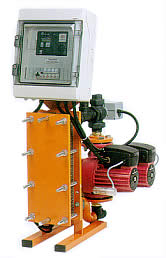
Échangeur à plaques instantané
Technologies
Un échangeur instantané à plaques est, par définition, un préparateur d’eau chaude sans capacité de stockage. C’est l’eau du réseau de chauffage (en provenance de la chaudière) qui chauffe l’eau sanitaire dans un serpentin tubulaire, au moment des besoins.
Les capacités de chauffage sont fabuleuses… pour autant que la chaudière suive !
Exemple.
Pour un débit au primaire de 14 m³/h au régime 90/45°C, on peut réchauffer environ 230 litres par minutes, de 10 à 55°C. Mais la puissance chaudière doit être de : 14 m³/h x 1,16 kWh/m³ x (90 – 45) = 730 kW ! Soit l’équivalent de la puissance de chauffage de 30 habitations domestiques… Et l’alimentation hydraulique doit suivre entre la chaudière et l’échangeur. |
De plus, la régulation doit être très souple pour suivre instantanément les variations de la demande. De là, l’adjonction fréquente d’un ballon tampon :
Pour résoudre à la fois ce besoin élevé de puissance et cette régulation sensible, on greffe un ballon tampon sur le secondaire de l’installation.
Échangeur extérieur à la chaudière
On rencontre généralement des serpentins tubulaires en cuivre ou des échangeurs à plaques. Ces échangeurs comportent souvent des tôles déflectrices formant chicanes, dispositifs servant à améliorer les échanges des deux circuits d’eau.
Le raccordement se fait sur l’aller du circuit de chauffage, comme tout corps de chauffe.
Échangeur incorporé à la chaudière
Si la capacité de la chambre d’eau est suffisamment importante, on l’utilise parfois comme échangeur de chaleur.
Les branchements sur la chaudière sont alors réalisés de telle façon qu’en hiver, lorsqu’il y a soutirage d’importantes quantités d’eau chaude sanitaire, c’est toute la puissance de la chaudière qui serve au réchauffage de cette eau. On parle de régulation en « eau chaude sanitaire prioritaire ».
Avantages et inconvénients
Les avantages
Les avantages d’une préparation instantanée sont liés à l’absence de stockage :
- Le faible encombrement.
C’est un argument-clef si la place disponible est particulièrement réduite.
- La faible charge au sol.
C’est un argument si la chaudière est prévue sous toiture.
- L’absence de pertes par stockage.
Cet argument tend à devenir négligeable, vu l’isolation poussée des ballons récents.
- La bonne performance hygiénique.
L’eau chaude ne stagnant pas dans le préparateur, les risques de propagation de la légionelle sont réduits. - Le faible coût d’investissement.
Cette technique est relativement peu onéreuse à installer.
Les inconvénients
Les inconvénients du préparateur instantané sont plus nombreux :
- La fluctuation de la température de l’eau au niveau de l’utilisateur.
Malgré une régulation fine (PID) (à prévoir absolument), on reste limité par le temps de réponse des éléments mécaniques de l’installation qui rend les fluctuations inévitables. Il est déconseillé d’utiliser ce type de système dans un bâtiment ayant un profil de puisage discontinu.
- Le rendement de production dégradé de la chaudière.
Avec une chaudière combinée chauffage-ECS, il est indispensable de maintenir la chaudière en permanence à température élevée (min 70°C) pour garantir un temps de réponse minimum lorsqu’une demande apparaît. Ceci interdit une régulation en température glissante des chaudières et n’est donc pas optimum énergétiquement, principalement avec les anciennes chaudières ou même avec des chaudières gaz atmosphériques récentes dont les pertes à l’arrêt sont importantes.
- Le fonctionnement du brûleur en cycles courts.
Étant donné l’absence de réservoir tampon, chaque puisage va entraîner la mise en route de l’installation pour des temps très courts. Les temps de fonctionnement du brûleur seront donc brefs, ce qui est défavorable pour le rendement de combustion et la pollution atmosphérique.
- La puissance élevée du générateur.
La production instantanée demande généralement une puissance de générateur très importante. Dans le cas d’une production d’ECS combinée au chauffage, il peut être nécessaire de surdimensionner la chaudière uniquement pour l’ECS. Ce qui serait une mauvaise utilisation de l’investissement consenti.
- La puissance des circulateurs.
La perte de charge des échangeurs instantanés demande des pompes plus puissantes dont la consommation électrique n’est pas à négliger.
- L’entartrage.
La température élevée au niveau des surfaces d’échange conduit à la formation rapide de tartre (inconvénient limité par l’action de la vanne trois voies qui évite que la température au primaire de l’échangeur soit en permanence à la valeur maximale).
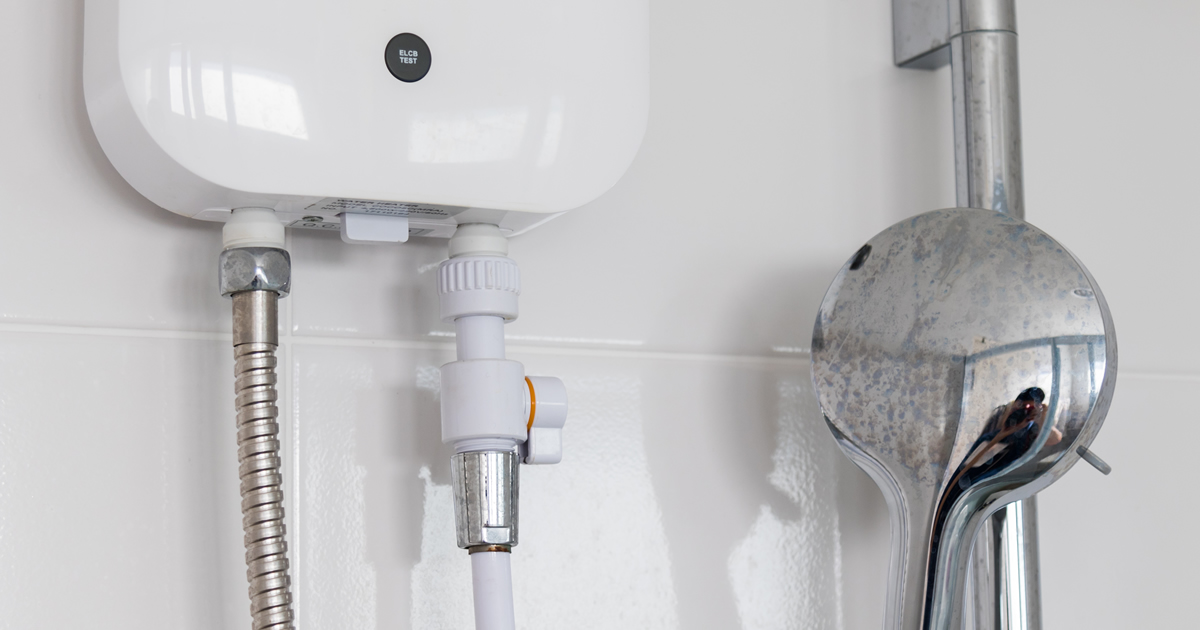
Préparateur d’eau chaude instantané
Technologie du préparateur électrique
En pratique, l’échangeur instantané électrique ne se rencontre pas (ou rarement) dans le secteur tertiaire. La puissance qu’il requiert est en effet trop importante.
Exemple.
Imaginons un préparateur instantané électrique alimentant 3 douches. Il se peut que les 3 douches fonctionnent simultanément. Le préparateur devra dès lors fournir 3 x 10 litres/min à 45°. Ces 30 litres/min correspondent à un débit de 1 800 litres/heure. La puissance qui en résulte est de : 1 800 litres/h x 1,163 kWh/litre.K x (45 – 10) K = 73,3 kW Sur base d’une alimentation 230 Volts, l’ampérage nécessaire serait de : Courant = Puissance / Tension = 73 300 W / 230 V = 319 Ampères !!! On n’ose imaginer le câble et le disjoncteur de protection ! |
Seul le petit débit d’un percolateur est admissible en électrique instantané. Il correspond également à la douceur avec lequel le grain de café finement moulu doit être arrosé … afin d’en capter tout l’arôme !
Aucune comparaison avec les besoins d’eau chaude d’un bâtiment tertiaire !
A la limite, on pourrait imaginer un préparateur instantané près d’un point de puisage (lavabo), mais on installe plus classiquement un ballon accumulateur « rapide » de 5 à 30 litres max, doté d’une puissance de 120 à 200 Watts/litre et dont le temps de chauffe n’excède pas 45 minutes. Ils permettent de ne pas devoir tirer un câble spécifique de raccordement depuis le coffret de distribution électrique.
Lors du chauffage de l’eau, son volume se dilate de 4 % environ. Il existe des appareils pour circuit ouvert ou fermé. Pour l’appareil à écoulement libre, on utilisera une robinetterie appropriée. L’appareil à circuit fermé sera lui résistant à la montée en pression.
Technologie du préparateur gaz
Comme tout préparateur instantané, il chauffe l’eau au fur et à mesure du soutirage, c’est à dire en continu lors de son passage dans l’appareil. Cette technique nécessite une puissance de production importante… qui n’est parfois utilisée que sur de très courtes périodes.
On distingue 3 classes d’appareils de ce type :
- les appareils non raccordés à un conduit ou à un dispositif d’évacuation de fumées,
- les appareils conçus pour être raccordés à un conduit d’évacuation des produits de combustion,
- les appareils à circuit de combustion étanche à ventouse.
![]() Accumulateur gaz à ventouse. |
|
Le préparateur instantané gaz est réservé à la desserte d’un petit nombre de points de puisage.
Fonctionnement d’un appareil mixte
Voici son fonctionnement en mode chauffage du circuit de radiateurs :
![]() Mode de fonctionnement chauffage. |
|
Et le même appareil en fonctionnement production d’eau chaude sanitaire :
![]() Mode de fonctionnement eau chaude sanitaire. |
|
Fonctionnement d’un appareil à condensation
Si la condensation de la vapeur d’eau des fumées est recherchée, un échangeur complémentaire alimenté en eau froide sera placé avant la sortie des fumées dans la cheminée.
Voici son fonctionnement en mode chauffage du circuit de radiateurs & ECS.
![]() Mode de fonctionnement chauffage. |
|
et le même appareil en fonctionnement production d’eau chaude sanitaire :
![]() Mode de fonctionnement eau chaude sanitaire. |
|
Les schémas ci-dessus sont plutôt des schémas de principe puisque, en tombant, les gouttes d’eau condensées risquent d’éteindre la flamme !
Dans la pratique, l’évacuation des condensats se fera mieux si l’échangeur de condensation est situé en dessous de l’échangeur principal. C’est ce que montre le schéma ci-dessous d’une chaudière à condensation traditionnelle, avec un conduit de fumées raccordé en partie inférieure :
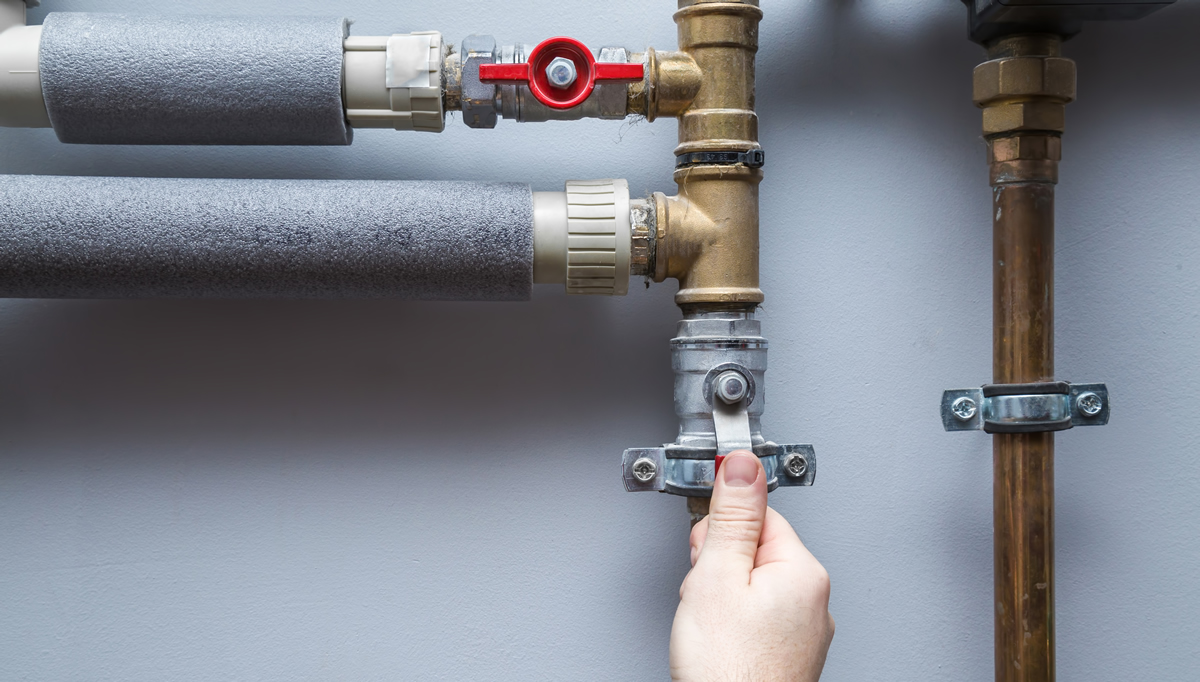
Régulation de la production d’eau chaude par « priorité sanitaire »
Le principe
Dans les installations domestiques, la régulation d’une installation de production d’eau chaude sanitaire combinée à l’installation de chauffage se base sur le principe de la « priorité sanitaire« . Lorsqu’il y a demande d’eau chaude sanitaire, la distribution de chauffage est mise en « stand by » et le ballon de stockage d’eau chaude est alimenté.
Cette technique de régulation a pour intérêt de ne pas devoir surdimensionner la chaudière pour assurer la production d’eau chaude et de ne pas maintenir en permanence (hiver comme été) la chaudière à haute température.
En pratique, cette technique de régulation ne se rencontre pas dans le secteur tertiaire. On n’imagine pas de fermer les départs différents circuits, au bénéfice des seuls besoins de l’eau chaude sanitaire.
Par contre, il est recommandé d’avoir une régulation de la température de départ de chaudière telle que la haute température ne soit appliquée que lorsqu’il y a demande de production d’eau chaude sanitaire. Imaginons un ballon réglé sur 60°C :
- En temps normal, c’est la régulation à température glissante qui est de rigueur.
- Lorsqu’il y a demande d’eau chaude sanitaire (T°ballon = 57,5°C), la température de départ chaudière augmente et les vannes mélangeuses des différents circuits de chauffage vont se fermer quelque peu.
- Dès la satisfaction du ballon (T°ballon = 62,5°C), la température de chaudière revient à la valeur calculée par le régulateur en fonction de la température extérieure.
Cette régulation sous-entend l’absence d’un préparateur instantané (échangeur à plaques) qui lui doit pouvoir réagir au quart de tour, et qui demandera une température de chaudière toujours élevée.
Elle montre aussi toute l’importance d’un surdimensionnement du serpentin installé dans le ballon :
T°chaudière = T°ballon + X°
X sera d’autant plus petit que la puissance de l’échangeur sera grande. Dimensionner le serpentin au régime 70/40 entraînera environ 10 % de coût d’investissement en plus, mais à l’exploitation, c’est la consommation de la chaudière qui baissera.
La justification
L’intérêt d’une telle régulation est d’autant plus important :
1° – Que la chaudière alimente le ballon d’eau chaude aussi en été. Dans ce cas, la régulation permettra d’arrêter totalement la chaudière (température retombant à 20°C) sauf durant les périodes de chauffage de l’eau sanitaire.
Ces périodes seront définies par une horloge qui limitera la charge du ballon de stockage à un nombre limité de périodes de la journée. Cela permet d’éviter que la chaudière ne démarre pour des faibles puisages, avec pour conséquence :
- Un maintien quasi permanent de la chaudière à une température moyenne relativement élevée,.
- Un fonctionnement du brûleur par cycles courts, synonyme de mauvaise combustion et d’émission polluantes.
Cas fréquent : le ballon présente une capacité supérieure aux besoins de la journée.
–> en été, une horloge n’autorisera le fonctionnement de la chaudière que durant 3 heures au matin, par exemple. |
2° – Que la chaudière présente des pertes à l’arrêt élevées. Ce n’est pas le cas des chaudières fuel ou gaz à brûleur pulsé modernes. C’est, par contre, le cas des chaudières gaz atmosphériques dont l’échangeur est en communication ouverte avec la cheminée (chaudières par ailleurs à proscrire dans une nouvelle installation). Il faut que ces chaudières soient toujours maintenues à la plus basse température possible (température définie par leur conception et donc par le fabricant).
Exemples.
Prenons une chaudière moderne à brûleur pulsé correctement dimensionnée de 300 kW. Son coefficient de perte à l’arrêt à température nominale (température d’eau de 70°C) est de 0,3 %. Si cette chaudière travaille en température glissante, sa température moyenne sur la saison de chauffe sera d’environ 43°C. Son coefficient de perte à l’arrêt moyen sera alors de 0,11 % : [(43 [°C] – 20 [°C]) / (70 [°C] – 20 [°C])] 1,25 x 0,3 [%] = 0,11 [%] Par rapport au fonctionnement permanent de la chaudière à température constante de 70°C, cela permet un gain sur le rendement saisonnier (et donc sur la consommation) de seulement 0,4 %. L’impact sera d’autant plus réduit qu’après une relance de la chaudière, celle-ci mettra un certain temps à se refroidir et à retrouver sa température d’origine. En moyenne, elle restera donc durant la journée à une température moyenne plus élevée que ne le justifierait le seul chauffage. Prenons l’exemple d’une chaudière gaz à brûleur atmosphérique ancienne génération de 300 kW surdimensionnée de 100 %. Son coefficient de perte à l’arrêt à température d’eau de 70°C est de 1,3 %. Si la conception de cette chaudière lui permet de travailler en température glissante (température moyenne sur la saison de chauffe d’environ 43°C) et ne remonte en température que pour produire l’eau chaude sanitaire, le gain sur le rendement saisonnier sera cette fois d’environ 4 %, par rapport au fonctionnement permanent de la chaudière à température constante de 70°C. Pour une consommation de 240 000 m³ de gaz par an, cela équivaut à une économie de : 0,04 x 240 000 [m³/an] = 9 600 [m³/an] ou environ 2 150 [€/an] |
À noter que certains constructeurs proposent une régulation tout à fait optimisée :
- Lorsque la température dans le ballon atteint 61 ou 62°C, la chaudière est déjà coupée. La circulation d’eau chaude est maintenue de telle sorte que le ballon monte à 62,5°C mais sans prolonger inutilement le maintien en température de la chaudière.
- Certains ballons sont régulés via 2 sondes plongeuses : si le puisage est faible, la première sonde est froide mais la deuxième reste chaude. L’installation ne réagit pas, elle se base sur la température moyenne entre les 2 sondes. Si le puisage est important, des remous vont déstratifier la température dans la cuve, la deuxième sonde sera rapidement touchée par le flux d’eau froide : une réaction immédiate de l’installation de chauffage est programmée. Cette astuce permet de ne pas faire réagir trop vite la chaudière et d’attendre qu’un volume d’eau important soit à réchauffer, ce qui augmente la durée de la période de condensation.
Complément : une horloge en été
Si l’on constate que la demande peut être couverte facilement par une ou deux relances de la chaudière sur la journée, il est utile, en plus de la priorité sanitaire, de greffer une horloge sur la régulation pour imposer les plages horaires durant lesquelles le réchauffage du ballon est autorisé. Par exemple : de 5 à 7 heures du matin et de 16 à 18 heures en fin de journée. Ainsi, on évitera de remettre la chaudière en route pour le puisage d’un seau d’eau ! C’est surtout avantageux en été, bien sûr, mais ce l’est également en hiver puisque la température moyenne d’une chaudière régulée en fonction de la température extérieure est de 43°C en hiver.
Cette technique a fait l’objet d’une simulation sur une installation ECS domestique (consommation de 45 m³ à 55°C). Voici les rendements obtenus (source « Chauffage et production d’ECS » – M. Rizzo – Éditions Parisiennes) :
Chauffage de l’ECS constant |
Chauffage de l’ECS programmé |
|
Eté |
44 % |
66 % |
Hiver |
69 % |
80 % |
Année |
59 % |
75 % |
Soit un gain moyen annuel de 21 % sur la consommation relative à la production d’eau chaude.
Alternative
S’il est difficile de planifier les périodes de chauffage de l’eau chaude, il est possible d’obtenir un effet similaire en régulant le ballon au moyen d’un thermostat à fort différentiel situé en partie haute (au moins au 2/3 de la hauteur). Ce thermostat arrête la pompe de circulation du réchauffeur quand on atteint la valeur désirée, généralement 60 à 65°C et remet le chauffage en service quand l’eau tombe à 40/45°C.
Précautions
Si la priorité sanitaire impose des périodes de coupure de chauffage importante (ce qui est à déconseiller pour le confort des occupants), les circuits de chauffe ont le temps de se refroidir. Au moment de la relance de ces derniers, les vannes vont s’ouvrir et/ou les circulateurs s’enclencher et l’eau froide des circuits va débouler dans la chaudière créant un choc thermique.
Il en va de même si, en mi-saison, l’installation travaille en température glissante : la chaudière sera toujours à haute température lorsque l’eau des circuits de chauffage à température mitigée revient à nouveau vers la chaudière.
Cela peut causer à terme la rupture des chaudières en fonte.
Exemple.
Durant le puisage de l’eau chaude sanitaire, les circuits de chauffage sont fermés et se refroidissent. A la relance du chauffage, l’eau froide des circuits est envoyée vers la chaudière chaude. |
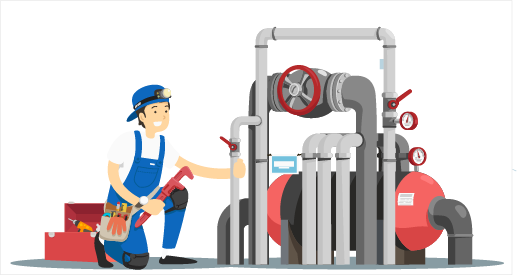
Préparateur d’eau chaude à accumulation
Éléments communs aux différentes technologies
Un préparateur d’eau chaude à accumulation est un réservoir dans lequel l’eau froide est chauffée puis accumulée. Cette fonction « accumulatrice » lui permet de répondre rapidement à une demande importante.
Les technologies se distinguent notamment en fonction du vecteur énergétique : gaz, électricité ou à eau chaude.
Cuve résistantes à la corrosion
L’eau est naturellement agressive suite à la présence de l’oxygène. Si dans un circuit de chauffage cette eau tourne sur elle-même et est considérée comme « morte », l’eau sanitaire est au contraire toujours renouvelée. Différents types de matériaux existent
- L’acier St 37 galvanisé au bain, à chaud, mais cette technique est abandonnée aujourd’hui.
- Le cuivre et les alliages de cuivre, qui semble doté d’une bonne résistance à la corrosion mais pour lequel nous manquons d’expérience. Il est couramment utilisé dans les pays scandinaves et en Angleterre.
- L’acier inoxydable (acier CrNiMo), qui doit être suffisamment allié pour la construction d’un chauffe-eau. On utilise généralement les nuances DIN 1.4435 ou 1.4571, soit des aciers à faible taux de carbone avec adjonction de molybdène. Pour les gaines de corps de chauffe, plus fortement sollicitées, on adopte des alliages plus performants à teneur élevée de nickel, tels que le IN 1.4539, l’Inconel, etc… La qualité de l’équipement est souvent liée à la réalisation des soudures et au décapage intérieur des cuves.
- L’acier St 37 avec revêtement organique ou synthétique. L’acier est soumis à différents traitements préparatoires (traitement chimique ou sablage) pour assurer l’accrochage de l’enduit. Son usage est limité puisqu’il requiert de ne pas dépasser la température prescrite par le fournisseur (généralement 60°C).
- Enfin l’acier St 37 émaillé. L’acier est du type pauvre en carbone. Différents traitements (chimiques ou mécaniques) sont nécessaires avant l’émaillage. Celui-ci est réalisé généralement par deux couches successives cuites au four à 890°C.
Protection cathodique contre la corrosion
Les revêtements émaillés comportent quelques pores après la cuisson. Pour exclure tout risque, les appareils émaillés sont munis d’une protection cathodique ou galvanique. Lors de la formation d’une pile électrique, c’est toujours l’anode qui se corrode. Le principe est donc de protéger l’acier (= la cathode) en le mettant en contact avec un métal moins noble que lui (= l’anode).
L’anode, plongée dans l’eau, est généralement en alliage de magnésium. Le fer « ennobli » reste intact et le magnésium sacrifié se dissout. L’anode devra être remplacée lorsque son usure dépasse 60 %.
Ce type d’anode est dégradable, mais il existe également des anodes électroniques (généralement en titane) fonctionnant sur le secteur, et qu’il ne faut en principe jamais remplacer. En cas de panne de courant, elles sont alimentées par une batterie rechargeable. Mais celle-ci n’a qu’une capacité de 1 à 2 jours. Cela suffit si le courant est coupé pendant la journée, parce que le boiler ne fonctionne que la nuit. Cela pourrait poser problème si le courant est coupé durant une période de vacances, par exemple. Le boiler ne serait plus protégé contre la corrosion.
Les pertes thermiques du ballon
Elles sont évaluées via sa constante de refroidissement Cr (puissance de déperditions du ballon) et sa constante d’entretien ce (pertes annuelles).
Mais les performances des ballons usuels sont généralement très proches de la valeur du ballon dit « surisolé » dans la norme française NF C 73-221.
Voici les critères proposés par l‘Ordonnance sur la procédure d’expertise énergétique des réservoirs d’eau chaude en Suisse (22/01/92) :
Capacité | Pertes maximum admissibles [kWh/24h] |
Capacité | Pertes maximum admissibles [kWh/24h] |
30 | 0,75 | 1 000 | 4,70 |
50 | 0,90 | 1 100 | 4,80 |
100 | 1,30 | 1 200 | 4,90 |
200 | 2,10 | 1 300 | 5,00 |
300 | 2,60 | 1 400 | 5,05 |
400 | 3,10 | 1 500 | 5,10 |
500 | 3,50 | 1 600 | 5,12 |
600 | 3,80 | 1 700 | 5,14 |
700 | 4,10 | 1 800 | 5,16 |
800 | 4,30 | 1 900 | 5,18 |
900 | 4,50 | 2 000 | 5,20 |
Le préparateur à accumulation gaz
Le préparateur à accumulation gaz est conçu pour chauffer et maintenir en température un certain volume d’eau variant de 75 à 200 litres.
Ce système permet de distribuer de grandes quantités d’eau chaude à plusieurs postes de puisage. L’eau est chauffée avant et durant les puisages. La reconstitution de la réserve d’eau chaude est rapide (entre 20 et 90 minutes, suivant les modèles).
Le réservoir est calorifugé et l’eau est ainsi maintenue à une consigne de 45 à 60°C.
Il existe des préparateurs « haut rendement » et des préparateurs à condensation.
L’accumulateur électrique
Le petit accumulateur décentralisé (contenance de 5 à 30 litres)
Prévu pour la fourniture d’un ou deux postes, il répond à des besoins ponctuels et supprime la nécessité de raccordement à une installation centralisée.
Certains appareils résistent à la pression (circuit fermé), d’autres sont à écoulement libre mais doivent être suivi d’une robinetterie permettant la dilatation de l’eau chauffée.
Il existe également des chauffe-eaux rapides, dotés d’une puissance de 120 à 200 Watts/litre et dont le temps de chauffe n’excède pas 45 minutes.
Il est possible de les encastrer (comme un réfrigérateur ou un lave-vaisselle).
L’accumulateur électrique prévu pour une préparation centralisée
La capacité d’accumulation est de plusieurs centaines de litres. Il est possible de le faire fonctionner en continu (alimentation électrique permanente) ou en accumulation en période tarifaire creuse (heures de nuit). Dans ce cas, le dimensionnement est basé sur la couverture des besoins quotidiens.
La puissance installée est de l’ordre de 10 à 12 Watts/litres (exemple : un ballon de 200 litres sera équipé d’une résistance de 2 ou 2,5 kW).
Il existe également des accumulateurs à double résistance électrique, un dans la partie inférieure assurant la charge nocturne à bas tarif, alors que l’élément chauffant supérieur couvre les demandes de pointe en eau chaude pendant la journée. L’enclenchement simultané des deux résistances n’est pas réalisé pour limiter la puissance cumulée.
Les thermostats installés sur les chauffe-eau sont préréglés (60 à 65°C) et le point de consigne ne peut pas toujours être modifié.
Pour permettre la dilatation de l’eau lors du chauffage, on trouve en amont du chauffe-eau un groupe de sécurité (un par appareil). Il comporte :
- un robinet d’arrêt, pour couper l’arrivée d’eau froide dans le chauffe-eau (démontage),
- un clapet de retenue, pour éviter le retour d’eau chaude dans la canalisation d’eau froide,
- une soupape de sûreté, pour limiter la pression dans le chauffe-eau,
- un dispositif de vidange, pour vidanger le réservoir.
- Carrosserie.
- Calorifuge (laine minérale, polyuréthane sans CFC).
- Cuve (acier galvanisé, cuivre ou acier).
- Thermovitrification / émail / plastique.
- Prise d’eau froide.
- Brise-jet.
- Fond.
- Tube plongeur pour sonde de thermostat.
- Corps de chauffe.
- Pieds réglables.
- Capot de recouvrement.
- Raccordement électrique.
- Thermostat de réglage et de sécurité.
- Flasque.
- Anode en magnésium.
- Thermomètre.
- Prise d’eau chaude.
- Groupe de sécurité (là, il faut le deviner !).
- Vidange à l’égout.
En voici le fonctionnement. Au fur et à mesure que l’eau monte dans la cuve, la pression augmente. Un clapet de sécurité évacue l’excès de pression. Le trop-plein d’eau s’écoule par le tuyau de décharge. Un bouton ou une manette fixée sur le groupe de sécurité permet d’actionner manuellement le clapet.
En l’actionnant régulièrement (tous les mois, par exemple), on évite qu’il ne s’encrasse ou ne s’entartre.
Les corps de chauffe électriques
On rencontre essentiellement deux systèmes :
> Les résistances blindées (ou thermoplongeurs), barres chauffantes de 6 à 9 mm environ. Le fil électrique chauffant est noyé dans de l’oxyde de magnésium (MgO) très pur à haute densité, matériau qui est à la fois un très bon conducteur de la chaleur et un protecteur de l’oxydation du conducteur chauffant.
Avantages.
- Moins de dépôt de calcaire suite aux dilatations et retraits successifs de la barre blindée.
- Une faible masse et donc une transmission très rapide de la chaleur vers l’eau.
- Un flasque de plus petite surface que celle d’une résistance céramique et donc une limitation des pertes énergétiques.
- Une possibilité, lors de sa construction à froid, de préformer la barre en fonction de la forme du chauffe-eau et donc de réduire la zone froide du fond (mesure anti-légionelle).
Inconvénients.
- La puissance élevée peut provoquer du bruit pendant la phase de réchauffage de l’eau.
- Il est nécessaire de vider le réservoir pour remplacer le corps de chauffe.
> Les corps de chauffe en céramique, où les résistances spiralées sont tirées dans les gorges des éléments en céramique, le tout étant introduit dans un tube de protection plongeur.
Avantages.
- Une inertie relativement importante et donc une charge plus lente qui limite la production de bruit.
- Un remplacement aisé de la garniture céramique contenue dans un tube plongeur sans devoir vidanger le ballon.
- Un flasque plus grand, facilitant les travaux d’entretien.
Inconvénients.
- La formation d’une couche calcaire sur le tube plongeur et donc une moins bonne transmission de chaleur.
- Des pertes thermiques plus élevées par les flasques, et cela malgré l’isolation thermique en céramique à l’extrémité du flasque.
- Zone morte plus importante au bas de la cuve, favorisant la stagnation d’eau à température faible et donc le développement de la légionelle.
Appareil à double corps de chauffe
Il existe des appareils équipés de 2 résistances : l’élément chauffant inférieur assure la charge nocturne à bas tarif, alors que l’élément chauffant supérieur couvre les demandes de pointe en eau chaude durant la journée. L’enclenchement simultané des deux résistances n’est généralement pas autorisé en raison de la puissance cumulée.
L’accumulateur à échangeur intégré
Un serpentin de chauffage ou un faisceau tubulaire est intégré. C’est un échangeur de chaleur parcouru par un fluide caloporteur, généralement de l’eau chaude, parfois de la vapeur. Il offre la possibilité de préparer l’eau chaude via une chaudière (gaz, fuel, …), via un capteur solaire ou via une pompe à chaleur.
L’échangeur est généralement en acier inoxydable ou en tube d’acier émaillé.
L’échangeur peut également consister en un faisceau de tubes lisses ou à ailettes, fixé sur un flasque lui-même intégré au chauffe-eau ou monté sur celui-ci.
L’accumulateur mixte
L’accumulateur mixte dispose d’un double raccordement : un serpentin d’eau chaude et une résistance électrique.
Deux types d’alternance sont possibles :
- Soit suivant la saison : chauffer par la chaudière en hiver et électriquement en été.
- Soit suivant la complémentarité des sources : chauffage de base par capteur solaires/pompe à chaleur/récupérateur de chaleur et chauffage d’appoint électrique lorsque le niveau de température de consigne n’est pas atteint.
- Thermomètre.
- Tube plongeur pour sonde de thermostat.
- Anode en magnésium.
- Tube de retour de circulation.
- Cuve (acier galvanisé, cuivre ou acier).
- Thermovitrification / émail / plastique.
- Capot de recouvrement.
- Thermostat de réglage et de sécurité.
- Corps de chauffe.
- Prise d’eau froide.
- Brise-jet.
- Tube plongeur pour sonde de thermostat.
- Pieds réglables.
- Calorifuge (laine minérale, polyuréthane sans CFC).
- Retour chauffage.
- Serpentin.
- Aller chauffage.
- Prise d’eau chaude.
S’il s’agit d’un chauffage par pompe à chaleur ou par énergie solaire, la position de l’échangeur électrique doit ors se placer en position médiane, créant 2 ballons : un demi-ballon inférieur pour le préchauffage solaire et un demi-ballon supérieur pour l’appoint électrique…
Une séparation totale en 2 ballons en série restera toujours préférable.
La stratification des températures
Lors de la charge, l’eau est chauffée, elle se dilate, sa densité diminue et elle se déplace vers le haut. Au-dessus de l’échangeur, l’eau chaude s’élève comme de la fumée au-dessus d’un feu.
Par contre, l’eau située au-dessous du corps de chauffe n’est pour ainsi dire pas chauffée et reste pratiquement froide.
Lors de la décharge du réservoir, l’eau chaude est progressivement remplacée par l’eau froide. Des perturbations peuvent se produire dans la stratification des températures. Or un « mélange » des températures intérieures est préjudiciable à la bonne utilisation du ballon.
Exemple.
Un ballon contient 200 litres à 60°C. Un puisage de 100 litres est réalisé. Il contient donc encore 100 litres à 60°C et 100 litres à 10°. Il peut être utilisé valablement. Si des tourbillons ont entraînés le mélange de l’eau, c’est 200 litres à 35°C qui seront présents… Aucune énergie n’est perdue, mais l’eau est « inutilisable ». Un réchauffement sera nécessaire pour ramener l’eau à 60°C. Cette situation (caricaturale) est surtout à éviter pour l’accumulateur électrique, car il appellera un appoint de jour, mais aussi pour un système traditionnel à eau chaude car il risque de relancer la chaudière suite au moindre soutirage. |
Des perturbations de la stratification peuvent avoir lieu suite à :
- une vitesse d’arrivée d’eau trop élevée,
- une circulation interne quand l’isolation est insuffisante (refroidissement de l’eau le long des parois),
- un retour de boucle de circulation trop froid,
- une disposition horizontale du ballon.