Connaissant PMV, la figure ci-après permet d’évaluer directement PPD. Si par exemple, le PMV est de – 1 ou + 1, l’indice PPD montre que près de 25 % de la population n’est pas satisfaite. Pour ramener le PPD à une valeur maximale de 10 % (ce qui est généralement l’objectif à atteindre dans un bâtiment), le PMV doit se situer entre – 0,5 et + 0,5. Et pour une valeur 0 de PMV, soit un état de confort thermique optimal, il y a encore 5 % d’insatisfaits.
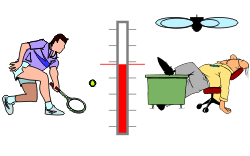
Le calcul du niveau de confort
Les mesures étant réalisées, le niveau d’habillement et le niveau d’activités étant connus, il est alors possible de déterminer où se situe la température opérative effective par rapport à l’optimum de confort.
De façon plus précise, des tableaux repris dans la norme donnent l’indice PMV en fonction de la vitesse relative de l’air pour un habillement et une température opérative donnés, lorsque l’humidité relative est de 50 %. Nous reprenons ci-dessous un exemplaire de ces tableaux pour la situation la plus fréquente en hiver. Dans celui-ci est mise en évidence (zone colorée) la zone de confort thermique pour un indice PMV situé entre – 0,5 et + 0,5, c’est-à-dire pour 10 % d’insatisfaits.
Hab. H (clo)
|
Temp. opér. to (°C)
|
PMV suivant la vitesse relative de l’air (m/s)
– Niveau d’activité M = 70 W/m² –
|
<0,10
|
0,10
|
0,15
|
0,20
|
0,30
|
0,40
|
0,50
|
1,00
|
1,50
|
0,5
(été)
|
18
|
-2,01
|
-2,01
|
-2,17
|
-2,38
|
-2,70
|
–
|
–
|
–
|
–
|
20
|
-1,41
|
-1,41
|
-1,58
|
-1,76
|
-2,04
|
-2,25
|
-2,42
|
–
|
–
|
22
|
-0,79
|
-0,79
|
-0,97
|
-1,13
|
-1,36
|
-1,54
|
-1,69
|
-2,17
|
-2,46
|
24
|
-0,17
|
-0,20
|
-0,36
|
-0,48
|
-0,68
|
-0,83
|
-0,95
|
-1,35
|
-1,59
|
26
|
0,44
|
0,39
|
0,26
|
0,16
|
-0,01
|
-0,11
|
-0,21
|
-0,52
|
-0,71
|
28
|
1,05
|
0,96
|
0,88
|
0,81
|
0,70
|
0,61
|
0,54
|
-0,31
|
-0,16
|
30
|
1,64
|
1,57
|
1,51
|
1,46
|
1,39
|
1,33
|
1,29
|
1,14
|
1,04
|
32
|
2,25
|
2,20
|
2,17
|
2,15
|
2,11
|
2,09
|
2,07
|
1,99
|
1,95
|
1,0
(hiver)
|
16
|
-1,18
|
-1,18
|
-1,31
|
-1,43
|
-1,59
|
-1,72
|
-1,82
|
-2,12
|
-2,29
|
18
|
-0,75
|
-0,75
|
-0,88
|
-0,98
|
-1,13
|
-1,24
|
-1,33
|
-1,59
|
-1,75
|
20
|
-0,32
|
-0,33
|
-0,45
|
-0,54
|
-0,67
|
-0,76
|
-0,83
|
-1,07
|
-1,20
|
22
|
0,13
|
0,10
|
0,00
|
-0,07
|
-0,18
|
-0,26
|
-0,32
|
-0,52
|
-0,64
|
24
|
0,58
|
0,54
|
0,46
|
0,40
|
0,31
|
0,24
|
0,19
|
0,02
|
-0,07
|
26
|
1,03
|
0,98
|
0,91
|
0,86
|
0,79
|
0,74
|
0,70
|
0,57
|
0,50
|
28
|
1,47
|
1,42
|
1,37
|
1,34
|
1,28
|
1,24
|
1,21
|
1,12
|
1,06
|
30
|
1,91
|
1,86
|
1,83
|
1,81
|
1,78
|
1,75
|
1,73
|
1,67
|
1,63
|
Partons d’un exemple de mesures
Dans un local de bureau où l’activité est légère et s’effectue en position assise, le métabolisme est de 70 W/m² ou 1,2 met. Supposons être en présence d’une personne en tenue d’intérieur pour l’hiver correspondant à un habillement de 1 clo. Les différentes mesures des paramètres physiques de l’ambiance donnent 20°C pour la température de l’air, 19°C pour la température moyenne de surface des parois, une humidité relative de 50 % et une vitesse de l’air de 0,15 m/s.
La température opérative est donc de 19,5°C. En se référant au tableau de la norme ci-dessous, on en déduit que l’indice PMV = – 0,56. Pour cette dernière valeur, le graphe PPD/PMV donne une prévision de 12 % de personnes insatisfaites par rapport à l’ambiance thermique du local.
Cherchons le confort optimal
Dans le cas de la détermination de la température d’ambiance optimale, l’objectif est de déterminer la température opérative optimale qui correspond à l’indice PMV = 0. Ensuite, la zone de confort thermique peut alors être établie pour un pourcentage de personnes insatisfaites donné.
En reprenant les mêmes hypothèses que l’exemple ci-dessus, la norme donne un indice PMV = 0 pour une température opérative optimale de 22°C. En admettant un écart de 1°C entre T°air et T°parois (ce qui n’est pas beaucoup), la température de l’air sera optimale pour 22,5°C !
En admettant 10 % d’insatisfaits (PMV compris entre – 0,5 et + 0,5), la température opérative varie de 19,8°C et 24,2°C. Soit pour la température de l’air : une zone de confort thermique de 4,4°C, allant de 20,3°C à 24,7°C (zone de couleur jaune du tableau).
Autrement dit, en hiver, dans un bureau bien isolé (T°parois élevées), on admettra un confort basé sur une température d’air de 20,5°C. Mais si la température des parois est faible (simples vitrages, par exemple), il faudra apporter un air à 21, voire 22°C pour assurer le confort.
Le confort thermique restera toujours variable en fonction des individus
La zone théorique de confort étant déterminée, la sensation de confort peut aussi être influencée par d’autres éléments comme l’état de santé, l’âge ou l’état psychologique de l’individu. Dans chacun de ces cas, il faudra admettre une température d’ambiance différente qui peut être située hors de la zone de confort thermique. De plus, la qualité ou « chaleur » humaine qui entoure l’individu participe à la sensation de confort ou d’inconfort. Enfin, la possibilité d’une intervention personnelle sur les caractéristiques de l’ambiance de son lieu d’activité est importante si on veut éviter tout sentiment de frustration ou d’enfermement et donc d’inconfort.
Confort au niveau du pied
Le texte ci-dessous est extrait de la brochure du FFC : Technologie de la construction – Méthodes de construction – Isolation thermique – Généralités.
Bien que dans les échanges thermiques, les pertes par contact (conduction) soient négligeables (< 1 %), une problématique courante réside dans le fait qu’avec certains types de plancher, on aura froid aux pieds et non avec d’autres. On admet en général que, pour un pied non chaussé, une température de contact inférieure à 26°C soit désagréable.
Lorsqu’un objet à une température θ1 est mis en contact avec un objet à une température q2, la surface de contact se mettra à une température comprise entre les deux précitées.
Les relations ci-après permettent de calculer la température de contact ( θc) entre le corps humain et quelques matériaux :
Acier : |
θC |
= |
2,1 + 0,93 θ |
Béton : |
θC |
= |
10,6 + 0,65 θ |
Bois : |
θC |
= |
19,4 + 0,35 θ |
Tapis : |
θC |
= |
27,5 + 0,08 θ |
θ est la température initiale du matériau. |
Ainsi, si on touche un objet en acier dont la température est inférieure à – 2,2°C, la température de contact sera inférieure à 0°C. Ceci explique pourquoi, si en période de gel, des enfants touchent avec la langue un garde-corps de pont en acier par exemple, celle-ci adhérera par le gel.
Il ressort de la relation θC = 27,5 + 0,08 θ , que pour toutes les températures courantes, un tapis est suffisamment chaud aux pieds. De même, un plancher en bois ne fera généralement pas l’objet de plaintes pour autant que la température de surface ne descende pas sous 19°C.
Par contre, un revêtement de sol en béton ou en dalles ne sera chaud aux pieds que si la température est au moins de 24°C. C’est pourquoi ces types de planchers font souvent l’objet de plaintes auxquelles on ne peut remédier que par la pose d’un tapis ou l’installation d’un système de chauffage par le sol.
Conseiller d’isoler, à sa face inférieure, un plancher en matériau pierreux afin d’augmenter le confort du pied est généralement peu judicieux. Quelle que soit l’isolation, des températures superficielles de 24°C ou plus ne peuvent être atteintes qu’avec une température de l’air de 27 °C, ce qui crée par ailleurs un certain inconfort.
Zones de confort adaptatif
Comme l’a montré la théorie du confort adaptatif, les plages de confort ne devraient pas être vues comme des valeurs statiques, définies une fois pour toutes. En réalité, elles sont susceptibles de varier selon la capacité d’action de l’occupant, l’historique météorologique, etc. C’est déjà partiellement reflété par l’intégration de l’habillement et de l’activité dans les représentations traditionnelles, mais cela reste trop partiel.
Il faut reconnaitre qu’il est difficile de représenter clairement une zone de confort définie sur base de six paramètres, en intégrant en plus la variabilité de ceux-ci. Heureusement, les recherches ont montré que parmi ces 6 paramètres, la température opérative était prédominante, et que la plupart des facteurs d’adaptation sont liés à la température moyenne extérieure. Les développeurs des théories du confort adaptatif ont donc pu simplifier la représentation de leurs résultats. On trouve aujourd’hui dans la littérature des figures donnant des plages de confort intérieur, exprimées uniquement sur base de la température opérative, en fonction d’une température de référence, généralement définie comme une moyenne des températures relevées sur quelques jours. Certains auteurs font cependant remarquer que ces représentations sont trop simplistes et font oublier les autres paramètres du confort thermique, notamment l’humidité.
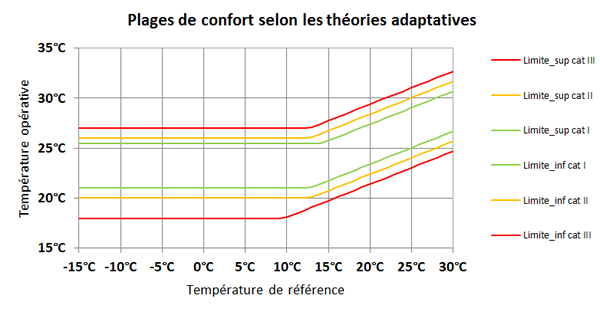
Températures opératives correspondantes aux différentes plages de confort définies par la norme NBN EN 15251.
En outre, ces plages de références ne sont utilisables que pour certains ‘profils de bâtiment’, et surtout d’occupants. Les théories du confort adaptatif l’on montré, la capacité d’action de l’occupant sur son environnement est un paramètre fondamental du confort. Il est donc nécessaire d’en tenir compte lorsque l’on choisit des systèmes techniques : va-t-on privilégier une gestion automatisée et centralisée, pour éviter « des mauvaises gestions » (oh, le méchant occupant qui dérègle ma belle machine !), ou au contraire choisir un système laissant à l’occupant la totalité du contrôle ? Bien entendu des solutions intermédiaires existent.
La capacité d’action de l’occupant ne dépend pas uniquement des dispositifs techniques. Elle est aussi liée à son activité ou à l’organisation du travail. Par exemple, on imaginera assez facilement un employé de bureau passant 8 heures continues à son poste de travail contrôler l’ouverture de la fenêtre située juste à côté de lui. Ce sera plus difficile pour quelqu’un qui saute d’une réunion à l’autre et n’a pas de poste de travail fixe.
On parlera d’un occupant actif s’il est capable et motivé à prendre en charge une partie de la gestion de l’ambiance, et d’un occupant passif dans le cas contraire. L’organigramme ci-dessous aide à identifier le type d’occupant auquel on a affaire.
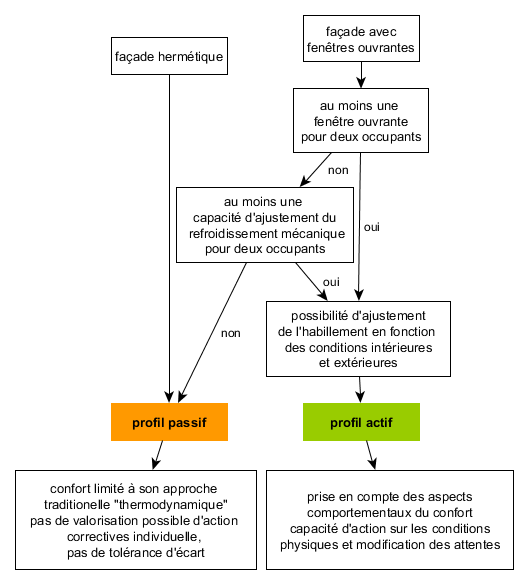
Profil des occupants, inspiré de Adaptive temperature limits: A new guideline in The Netherlands : A new approach for the assessment of building performance with respect to thermal indoor climate, A.C. van der Linden, A.C. Boerstra, A.K. Raue, S.R. Kurvers, R.J. de Dear.