Régulation de plusieurs chaudières ou de brûleurs à plusieurs allures en cascade
La régulation en cascade s’applique à des installations équipées de plusieurs chaudières ou de brûleurs à deux allures (fuel ou gaz), c’est-à-dire à des installations dont la puissance totale est fractionnée en plusieurs unités.
Elle consiste à n’enclencher un étage de puissance que lorsque celui-ci est nécessaire.
Principe de fonctionnement
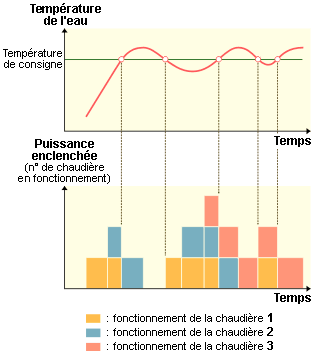
Régulation en cascade de 3 chaudières. Ici la cascade se fait suivant le principe « première allumée – première arrêtée » qui permet d’équilibrer naturellement les temps de fonctionnement de chaque chaudière.
Un régulateur climatique ou un aquastat à température constante fixe une température d’eau à fournir.
Au démarrage, le premier étage de puissance s’enclenche (première allure du brûleur ou première chaudière). Si après un certain temps programmable, la consigne de température n’est pas atteinte, un deuxième étage de puissance vient en complément (deuxième allure du brûleur ou deuxième chaudière), puis un troisième si nécessaire.
Lorsque la température de consigne est dépassée, un premier étage de puissance s’arrête (par exemple, le premier allumé). Si après un certain temps, la consigne est toujours dépassée, un deuxième étage s’arrête également. Si la température descend en dessous de la consigne, un étage complémentaire est réenclenché.
La puissance mise en œuvre suit ainsi les besoins. En effet, si la petite puissance est suffisante pour maintenir la consigne (en mi-saison), les autres étages ne seront pas enclenchés.
Exemple.
Dans le cas de deux chaudières équipées chacune d’un brûleur 2 allures, on dispose de 4 étages de puissance qui peuvent s’enclencher suivant la séquence :
- chaudière 1, allure 1
- puis chaudière 1, allure 2
- puis chaudière 2, allure 1
- puis chaudière 2, allure 2
ou la séquence :
- chaudière 1, allure 1
- puis chaudière 2, allure 1
- puis chaudière 1, allure 2
- puis chaudière 2, allure 2
La première solution a l’avantage de limiter la nombre de démarrages de brûleur à « froid », synonymes de mauvaises combustions transitoires. Par contre, elle ne favorise pas le fonctionnement des brûleurs en première allure, c’est-à-dire avec le meilleur rendement de combustion.
Le compromis peut donc être trouvé dans la description faite par le cahier des charges type 105 de la Régie des bâtiments (1990) où on recommande que l’enclenchement se fasse suivant la séquence :
- chaudière 1, allure 1
- puis chaudière 1, allure 2
- puis chaudière 2, allure 1
- puis chaudière 2, allure 2
et le déclenchement suivant la séquence :
- chaudière 2, allure 2
- puis chaudière 1, allure 2
- puis chaudière 2, allure 1
- puis chaudière 1, allure 1
|
Intérêt
L’intérêt de la régulation en cascade se situe au niveau de :
- L’adaptation au plus juste la puissance mise en œuvre aux besoins thermiques du bâtiment, de manière à obtenir un temps de fonctionnement des brûleurs le plus long possible. En effet, plus le temps de fonctionnement d’un brûleur est long par rapport au temps d’utilisation d’une chaudière meilleur sera son rendement (diminution du temps d’attente de la chaudière et donc de ses pertes à l’arrêt (augmentation du facteur de charge) et diminution des émissions polluantes associées au démarrage des brûleurs).
- Dans le cas de plusieurs chaudières régulées en cascade : l’élimination des pertes à l’arrêt des chaudières non nécessaires en arrêtant leur irrigation à l’arrêt du brûleur par fermeture automatique d’une électrovanne et l’arrêt du circulateur de la chaudière si elle en possède un.
- Dans le cas de brûleurs 2 allures : l’augmentation du rendement de combustion. En effet, en petite allure, la puissance du brûleur diminuant par rapport à la surface d’échange, les fumées sont évacuées plus froides vers la cheminée et donc les pertes par les fumées diminuent. Un gain de 2 .. 2,5 % sur le rendement de combustion peut être obtenu lorsque la puissance du brûleur est de l’ordre de 60 .. 70 % de la puissance de la chaudière.
On l’aura compris, la régulation en cascade des chaudières peut améliorer le rendement saisonnier de l’installation de production de chaleur.
Exemple.
Un bâtiment nécessite une puissance de chauffage de 800 kW.
Voici le temps de fonctionnement simulé du(des) brûleur(s) en fonction du découpage de la puissance choisi, pour une durée de la saison de chauffe de 5 800 heures/an :
Nombre de chaudières |
Type de brûleur |
Temps de fonctionnement du (des) brûleur(s) à chaque allure [h/an] |
1 de 800 [kW] |
1 allure |
2 009
(all 1 : 800 [kW]) |
1 de 800 [kW] |
2 allures (60 % / 100 %) |
2 754
(all 1 : 480 [kW]) |
374
(all 2 : 800 [kW]) |
2 de 400 [kW] |
2 allures (60 % / 100 %) |
4 210
(ch 1 – all1 : 240 [kW]) |
417
(ch 1 – all2 : 400 [kW]) |
1 725
(ch 2 – all1 : 240 [kW]) |
40
(ch 2 – all2 : 400 [kW]) |
Voici le rendement saisonnier de l’installation obtenu avec différentes combinaisons de chaudières, en fonction des pertes à l’arrêt de celles-ci. Les hypothèses prises pour la simulation sont :
- une puissance de chauffe non surdimensionnée,
- un rendement de combustion de 92% en grande allure de brûleur et de 94% en petite allure,
- une séquence de régulation de la cascade suivant l’ordre : « chaudière 1, petite allure, puis chaudière 2, petite allure, puis chaudière 1, grande allure, puis chaudière 2, grande allure ».
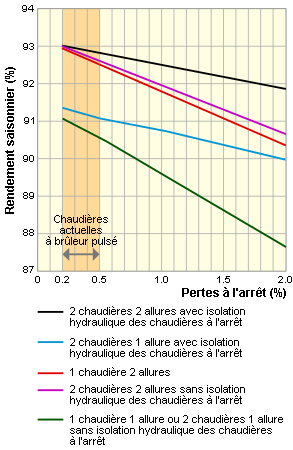
Calcul du rendement saisonnier de la production de chaleur en fonction du choix de la combinaison de chaudières.
L’écart affiché entre les différentes solutions s’accentue lorsque l’installation est surdimensionnée (ici on a dimensionné la ou les chaudières au plus juste) et que les chaudières présentent des pertes à l’arrêt importantes (par exemple, pour les chaudières gaz atmosphériques).
|
On constate que, théoriquement, posséder plusieurs chaudières régulées en cascade mais qui restent irriguées en permanence ne sert quasi à rien d’un point de vue énergétique (si on ne tient pas compte de la production d’imbrûlés et autres émissions polluantes).
L’écart de rendement saisonnier entre les différentes solutions s’amenuise lorsque les pertes à l’arrêt des chaudières diminuent (arrêt de la circulation d’air dans la chaudière à l’arrêt et isolation performante). Il peut même devenir nul ou négatif en fonction des conditions de fonctionnement. La différence est de moins de 0,5 % sur la consommation annuelle pour des chaudières modernes à faibles pertes à l’arrêt, équipées d’un brûleur 2 allures.
En pratique
Voici différents modes de régulation possibles :
Décalage des aquastats de chaudière
Ce mode de régulation est souvent appliqué sur d’anciennes installations et n’apporte quasi pas d’économie.
Il s’agit de décaler la consigne de l’aquastat de chaque chaudière, de quelques degrés (par exemple 80°C pour une chaudière et 70°C pour l’autre).
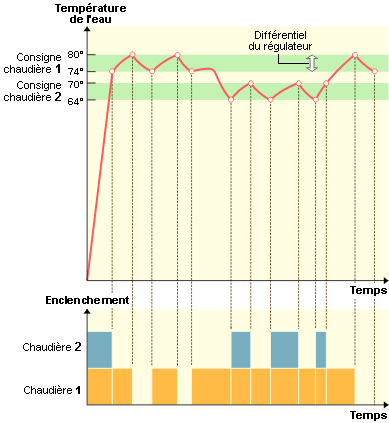
Ordre d’enclenchement des chaudières avec une régulation de cascade basée sur des aquastats de départ.
Lorsque les besoins thermiques deviennent importants (par exemple à la relance matinale), la température dans les chaudières va chuter en dessous de 70°C. Le brûleur des deux chaudières va donc s’enclencher.
Lorsque les besoins vont diminuer, la température dans les chaudières va augmenter. Lorsqu’elle dépasse 70°C, une première chaudière s’arrête. Si elle dépasse 80°C, la deuxième chaudière s’arrête. Si la température retombe en dessous de 80°C, seule cette dernière chaudière va démarrer. Si malgré le fonctionnement de celle-ci, la température d’eau continue à chuter en dessous de 70°C, la deuxième chaudière va venir au secours de la première.
Ce système présente un avantage : il ne demande pas l’adjonction d’un régulateur particulier puisque l’on travaille avec les aquastats des chaudières.
Par contre il présente trois inconvénients majeurs, qui le rendent quasi inintéressant d’un point de vue énergétique :
- Il impose l’irrigation permanente de toutes les chaudières. On perd donc un des intérêts de la régulation en cascade : la suppression des pertes à l’arrêt des chaudières non nécessaires.
- La température de départ est faible si la puissance demandée est élevée et élevée si la puissance demandée en faible. Même si les vannes mélangeuses corrigent le tir par après, c’est une situation énergétiquement défavorable.
- Les aquastats doivent avoir des consignes suffisamment décalées sous peine de voir les chaudières fonctionner en parallèle et non en cascade. En effet, si la température de retour des circuits descend en dessous de la température de consigne de la chaudière à l’arrêt, le brûleur de cette dernière s’enclenchera d’office puisqu’il mesurera une température de chaudière trop basse.
Régulation en fonction de la température de départ du collecteur
Ce mode de régulation est le plus courant.
Ici, on mesure la température commune à toutes les chaudières, sur le départ du collecteur (ne pas placer la sonde entre les chaudières). Ceci a comme avantage de permettre l’arrêt de l’irrigation des chaudières à l’arrêt et donc de diminuer les pertes.
Le fonctionnement de la cascade peut être géré par des relais temporisés ou un programmateur électronique qui enclenchent et déclenchent les différentes chaudières.
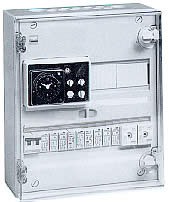
Coffret de gestion de cascade analogique.
Les nouveaux régulateurs gèrent de façon « intelligente » l’enclenchement des chaudières. Par exemple, en fonction de la courbe d’évolution de la température de l’eau par rapport à la consigne, le régulateur prendra ou non la décision d’enclencher une nouvelle chaudière, évitant ainsi tout enclenchement de courte durée.
Régulation en fonction de la température de retour du collecteur
Lorsque les besoins en chauffage augmentent, la température de retour diminue, à débit d’eau constant.
Lorsque la température de retour chute, la chaudière suivante de la séquence est enclenchée.
Exemple.
Prenons une chaufferie composée de 3 chaudières dimensionnées pour un régime de température 90°/70°. La différence entre le départ et le retour est de 20°C lorsque les besoins sont maximaux.
Si la température de départ est maintenue en permanence à 90°C, on peut déterminer la température de retour qui correspond à la puissance de chaque étage de la cascade :
20 [°C] / 3 [chaudières] = 7 [°C]
Une chaudière est nécessaire lorsque la température de retour est supérieure à :
90 [°C] – 7 [°C] = 83 [°C]
Deux chaudières sont nécessaires lorsque la température de retour est comprise en 83 [°C] et :
90 [°C] – 7 [°C] – 7 [°C] = 76 [°C]
En dessous de 76 [°C], la troisième chaudière s’enclenche.
|
Si la température de départ du collecteur est régulée en fonction de la température extérieure, la consigne de retour à maintenir, varie également.
Notons qu’avec une régulation en cascade en fonction de la température de retour, en absence de besoin, la température circulant dans la boucle primaire sera égale à la température de retour (70°C). Par contre cette température sera égale à la température de départ (90°C) dans le cas d’une régulation en fonction de la température de départ, ce qui est plus défavorable d’un point de vue énergétique.
Régulation en fonction de la chaleur fournie
Il existe également des régulateurs de mise en cascade qui se basent sur la quantité de chaleur fournie aux utilisateurs, par exemple, en mesurant les temps de fonctionnement des brûleurs.
Les chaudières modulaires
Les chaudières sont quasiment raccordées en série : si la température demandée au départ du collecteur n’est pas atteinte, la deuxième chaudière est enclenchée (ouverture de la vanne d’isolement et mise en route du circulateur). L’eau préchauffée dans la première chaudière transite alors dans la deuxième chaudière.
On peut ainsi associer une série de chaudières sur un même collecteur.
Une des caractéristiques de ce système est que la température demandée au départ du collecteur est toujours inférieure à la température maximale des chaudières puisque l’eau chaude issue de (des) la chaudière(s) est en permanence mélangée avec une partie de l’eau froide issue des retours vers le collecteur.
Un fonctionnement correct de ce type d’installation est assez aléatoire. Il demande donc un dimensionnement minutieux des différentes parties.
Précautions
Idéalement, pour fonctionner correctement, une régulation en cascade des chaudières doit comprendre :
Isolation hydraulique des chaudières à l’arrêt
Le principal intérêt de la cascade repose sur l’élimination des pertes à l’arrêt des chaudières non nécessaires. Pour cela, l’irrigation de ces chaudières doit être stoppée au moyen d’une vanne d’isolement motorisée (2 ou 3 voies). Si chaque chaudière possède son propre circulateur de charge, l’arrêt de celui-ci n’est pas suffisant. En effet, il ne faut pas négliger le débit qui peut circuler au travers d’un circulateur à l’arrêt, du fait de la pression différentielle présente dans l’installation. Une vanne d’isolement motorisée ou un clapet anti-retour complémentaire est donc nécessaire.
L’arrêt de la circulation dans les chaudières à l’arrêt a également un intérêt au niveau du bon fonctionnement de l’installation. En effet, si on maintient « ouvertes » les chaudières à l’arrêt, de l’eau de retour transitent par celles-ci et puis se mélange à l’eau chaude de départ, ce qui perturbe la régulation puisque l’on n’atteint plus la température désirée.
Vannes d’isolement à ouverture lente
L’isolation hydraulique d’une chaudière à l’arrêt est la plupart du temps réalisée par une vanne motorisée d’isolement à 2 voies. Cette vanne est généralement à vitesse lente. A la mise en route, on évite ainsi un choc thermique dans une chaudière froide subitement alimentée par des retours chauds. De plus, quand la chaudière est froide, on évite d’injecter brutalement de l’eau froide dans l’installation.
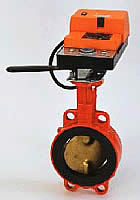
Vanne d’isolement motorisée.
C’est la fin de course de la vanne d’isolement donne l’autorisation de mise en route du brûleur, ce qui permet :
- à la chaudière de se réchauffer progressivement au contact de l’eau chaude de l’installation,
- à une chaudière ne pouvant pas travailler en très basse température de démarrer sans condenser, puisque la température de l’eau au démarrage du brûleur sera déjà supérieure à 60°C.
Cette précaution n’est pas nécessaire pour certaines chaudières à forte capacité en eau (qui peuvent fonctionner à débit nul) avec lesquelles, il est possible de mettre la chaudière en température avant l’ouverture de la vanne.
Lorsque chaque chaudière possède sa pompe de charge, il est conseillé d’enclencher la pompe avant l’ouverture de la vanne d’isolement pour éviter une perturbation dans le réseau, consécutive à l’injection brutale du débit total de la chaudière.
Temporisation à l’enclenchement
Lors de la mise en service d’une chaudière, on ne peut quasiment pas éviter une baisse de température de l’eau d’alimentation des circuits, ce qui pose des problèmes pour le régulateur de la cascade. Celui-ci à tendance à compenser cette baisse de température par la mise en route d’une chaudière supplémentaire (qui aggravera encore plus la situation). Une temporisation adéquate doit être prévue, sinon on risque de voir s’enclencher inutilement plus de chaudières que nécessaire et faire ainsi chuter le rendement saisonnier de l’installation.
La temporisation de mise en marche des chaudières dépend de leur inertie thermique. Elle peut être réglée à :
- 3 .. 10 minutes pour les chaudières peu inertes,
- 10 .. 30 minutes pour une chaudière à forte capacité en eau.
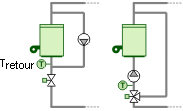
Chaudière équipée d’un by-pass de recyclage maintenant une température de retour minimale vers la chaudière.
Dans le cas de chaudières équipées d’un by-pass de recyclage avec circulateur, on peut éviter ce problème en mettant en marche le brûleur de la chaudière et le circulateur avant l’ouverture de la vanne d’isolement. Lorsque la température de retour minimale pour la chaudière est atteinte, la vanne d’isolement commence à s’ouvrir. Ce fonctionnement évite un refroidissement brutal de la température d’alimentation des circuits et facilite le contrôle de la cascade en évitant les enclenchements intempestifs de chaudières. L’inconvénient est que, durant sa remontée en température, la chaudière passe par une courte période pendant laquelle elle condense, ce qui peut être préjudiciable à certaines chaudières fonctionnant au fuel.
Evacuation de la chaleur résiduelle de la chaudière
Lorsqu’une chaudière est mise hors circuit, la circulation d’eau est maintenue pendant le temps nécessaire au dégagement de la chaleur accumulée dans la chaudière. Ce temps de circulation varie entre 2 et 15 minutes selon l’inertie thermique de la chaudière. Généralement cette temporisation est assurée par la vanne motorisée d’isolement dont le temps de fermeture est d’environ 5 minutes, ce qui est parfois insuffisant, notamment pour les chaudières à forte inertie.
On peut aussi imaginer que la vanne ne se referme que lorsque la température mesurée à la sortie de la chaudière est égale à la température de retour commune. Attention, dans ce cas, il y aura, au départ du collecteur une chute progressive de la température de départ puisque celle-ci sera le résultat d’un mélange entre de l’eau en provenance de la chaudière en fonctionnement et de l’eau de retour transitant par la chaudière à l’arrêt. La temporisation à l’enclenchement des chaudières doit permettre tout redémarrage intempestif de la chaudière mise à l’arrêt.
Pour les chaudières de forte puissance, la vanne motorisée d’isolement peut être modulante et se fermer progressivement pour maintenir la température de sortie à une valeur choisie. Cela permet d’évacuer la chaleur accumulée dans la chaudière sans perturber la température d’alimentation du réseau.
Inversion de l’ordre de cascade
L’ordre d’enclenchement des chaudières dans la cascade peut être modifié pour assurer un nombre équivalent d’heures de fonctionnement de chaque chaudière (rem : la circulation est généralement maintenue permanente dans la première chaudière de la cascade).
L’inversion de l’ordre de cascade peut être modifié manuellement, à l’aide d’une horloge ou de façon cyclique par un module d’inversion automatique inclus dans le régulateur.
Les avantages de l’inversion sont :
- la réduction de l’encrassement de la chaudière qui serait sollicitée en permanence,
- la non-déterioration de la chaudière qui serait maintenue à l’arrêt durant une longue période.
Ce principe d’inversion ne prévaut cependant pas :
- pour les chaufferies composées comprenant une chaudière traditionnelle et une chaudière à condensation. Cette dernière doit en permanence être prioritaire car elle présente toujours un meilleur rendement utile..
- pour les chaufferies composées de chaudières de puissance différentes. Dans ce cas l’enclenchement des chaudières dépendra de l’ampleur des besoins à satisfaire.
Fonctionnement prioritaire en première allure
Lorsque l’on dispose de plusieurs chaudières équipées de brûleurs 2 allures, on a tout intérêt à favoriser l’ordre d’enclenchement suivant (par exemple, pour 2 chaudières) :
- chaudière 1, allure 1
- puis chaudière 2, allure 1
- puis chaudière 1, allure 2
- puis chaudière 2, allure 2
plutôt que :
- chaudière 1, allure 1
- puis chaudière 1, allure 2
- puis chaudière 2, allure 1
- puis chaudière 2, allure 2
En effet, la première solution augmente le temps de fonctionnement des brûleurs en première allure, allure qui présente un meilleur rendement de combustion (2 à 2,5 % de gain entre la première et la deuxième allure).
Commutation automatique en cas de défaut
Si une chaudière ne peut démarrer pour un défaut de son brûleur ou de sa pompe, l’appel automatique à une autre chaudière permet de ne pas interrompre le service.
Interdiction de fonctionnement d’une chaudière en fonction de la température extérieure
Cette fonction permet de ne pas appeler systématiquement toutes les chaudières au moment des remontées en température et d’éviter des démarrages de trop courte durée en mi-saison.
Par exemple, si à chaque relance, toutes les chaudières sont mises en route, les chaudières devenues inutiles en journée mettront un temps certain à se refroidir. Elles présenteront ainsi des pertes à l’arrêt qui se rapprocheront d’une installation dont toutes les chaudières sont en permanence irriguées.
Attention cependant quand l’installation comprend un optimiseur pour gérer le ralenti nocturne. En effet, celui-ci sera perturbé s’il compte sur une puissance constante à la relance.
Limitation basse de la puissance des brûleurs en première allure
Les fabricants de chaudières définissent, par rapport à chaque chaudière, une puissance minimale en dessous de laquelle un brûleur ne peut pas descendre. Cette puissance est généralement de 60% de la puissance nominale de la chaudière. La raison de cette exigence est d’éviter les risques de condensation des fumées. En effet plus la puissance de la flamme est petite par rapport à la surface d’échangeur, plus les fumées pourront se refroidir jusqu’à ce qu’elles atteignent leur température de condensation.