
Le moins qu’on puisse dire, c’est que les idées ne manquent pas quant à la récupération de la chaleur des condenseurs afin de chauffer l’ambiance des magasins directement ou des annexes indirectement.
La question traditionnelle qui revient dans les discussions est la suivante :
« J’ai déjà payé mon électricité pour garder à basse température mes aliments, que puis-je faire de la chaleur des condenseurs ? C’est quand même idiot de la rejeter à l’extérieur en période froide alors que je dois en plus chauffer mon magasin ».
Sur base du principe :
« La véritable économie d’énergie est celle que l’on ne consomme pas ! »
On ne recommandera jamais assez de fermer les meubles frigorifiques tout en rappelant qu’un meuble de 1 mètre de largeur (1 mètre linéaire) échange par convection et rayonnement de l’ordre de 800 W et représente les 2/3 de la demande de froid au niveau de l’évaporateur.
Il est sûrement l’heure de rappeler aussi que l’on a atteint le paradoxe de la chaîne alimentaire froide. En effet, on en arrive, depuis un certain temps, à réchauffer les « allées froides » des magasins, et ce, afin d’assurer le confort des clients.
» C’est une aberration énergétique criante ! »
Pour bien illustrer ce petit « coup de gueule », l’étude simplifiée qui suit montre les effets conjugués du succès des meubles frigorifiques d’ouverture de plus en plus imposante avec les effets négatifs qui vont de paire, à savoir :
- le risque accru pour la conservation de la chaîne du froid;
- l’inconfort évident des « allées froides ».
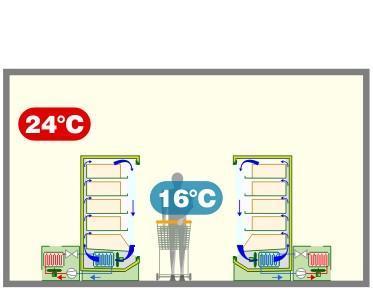
Incorfort dans les allées froides.
Dans ce qui suit, on se propose d’analyser, de manière théorique, différents cas souvent rencontrés dans les magasins d’alimentation :
- des meubles frigorifiques fermés avec le rejet de la chaleur de condensation dans l’ambiance du magasin et un appoint venant d’une chaudière traditionnelle;
- des meubles frigorifiques fermés avec le rejet de la chaleur de condensation à l’extérieur du magasin et le chauffage du magasin venant d’une chaudière traditionnelle;
- des meubles frigorifiques ouverts avec le rejet de la chaleur de condensation dans l’ambiance du magasin et un appoint venant d’une chaudière traditionnelle;
- des meubles frigorifiques ouverts avec le rejet de la chaleur de condensation à l’extérieur du magasin et le chauffage du magasin venant d’une chaudière traditionnelle.
Ici, on analyse les consommations énergétiques finales et primaires ainsi que le bilan CO2 des différentes configurations en tenant compte des valeurs de rendement et d’efficacité énergétiques des équipements :
- La chaudière présente un rendement saisonnier sur PCI (Pouvoir Calorifique Inférieur) de 0.90 (
valeur de la CWaPE ou Commission Wallonne Pour l’Énergie.
).
- Le rendement global des centrales belges est de 55 % (selon la CWaPe). Dans cet exercice, on se place dans une situation défavorable, à savoir que le rendement moyen belge des centrales (en tenant compte du rendement des centrales nucléaires) est plutôt de 38 %.
- 1 kWh de gaz consommé représente 251 g de CO2.
- Le prix actuel du gaz est estimé à 0.05 €/kWh PCI.
- Le prix de l’électricité est évalué à 0.11 €/kWh.
Les conditions d’ambiance du magasin sont simplifiées pour les besoins du calcul, à savoir :
- la température ambiante que le commerçant veut assurer est de 24°C;
- la température moyenne externe est de 6°C;
Le bilan thermique du magasin est aussi simplifié dans le sens où :
- Les déperditions du magasin sont ramenées aux seules pertes des parois de l’enveloppe :
- pour un petit commerce peu isolé de 40 m² au sol (4 façades), avec un Uglobal de l’ordre de 4 W/m².K, les déperditions sont de l’ordre de 12 kW en régime établi;
- pour le même commerce fortement isolé, avec un coefficient Uglobal de l’ordre de 1.2 kW/m².K, les déperditions atteignent 3.6 kW;
- Les apports internes et externes ne sont pas pris en compte (occupations, éclairage, … et l’ensoleillement. On se place donc dans des conditions défavorables au niveau de la récupération de chaleur.
Configuration 1 : meubles ouverts, condenseurs à l’extérieur et commerce peu isolé (configuration classique)
Le commerçant possède un commerce peu isolé (12 kW de déperditions). Il investit dans des meubles frigorifiques ouverts (2 x 10 kW) et les groupes de froid (groupes condenseurs) sont placés à l’extérieur.
La température de condensation des groupes condenseurs en externe est de l’ordre de 22°C pour un air externe moyen sur l’année de 6°C. Le coefficient de performance du groupe condenseur en externe est de 4.2 d’après un constructeur de machine frigorifique (COP’s équivalents donnés par Bitzer software de BITZER et Select 6 de COPELAND).
Pour cette configuration, un appoint de chaleur est nécessaire; c’est la chaudière qui le donne.
Schéma
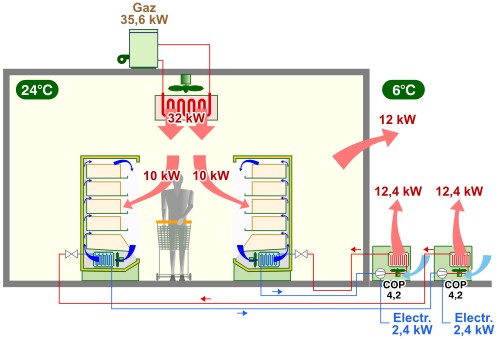
Performance des équipements
Le bilan thermique montre que, vu la bonne performance des compresseurs pour une température de condensation basse (COP de l’ordre de 4.2), les rejets de chaleur à l’extérieur sont limités. Néanmoins, la chaudière doit apporter 32 kW pour maintenir un certain confort dans le magasin et compenser les déperditions de 12 kW au travers des parois et la perte de chaleur vers les meubles frigorifiques ouverts (soit 20 kW).
Bilan énergétique et CO2
Poste |
Calcul |
Unités |
Energie finale (au niveau du magasin) |
|
Energie chaudière |
32/0.9 = 35.6
|
kWh/h
|
|
Energie compresseurs
|
2.4 x 2 = 4.8 |
kWh/h |
|
Energie condenseur |
12.4 x 2 = 24.8 |
kWh/h |
|
Coût |
35.6 x 0.05 + 4.8 x 0.11= 2.3 |
€/h |
Energie primaire (à la centrale électrique) |
|
Energie primaire |
35.6+ 4.8 / 0.38= 48.2 |
kWh/h |
|
CO2 |
48.2 x 0.251 = 12.1 |
kg/h de CO2 |
Configuration 2 : meubles ouverts, condenseurs dans l’enceinte et commerce peu isolé
Le commerçant décide de remplacer ses groupes de condensation, car il sont vétustes (soumis au intempéries depuis 15 ans par exemple). L’installateur lui conseille de les placer à l’intérieur afin de récupérer la chaleur de condensation.
La température de condensation des groupes condenseurs en interne est de l’ordre de 50°C afin de pouvoir chauffer l’air aux environs des 40°C pour une température d’air d’entrée au condenseur de 32°C (condenseur placé dans des mauvaises conditions de fonctionnement). Le coefficient de performance du groupe condenseur est de 1.66 d’après un constructeur de machine frigorifique.
Schéma
Performance des équipements
Le bilan thermique nous montre que les compresseurs, vu leur performance médiocre (COP de 1.7), doivent évacuer plus de chaleur au niveau des condenseurs. Il en résulte que la chaudière, dans ce cas, n’a pas besoin de venir en appoint. La question clef est de savoir s’il faut récupérer la chaleur au prix de la dégradation de la performance énergétique des compresseurs ou l’inverse.
Bilan énergétique et CO2
Poste |
Calcul |
Unités |
Energie finale (au niveau du magasin) |
|
Energie chaudière |
0
|
kWh/h
|
|
Energie compresseurs
|
6 x 2 = 12 |
kWh/h |
|
Energie condenseur |
16 x 2 = 32 |
kWh/h |
|
Coût |
0 x 0.05 + 12 x 0.11= 1.32 |
€/h |
Energie primaire (à la centrale électrique) |
|
Energie primaire |
0 + 12 / 0.38= 31.6 |
kWh/h |
|
CO2 |
31.6 x 0.251 = 7.9 |
kg/h de CO2 |
Configuration 3 : meubles fermés, condenseurs à l’extérieur et commerce peu isolé
Le commerçant est très sensibilisé à l’énergie.
Il décide de réinvestir dans des meubles fermés. Pour une même capacité d’exposition des denrées, la puissance à l’évaporateur sera moindre. En effet, sur base de l’étude du bilan thermique des meubles ouverts, les pertes par l’ouverture représentent de l’ordre de 66 % de la puissance disponible à l’évaporateur. En fermant ces ouvertures, la puissance nécessaire à l’évaporateur est de l’ordre de 2 x 3 kW.
Dans un second temps, il se dit qu’il n’y a plus de nécessité de récupérer la chaleur de condensation puisqu’il devrait y avoir moins de pertes de chaleur vers les meubles frigorifiques. Les groupes de froid (groupes condenseurs) sont donc placés à l’extérieur.
La température de condensation des groupes condenseurs en externe est de l’ordre de 22°C pour un air externe moyen sur l’année de 6°C. Le coefficient de performance du groupe condenseur en externe est de 4.2 d’après le même constructeur de compresseur.
Schéma
Performance des équipements
Le bilan thermique nous montre que, vu la bonne performance des compresseurs pour une température de condensation basse (COP de l’ordre de 4.2), les rejets de chaleur à l’extérieur sont limités. La chaudière doit tout de même apporter 18 kW pour maintenir un certain confort dans le magasin et compenser les déperditions de 12 kW au travers des parois et la perte de chaleur vers les meubles frigorifiques fermés (soit 6 kW).
Bilan énergétique et CO2
Poste |
Calcul |
Unités |
Energie finale (au niveau du magasin) |
|
Energie chaudière |
18/0.9 = 20
|
kWh/h
|
|
Energie compresseurs
|
0.7 x 2 = 1.4 |
kWh/h |
|
Energie condenseur |
3.7 x 2 = 7.4 |
kWh/h |
|
Coût |
20 x 0.05 + 1.4 x 0.11= 1.2 |
€/h |
Energie primaire (à la centrale électrique) |
|
Energie primaire |
20 + 1.4 / 0.38= 23.7 |
kWh/h |
|
CO2
|
23.7 x 0.251 = 5.9 |
kg/h de CO2 |
Configuration 4 : meubles fermés, condenseurs dans l’enceinte et commerce peu isolé
Le commerçant furieux, demande à l’installateur de se débrouiller pour réduire la facture de chauffage. Les groupes de froid sont donc incorporés dans les meubles et la chaleur évacuée par les condenseurs est réintroduite dans le magasin aussi pour assurer le confort des clients (dans les allées froides par exemple).
La température de condensation des groupes condenseurs en interne est de l’ordre de 50°C afin de pouvoir chauffer l’air aux environs des 40°C pour une température d’air d’entrée au condenseur de 32°C. Le coefficient de performance du groupe condenseur est de 1.66 d’après un constructeur de machines frigorifiques.
Schéma
Performance des équipements
Le bilan thermique nous montre que malgré le rejet de 9,2 kW dans l’ambiance du magasin, la chaudière doit apporter 8,8 kW pour maintenir un certain confort dans le magasin et compenser les déperditions de 12 kW au travers des parois et la perte de chaleur vers les meubles frigorifiques fermés (soit 6 kW).
Bilan énergétique et CO2
Poste |
Calcul |
Unités |
Energie finale (au niveau du magasin) |
|
Energie chaudière |
8.4/0.9 = 9.3
|
kWh/h
|
|
Energie compresseurs
|
1.8 x 2 = 3.6 |
kWh/h |
|
Energie condenseur |
4.8 x 2 = 9.6 |
kWh/h |
|
Coût |
8.4 x 0.05 + 3.6 x 0.11= 0.8 |
€/h |
Energie primaire (à la centrale électrique) |
|
Energie primaire |
8.4 + 3.6 / 0.38= 17.9 |
kWh/h |
|
CO2 |
17.9 x 0.251 = 4.5 |
kg/h de CO2 |
Configuration 5 : meubles fermés, condenseurs dans une enceinte très isolée
Le commerçant constate qu’il a encore une facture de chauffage exagérée. Tout en conservant sa configuration précédente, il décide d’isoler son enveloppe (des primes existent). Les déperditions ne sont plus que de 3.6 kW.
La température de condensation des groupes condenseurs en interne est de l’ordre de 50°C afin de pouvoir chauffer l’air aux environs des 40°C pour une température d’air d’entrée au condenseur de 32°C. Le coefficient de performance du groupe condenseur est de 1.66 d’après un constructeur de machine frigorifique.
Schéma
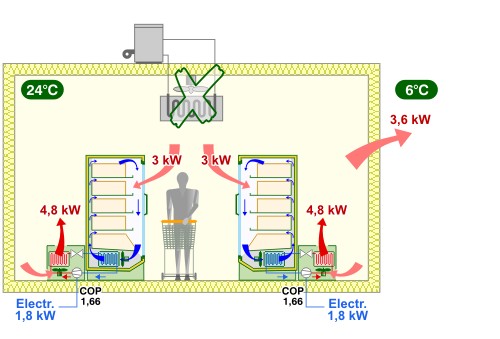
Performance des équipements
Le bilan thermique nous montre que le rejet de 9,6 kW dans l’ambiance du magasin permet à la chaudière de ne pas être allumée et compenser, non seulement les 6 kW pris par les meubles frigorifiques, mais aussi les 3.6 kW de déperdition au travers des parois.
On a donc affaire à une pompe à chaleur dont :
- la source froide (la source d’où provient l’énergie) est chaude puisque dans l’ambiance;
- à la consommation près du compresseur, l’énergie, « tournant » sur elle-même, est utilisée pour refroidir les meubles frigorifiques et, après utilisation, est restituée à l’ambiance;
- la chaleur de compression excédentaire sert en fait à compenser les déperditions au travers des parois de l’enveloppe.
Bilan énergétique et CO2
Poste |
Calcul |
Unités |
Energie finale (au niveau du magasin) |
|
Energie chaudière |
0
|
kWh/h
|
|
Energie compresseurs
|
1.8 x 2 = 3.6 |
kWh/h |
|
Energie condenseur |
4.8 x 2 = 9.6 |
kWh/h |
|
Coût |
3.6 x 0.11= 0.4 |
€/h |
Energie primaire (à la centrale électrique) |
|
Energie primaire |
3.6 / 0.38= 9.5 |
kWh/h |
|
CO2 |
9.5 x 0.251 = 2.4 |
kg/h de CO2 |
Synthèse
Tableau comparatif
Configuration |
Enveloppe |
Type de meuble |
Condenseur |
Energie finale consommée chaudière [kWh/h] |
Energie finale électrique consommée [kWh/h] |
Energie primaire consommée [kWh/h] |
Coût de l’énergie [€/h] |
kg/h de CO2 |
Rejet de CO2 |
1 |
peu isolée |
ouverts |
externe |
35.6 |
4.8 |
48.2 |
2.3 |
12.1 |
+504 % |
2 |
peu isolée |
ouverts |
interne |
0 |
12 |
31.6 |
1.32 |
7.9 |
+329 % |
3 |
peu isolée |
fermés |
externe |
20 |
1.4 |
23.7 |
1.2 |
5.9 |
+246% |
4 |
peu isolée |
fermés |
interne |
9.3 |
3.6 |
17.9 |
0.8 |
4.5 |
+188 % |
5 |
bien isolée |
fermés |
interne |
0 |
3.6 |
9.5 |
0.4 |
2.4 |
0 |
Choix des meubles frigoriques fermés
La toute première conclusion à tirer est qu’il faut choisir des meubles frigorifiques fermés quel que soit le type de denrée exposé. À ce sujet, au risque de passer pour des doux rêveurs, c’est possible de choisir des meubles tant en froid positif qu’en froid négatif avec des portes sans trop de risque pour que le chiffre d’affaires tombe en chute libre.
Energie finale
Le graphique ci-dessous montre l’évolution des énergies finales que consomment l’installation de froid avec récupération ou sans récupération et le système de chauffage.
Ces consommations énergétiques sont celles que le commerçant peut retrouver à partir de ses factures de chauffage et d’électricité.
Récupération importante par rapport aux besoins de chaleur
Le tableau comparatif précédent permet de tirer des conclusions :
- Il faut fermer les meubles frigorifiques ouverts.
- En période froide, même si la performance énergétique des compresseurs est dégradée (COP de 1.66) vu que la température de condensation (le condenseur se trouve à l’intérieur) est élevée, il est intéressant de récupérer l’énergie de condensation. L’optimum se situe naturellement lorsque la chaleur rejetée par les condenseurs équivaut aux déperditions des parois de l’enveloppe du commerce;
- En plus de récupérer la chaleur, on aura donc intérêt à limiter au maximum les déperditions de l’enveloppe qu’elles soient sous forme :
- d’une meilleure isolation;
- d’un meilleur contrôle des infiltrations au niveau des portes d’entrée et des réserves;
- d’une gestion efficace de la ventilation de l’air hygiénique.
Régime en période chaude
Là où le bât blesse, c’est pendant les périodes chaudes :
Les condenseurs étant incorporés aux meubles frigorifiques ou dans l’enceinte même du magasin, lorsque les déperditions au travers des parois s’inversent (période chaude, apport solaire important, …), il est nécessaire d’évacuer la chaleur des condenseurs à l’extérieur. Dans le cadre d’une installation de récupération de chaleur sur un condenseur à air, il n’est pas aisé de le réaliser.
Pour récupérer la chaleur de condensation, Delhaize, par exemple, a mis au point un système similaire à celui représenté dans les figures suivantes permettant de récupérer la chaleur en période froide pour chauffer l’ambiance.
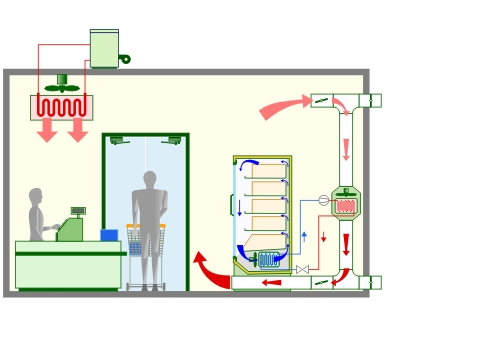
Schéma de principe en période froide (récupération); source : Delhaize.
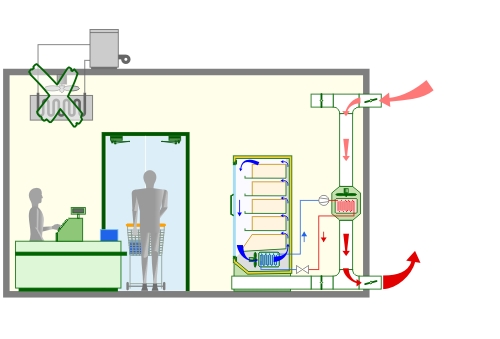
Schéma de principe en période chaude (pas de récupération); source : Delhaize.
Bilan des énergies primaires
Dans le tableau de synthèse ci-dessus, on parle aussi d’énergie primaire. Ce bilan est moins parlant, car, surtout au niveau de l’énergie électrique, on a souvent tendance à oublier que nos centrales électriques ont aussi un rendement.
Comme précisé dans les hypothèses, le rendement global, selon les sources, est de 55 ou 38 % suivant que l’on compte ou non les centrales nucléaires dans le parc des centrales belges. Ce qui signifie que lorsqu’on consomme 1 kWh d’énergie électrique chez nous les centrales, elles, en consomment 1 / 0,38 = 2,63 kWh sous forme de gaz, de nucléaire, de biomasse, …
Quant à l’énergie primaire consommée par notre chaudière (c’est plus facile), c’est le gaz, le fuel, le m³ de bois consommé.
Le graphique suivant montre cette approche :
Bilan CO2
À partir des énergies primaires, on peut déterminer quelle sera notre production de CO2 :
Remarques
La plupart des cas présentés ci-dessus, sont issus de cas réellement observés. Malheureusement, aucun monitoring des consommations n’est disponible à l’heure actuelle. Il va de soi que le placement d’une batterie de chauffe au dessus de la tête des clients dans l’allée froide n’est pas un bon principe, mais est juste utilisé comme moyen d’interprétation ou de réaction des lecteurs. Ce principe donne les avantages et inconvénients suivants:
|
(+)
(-)
- nécessite des vitesses d’air plus importantes afin d’amener l’air chaud à environ 1.5 m du sol pour assurer un certain confort thermique des clients;
- augmente l’induction de l’air chaud au niveau du rideau d’air, car le mouvement de l’air dans cette zone est amplifié;
- …
|