffage et refroidissement.
Un commutateur manuel peut permettre à l’utilisateur de sélectionner la vitesse de rotation du ventilateur (et donc le niveau de bruit qu’il accepte de subir !)
Mais c’est au niveau de la boucle que la régulation doit être la mieux étudiée pour optimaliser la performance énergétique. Plusieurs scénarii sont possibles. Par exemple, on peut laisser flotter la température entre 18 et 32 °C (autrement dit, la chaudière s’enclenche sous les 18 °C et la tour s’enclenche au-dessus des 32 °C). La récupération de chaleur entre locaux demande d’ailleurs un large différentiel, mais il ne faut pas pour autant pénaliser le COP des machines ! En plein hiver et en plein été, il faudra étudier quelle est la température qui optimalise au mieux l’ensemble.
Ainsi, si on diminue l’écart entre ces 2 seuils d’enclenchement, le COP des pompes à chaleur sera amélioré, mais la consommation énergétique au niveau central sera accrue.
Exemple.
Dans la galerie commerciale, il est possible que les locaux doivent être réchauffés le matin (relance après la nuit) et refroidis l’après-midi suite à l’éclairage et à l’occupation. Idéalement, c’est alors l’inertie de la boucle qui devrait jouer, inertie renforcée par un ballon de stockage placé en série sur la boucle.
Durant l’après-midi, les machines frigorifiques chargent la boucle et son stockage. Le lendemain, en fin de nuit (pour profiter du tarif de nuit plus avantageux), les locaux sont remis en température avant l’arrivée des occupants… et le stockage est déchargé, sans consommation de la tour.
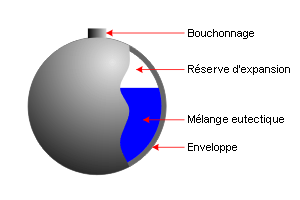
À noter : pour réduire l’encombrement du ballon de stockage, on peut envisager de le remplir avec des nodules eutectiques dont la température de solidification se situe dans la zone neutre de fonctionnement de la boucle.
|
Si un de nos lecteurs dispose d’une installation de ce type dans son bâtiment, nous serions heureux de participer à la mise au point de la régulation de ce système et de pouvoir en transcrire ici les résultats, en vue d’une prochaine version d’Énergie+ ! Notre adresse électronique est la suivante : energieplus@uclouvain.be.
Domaine d’application
D’une manière générale, ce système est adapté aux bâtiments dont on prévoit que les charges thermiques seront en opposition (façades d’orientation différentes). On pense tout particulièrement aux bâtiments ayant des salles aveugles avec fort taux d’éclairage, forte occupation, … et à la fois des locaux en façade Nord avec fortes déperditions (fort taux de vitrage).
Il permet une régulation individualisée. Il permet une sensibilisation de l’utilisateur final puisque la consommation propre des PAC installées dans ses locaux peut lui être facturée.
Mais il ne contrôle pas l’hygrométrie de l’air du local. La nuisance acoustique est parfois importante. Et l’utilisation d’énergie électrique aux heures pleines reste coûteuse.
De plus, aujourd’hui il entre en concurrence avec le système à « Débit de Réfrigérant Variable », (qui lui même dans une de ses variantes peut aussi comporter une boucle d’eau reliant les différentes unités extérieures).
Ce système est fréquemment utilisé dans les centres commerciaux. Chaque local est livré nu de tout équipement, sinon de la présence de la boucle et de raccordements en attente. Le commerçant investit dans une ou plusieurs machines réversibles et « pompe » le chaud ou le froid qu’il souhaite sur la boucle. On peut facilement mesurer la part individuelle de la consommation de chaque appareil dans le bilan total.
Étude de cas
Dans une galerie commerciale de Liège, un très gros circulateur à vitesse variable avait été mis sur la boucle d’eau. Sa régulation se faisait classiquement en fonction de la pression d’eau du réseau. Or les échangeurs des pompes à chaleur sont toujours alimentés à débit constant pour éviter le gel des évaporateurs. Donc l’eau tournait à grande vitesse et le Delta T° sur la boucle était seulement de 2 K, départ-retour.
Il a été imaginé de moduler la vitesse de rotation du circulateur en fonction du maintien d’un Delta T° de 6 K. Ainsi, si la demande augmente, le delta de T° augmente et la vitesse est adaptée. La température est maîtrisée et le gel est impossible.
Une chute drastique de la consommation électrique en a résulté.
|
Avantages du système
- Régulation de température individualisée.
- Conception simple, relativement facile à mettre en œuvre.
- Système intéressant du point de vue énergétique en intersaison ou plus exactement lorsque les charges dans les différents locaux sont opposées et que la boucle est proche de l’équilibre thermique.
- Les PAC sont relativement fiables à condition de respecter les débits d’air et d’eau.
- Extension facile de l’installation.
- Facilité d’installation, de démontage et de réemploi des PAC suivant l’occupation des locaux ou des réparations.
- Sensibilisation de l’utilisateur final aux économies, car il supporte directement les frais électriques liés au fonctionnement des PAC installées dans ses locaux.
- Réduction de la puissance de la production thermique centralisée.
Désavantages
- Pas de contrôle de l’hygrométrie de l’air du local.
- Problème de niveau sonore : puissance acoustique non négligeable, donc nécessité de traitement spécifique.
- Besoin de raccordement des condensats vers l’égout.
- Les économies sont relativement modestes. Les PAC consomment essentiellement de l’énergie électrique au qui ne peut être différée en heure creuse.
- Le risque de panne ou d’intervention sur la boucle d’eau, sur les dispositifs centralisés, rend le système inquiétant pour les utilisateurs de climatisation critique (locaux informatiques, salles de fabrication…). Cette crainte conduit à séparer ces installations de l’installation principale ou à en dédoubler les équipements en cas de problèmes.
Choix des PAC réversibles
Ces PAC se présentent essentiellement sous trois formes :
- Le modèle console en allège, installé contre les murs extérieurs, de préférence sous la fenêtre : il peut être carrossé ou bien intégré dans un habillage de façade ; il doit être installé dans le local à traiter et l’habillage de l’appareil doit faire l’objet d’un renforcement acoustique.
- Le modèle plafonnier horizontal, installé généralement en faux plafond : il est conseillé d’installer la PAC à l’extérieur du local à traiter (circulation de bureau par exemple) et d’assurer le raccordement au diffuseur de soufflage par l’intermédiaire de gaines isolées thermiquement et phoniquement.
- Le modèle vertical type armoire, installé dans un placard technique : un réseau de gaines de soufflage et éventuellement de reprise, assure la liaison entre la PAC et le local à traiter.
L’installation doit permettre de maintenir un accès aisé à l’appareil pour les opérations d’entretien. Les opérations de maintenance courantes consistent en nettoyage ou remplacement des filtres (opérations pouvant être effectuées par du personnel non qualifié).
Les opérations d’entretien, de réparation ou de remplacement de composant électrique (principalement le moteur du ventilateur de soufflage) sont possibles depuis les panneaux d’accès démontables.
En cas d’intervention sur le circuit frigorifique, il est recommandé de procéder à un échange standard de l’appareil et d’assurer la réparation en atelier.
La sélection doit être faite en fonction des besoins thermiques des locaux et de leur application. Il est souvent préférable de sélectionner un appareil d’une puissance légèrement inférieure aux besoins déterminés pour les conditions les plus défavorables; cela permet une meilleure adaptation de la puissance à la charge thermique moyenne à combattre et allonge les durées des cycles de fonctionnement de l’unité en évitant des inversions de cycle trop fréquentes.
Enfin, un réseau d’évacuation des condensats est à raccorder sur chaque appareil.
On sera attentif à la bonne isolation phonique du compresseur puisqu’il est ici situé dans le local !
Il existe des versions en apparent et des versions destinées à être insérées dans un habillage (en allège ou en faux plafond). S’il peut être placé dans un local technique attenant et relié au local par une gaine, l’installation sera nettement moins bruyante. La maintenance en sera également facilitée.
On veillera tout particulièrement à éviter la transmission des vibrations de l’appareil au bâtiment par l’usage de silentblocs ou de semelles antivibratiles. L’usage de raccordements flexibles est également favorable sur le plan acoustique et facilitera le démontage de l’appareil (prévoir des vannes d’isolement étanches).
Choix de la boucle d’eau
La boucle d’eau doit être un circuit d’eau fermé, préféré à un circuit d’eau ouvert en raison des problèmes d’embouage, d’entartrage et de corrosion. Ce circuit d’eau à température tempérée (15 °C à 35 °C environ) reçoit les composantes suivantes :
- Les pompes de circulation prévues, l’une en fonctionnement normal, l’autre en secours, afin d’éviter tout risque de panne totale.
- Une filtration de l’eau à réaliser au niveau des pompes de circulation et près des climatiseurs.
- Un échangeur d’évacuation des calories, généralement du type échangeur à plaques, équipé d’un by-pass permettant les opérations de nettoyage, raccordé à un réseau d’eau de refroidissement.
- Un réchauffeur d’eau équipé d’un by-pass.
- Un réseau de distribution en tubes d’acier noir non calorifugé (sauf à l’extérieur); néanmoins la T°C modérée de l’eau permet l’utilisation de tuyauteries en PVC.
- Des vannes d’isolement et d’équilibrage du réseau et, notamment, pour chaque raccordement à un climatiseur; ce raccordement sera réalisé en tuyauterie flexible facilitant l’installation, évitant les transmissions de vibrations et simplifiant les opérations de maintenance.
- Des accessoires tels que vases d’expansion, vannes de vidange et systèmes de purge d’air (manuel et automatique), ainsi qu’un système d’appoint d’eau.
Choix de l’échangeur « froid »
L’échangeur froid doit permettre l’évacuation des calories excédentaires de la boucle d’eau. Différents systèmes sont utilisés :
- Raccordés à la boucle d’eau par l’intermédiaire d’un échangeur à plaques, on trouve fréquemment des tours de refroidissement à circuit ouvert ou un réseau d’eau de pompage dans la nappe phréatique, dans la mer, une rivière, un lac,…
- Raccordés directement à la boucle d’eau, on utilise des tours de refroidissement à circuit fermé ou des appareils appelés « dry-cooler ».
Le choix entre ces différents appareils s’établit en fonction de leur existence (eau de mer, nappe phréatique…), des critères dimensionnels (tours de refroidissement ouvertes ou fermées) et des contraintes acoustiques.
Il faut noter que l’utilisation de « dry-cooler » nécessite de relever la température de la boucle d’eau en été à 40 °C environ, ce qui oblige à l’emploi de PAC adaptées.
Choix de l’échangeur « chaud »
Il doit permettre d’apporter les calories nécessaires au maintien en température de la boucle d’eau. Les sources de chaleur pouvant être utilisées sont variées :
- chaufferie alimentée au gaz ou au fuel
- sous-station de chauffage urbain
- PAC Air/Eau sur l’air extérieur
L’utilisation d’un échangeur de transfert d’énergie n’est pas forcément nécessaire lors de l’utilisation de chaufferies ou de sous-stations de chauffage urbain.
L’utilisation d’une nappe phréatique nécessite de descendre le niveau de T°C de la boucle d’eau, en hiver, à 12 °C environ, ce qui oblige à l’emploi de PAC adaptées et de calorifuger tout ou partie du réseau de distribution.
On trouvera dans le Tome 4 de la collection Climatisation et conditionnement d’air de J. Bouteloup différents schémas de montage des installations.