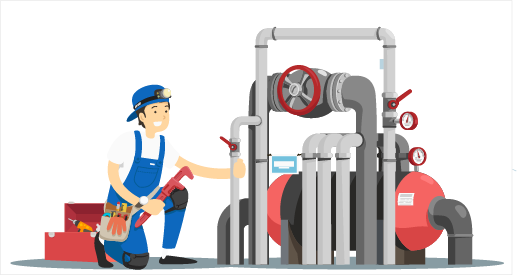
Refroidissement adiabatique
Principe de base
Le principe est le suivant : si de l’air chaud et sec traverse un filet d’eau, il en provoque l’évaporation. La chaleur nécessaire à la vaporisation d’eau étant extraite de l’air. Celui-ci se refroidit.
Par exemple, de l’air à 20°C, 30 % HR traversant un nuage d’eau voit sa température atteindre 12°C en se chargeant d’humidité.
Le refroidissement adiabatique peut-être
- direct : si l’air humidifié soit directement pulsé dans l’ambiance;
- indirect : si de l’air pulsé ou un réseau d’eau est refroidi par échange avec l’air qui aura été humidifié.
Refroidissement indirect de l’air pulsé
Il existe des échangeurs à plaques dans lequel l’air vicié est refroidi par humidification. Un tel système permet d’exploiter le « pouvoir refroidissant » de l’humidification adiabatique, tout en évitant le problème de l’humidification de l’air neuf.
Photo d’une centrale de refroidissement adiabatique.
L’air vicié et l’air neuf passent dans un double échangeur à plaques. Dans l’échangeur, l’air vicié est humidifié. On combine donc deux phénomènes dans l’échangeur : le refroidissement adiabatique de l’air vicié et le refroidissement au contact avec l’air neuf. Remarquons les volets de by-pass (sur l’air neuf et l’air vicié) permettant une régulation de la puissance échangée.
Actuellement, nous manquons de données neutres pour juger des performances et de l’intérêt énergétique d’un tel équipement. Il semblerait que si l’humidification de l’air vicié est effectuée avant l’échangeur, le refroidissement complémentaire qui en résulte ne soit pas suffisant pour augmenter significativement l’énergie récupérée en période de climatisation. C’est apparemment l’intégration de l’humidificateur dans l’échangeur, qui augmenterait les performances du système. En effet, dans ce cas, l’eau s’évapore dans l’échangeur et refroidit aussi bien celui-ci que l’air vicié. Le fabricant de ce matériel annonce, dans les meilleures conditions, un refroidissement de l’air neuf de 10 °C.
En hiver, avec l’arrêt de l’humidification, on retrouve le fonctionnement d’un groupe « traditionnel » avec échangeur à plaques.
Refroidissement indirect d’un réseau d’eau
Il existe d’autres modes de refroidissement exploitant le principe de l’évaporation de l’eau, notamment associés à des machines frigorifiques avec possibilité de free chilling via aérorefroidisseur ou tour de refroidissement.
Photo d’un refroidisseur adiabatique.
Dans ce processus, quel que soit le mode d’humidification, le principe est toujours le même : les molécules d’eau passent progressivement à l’état de vapeur, provoquant ainsi par évaporation une diminution de la température d’air.
Son efficacité sera accrue si la surface de l’eau est grande, si le débit d’air à la surface de l’eau est important et si la température de l’air est élevée.
Enfin, il est indispensable d’assurer un contrôle et une maintenance très rigoureux des équipements, car :
- les surfaces humides présentent un terrain favorable au développement des micro-organismes;
- l’évaporation provoque des dépôts consécutifs à la cristallisation (sels minéraux, carbonates);
- la ventilation de l’air favorise les dépôts de poussière.
Avantages et inconvénients
- La solution simple permettant un refroidissement naturel en exploitant des équipements existants : groupe de ventilation, tour de refroidissement, …
- Mais le pouvoir rafraîchissant est limité.
- Le refroidissement de l’air est d’autant plus grand que le climat est chaud et sec (un tel système est donc inutile dans les régions où le climat est tropical, c’est-à-dire que l’air chaud est déjà chargé en humidité excessive. Chez nous, on se retrouve entre les deux …
- Le refroidissement de l’eau ne sera lui possible que pour des températures extérieures typiques de la mi-saison, voire de nuit.
- On parle donc bien de rafraîchissement et non de climatisation au sens de la fourniture d’une puissance de froid suffisante quels que soient les besoins.
- Le dispositif ne peut être régulé avec précision, car il dépend de l’hygrométrie extérieure. Il est d’autant plus efficace que le climat est chaud et sec.
- La consommation en eau non négligeable, nécessite qu’elle soit de bonne qualité pour éviter l’entartrage des tuyauteries, ainsi que les problèmes de légionelles. Pour éviter ce désagrément, un traitement d‘eau est nécessaire. Évidemment, l’utilisation de l’eau de pluie réduit l’impact sur la consommation en eau potable, mais nécessite la garantie du fabricant quant à la résistance de ses équipements.
Régulation
Les éléments qui constituent l’installation : filtres, surpresseur, pressostats de sécurité, pompe, électrovanne, rampes avec buses, échangeur, vannes de purge.
La régulation du refroidissement adiabatique repose principalement sur le contrôle des débits d’air et d’eau.
La régulation pour la ventilation d’air peut être de deux types :
Régulation par étage
Des étages de ventilation s’enclenchent les uns après les autres. Lorsque 100 % de la ventilation est en fonctionnement et que la température extérieure est supérieure à la valeur de consigne d’enclenchement de la brumisation haute pression, une électrovanne s’ouvre et un surpresseur se met en route.
Régulation par variations de fréquence
La variation de vitesse régulera jusqu’à ce que 100 % du débit de ventilation soit en fonctionnement (à 50 Hz l’électrovanne de la rampe s’ouvre et le système adiabatique fonctionne).
La régulation pour le débit d’eau projeté
Un brouillard d’eau efficace offre la plus grande surface d’échange possible avec l’air.
Cette surface d’échange est d’autant plus grande que le nombre de microgouttelettes pulvérisées est important. Pour obtenir un brouillard de qualité, l’eau est donc mise sous forte pression (100 bar) et accumule ainsi, une énergie importante. Le débit d’eau de brumisation est calculé précisément afin d’apporter à l’air la juste quantité d’eau.