Une manière souvent utilisée pour classifier les meubles frigorifiques, est de se baser sur la puissance frigorifique spécifique ou la puissance frigorifique :
- par mètre linéaire;
- ou par module de porte en fonction des conditions classiques définies par EUROVENT (température d’ambiance de 25°C et une humidité relative de 60 %).
Meuble frigorifique à applications positives
Famille de meubles |
Surface d’exposition [m²/ml] |
Température de service [°C] |
Puissance frigorifique spécifique [kW/ml] |
Vitrine service par le personnel en convection naturelle |
0,8 |
2 à 4 |
0,2 à 0,25 |
Vitrine service par le personnel en convection forcée |
0,25 à 0,28 |
Comptoir horizontal self-service en convection |
0,9 |
0 à 2 |
0,4 à 0,43 |
Meuble vertical self-service en convection forcée |
1,3 |
4 à 6 |
1,2 à 1,3 |
Meuble frigorifique à applications négatives
Famille de meubles |
Type de rideau d’air |
Surface d’exposition [m²/ml] ou [m²/porte] |
Température de service [°C] |
Puissance frigorifique spécifique [kW/ml] |
Gondole self-service en convection forcée |
horizontale, asymétrique, laminaire |
0,8 |
-18 à -20 |
0,42 à 0,45 |
Vitrine service par le personnel en convection forcée |
horizontal, asymétrique, laminaire |
1,1 |
-23 à -25 |
0,63 à 0,67 |
Meuble vertical self-service en convection |
verticale, à 3 flux parallèles, turbulents |
1,1 |
-18 à -20 |
1,9 à 2,1 |
Meuble vertical self-service en convection forcée |
portes vitrées, rideau d’air interne turbulent |
0,84 |
-23 à -25 |
0,8 0,86 |
Température
La puissance frigorifique est toujours liée à une température d’évaporation qui permet de tenir la température de consigne au sein du meuble frigorifique.
Type de meuble |
Température de service interne au meuble frigorifique [°C] |
Température de l’évaporateur[°C] |
Froid positif |
+6/+8 |
-3 à -5 |
+4/+6 |
-4 à -10 |
+2/+4 |
-6 à -12 |
0/+2 |
-8 à -14 |
Froid négatif |
-18/-20 |
-30 à -35 |
-23/-25 |
-33 à -38 |
Bilan énergétique par simulation
Les valeurs des bilans énergétiques sont des valeurs approchées instantanées qui ne tiennent pas compte des variations du climat intérieur au magasin lui-même influencé par des paramètres tels que :
- les conditions climatiques externes (températures, humidité, ensoleillement, vent, pluie, …);
- le profil d’occupation du magasin;
- les apports internes (rayon HiFi, type d’éclairage et leur gestion, …);
- …
Une simulation a été réalisée à partir de TRNSYS (logiciel de simulation dynamique du comportement thermique des bâtiments en fonction du climat externe) en modélisant une surface de 2 000 m². On tient compte :
- de la composition des parois de l’enveloppe;
- des systèmes de ventilation, de chauffage, de climatisation et de leur gestion;
- de l’occupation des surfaces de vente, des réserves, … (profil d’occupation hebdomadaire);
- des apports internes d’éclairage, …;
Apports en fonction de la température externe
Sur une année climatique de référence (8 760 heures) les apports tant internes qu’externes varient en permanence. Les agressions thermiques, elles aussi, changent. En quelle proportion ? C’est ce que la simulation dynamique tente de montrer.
Simulation
Il est extrêmement rare que des meubles frigorifiques soient dans des conditions de fonctionnement nominal. Une manière d’évaluer les variations de la puissance frigorifique nécessaire au meuble frigorifique pour assurer la continuité de la chaîne de froid (température constante) en fonction des agressions thermiques, est de décortiquer les différentes puissances quand le climat interne au magasin varie. Bien que les systèmes HVAC (Heating Ventilation Air Conditioning) soient prévus pour assurer le confort du personnel et des clients au sein des zones de vente et, par conséquent, capables de maintenir un climat stable dans le magasin, les variations de températures et d’humidité sont inévitables de par :
- les apports internes,
- les courants d’air;
- le climat externe ;
- ….
Une manière intéressante de quantifier les variations relatives des apports aux meubles, est de voir leur évolution pour une semaine en période froide et chaude.
Période froide
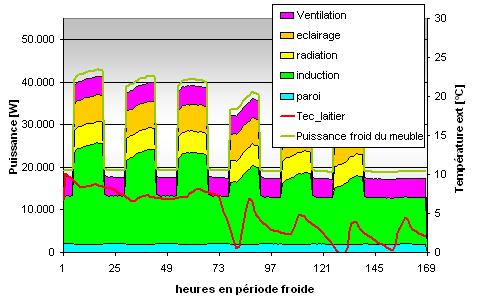
Sur le graphe ci-dessus, l’évolution des apports est représentée sur une période d’une semaine. On constate que :
- le climat intérieur évolue en fonction du climat externe et des apports internes. On voit en effet les apports évoluer selon plus ou moins le même profil que la température externe. Le déphasage et la pente différente de la courbe de température externe résultent respectivement de l’inertie du bâtiment et des denrées et de la variation différente des apports internes liés à l’activité du magasin;
- lors de l’inactivité du magasin (en dehors des heures d’ouverture de semaine et le dimanche), les apports sont fortement réduits de par la pose des rideaux de nuit et de la coupure de l’éclairage;
- les apports par induction au travers du rideau d’air sont importants; ce sont eux qui sont fortement influencés par les conditions d’ambiance internes et indirectement externes.
Période chaude
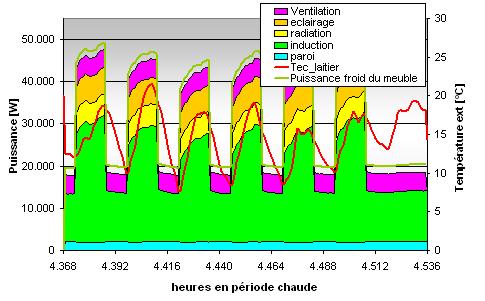
De même que pour la période froide, sur le graphe ci-dessus, l’évolution des apports est représentée sur une période d’une semaine en période chaude. On constate de nouveau que :
- les apports par induction prennent la mesure sur les autres apports. Il est donc important d’optimiser le rideau d’air.
Puissance frigorifique
Le graphe ci-dessous exprime la variation des apports en fonction de la température extérieure. Le total représente la puissance nécessaire à l’évaporateur pour combattre les apports tant internes qu’externes au meuble frigorifique.
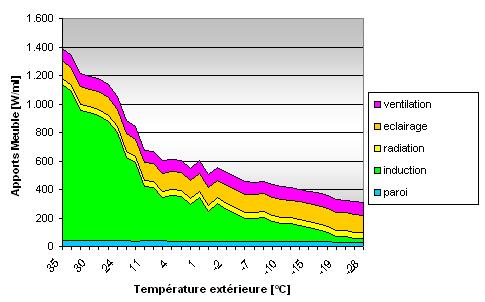
Commentaires
On constate qu’effectivement c’est l’induction de l’air de la zone de vente par le rideau d’air du meuble qui varie en fonction du climat externe. La puissance à l’évaporateur peut atteindre :
-
en période de canicule, de 1 200 à 1 400 [W/ml];
-
en période froide normale, de 400 à 600 [W/ml].
Au vu de ces valeurs, la sollicitation de la machine frigorifique (compresseur principalement) risque d’être importante non seulement au niveau de l’évaporateur, mais aussi au niveau du condenseur (directement influencé par les conditions climatiques externes).
Influence du rideau d’air
Comme souvent mentionné ci-avant, le point faible des meubles frigorifiques ouverts est naturellement la difficulté de maintenir une température interne basse au sein du meuble par rapport à une ambiance des zones de vente de l’ordre de 20 °C, soit un écart de température pouvant aller jusqu’à 50 °C voir plus dans certaines conditions.
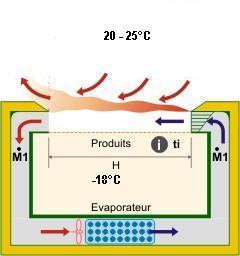
Écart de température au niveau des meubles frigorifiques positif et négatif.
Problèmes liés aux meubles frigorifiques ouverts
Les meubles horizontaux
Les meubles frigorifiques horizontaux sont dans une situation instable dans le sens où :
- un rien (courant d’air, chargement, …) peut perturber l’équilibre par rapport à la différence de densité entre l’air chaud au dessus de l’ouverture du meuble qui a tendance à monter et l’air froid plus lourd qui a, quant à lui, tendance à vouloir descendre et rester confiné dans le meuble (effet baignoire). Ceci est vrai d’autant plus que le volume utile du meuble est rempli de denrées;
- comme un meuble frigorifique ouvert agit comme un véritable déshumidificateur de l’air ambiant (la pression partielle de l’air dans le meuble est plus faible que celle dans l’air ambiant de la zone de vente), du givre, de la neige ou encore de la glace se forme sur les denrées.
Les meubles verticaux
Les meubles frigorifiques verticaux sont aussi dans une situation instable dans le sens où :
- le froid du meuble s’écoule vers l’extérieur par l’ouverture;
- la quantité, la masse (inertie) et la position des denrées influencent cet écoulement. En situation réelle, le contrôle de l’écoulement est très difficile à maîtriser vu le mouvement incessant des denrées, des mains pour les prendre, les courants d’air souvent présent dans les zones de vente, …
Une solution partielle : les rideaux d’air
Les rideaux d’air vont donc tenter de « désensibiliser » les meubles frigorifiques ouverts par rapport aux perturbations externes et par la même occasion réduire les déperditions thermiques de l’ambiance vers l’intérieur du meuble.
Bilan hygrothermique d’un meuble horizontal à flux asymétrique
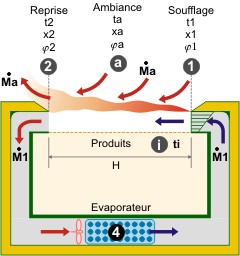
Humidité : l’établissement du bilan de l’humidité est primordial afin de réduire au maximum les échanges de vapeur d’eau entre l’ambiance externe et le meuble et, par conséquent, diminuer les quantités de givre, de glace et de neige au niveau principalement fixées sur l’évaporateur.
Bilan de l’humidité (sortie bouche = entrée reprise)
M*1 x (x1)+ M*a x (xa) = M*1 x (x2)+ M*a x (x2)
avec :
- M*1 : débit massique du rideau d’air [kg/s];
- x1 : humidité absolue du rideau d’air au soufflage [geau/kg d’air sec];
- M*a : débit massique de l’air extérieur au meuble induit par le rideau d’air [kg/s];
- xa : humidité absolue de l’air extérieur au meuble induit par le rideau d’air[geau/kg d’air sec];
- x2 : humidité absolue du rideau d’air à la reprise [geau/kg d’air sec];
|
Thermique : de même, l’établissement du bilan thermique permet de minimiser les échanges entre l’ambiance et l’intérieur du meuble.
Bilan thermique (sortie bouche = entrée reprise)
M*1 x h1+ M*a x ha + Qdenrées= M*1 x h2 + M*a x h2
avec :
- Qdenrées+parois exposées= chaleur emmagasinée par les denrées et les parois du dessus du volume de chargement en vis à vis des parois rayonnantes (plafond par exemple) et en contact avec le rideau d’air.
- M*1 : débit massique du rideau d’air [kg/s];
- h1 : enthalpie du rideau d’air au soufflage [kJ/kg d’air];
- M*a : débit massique de l’air extérieur au meuble induit par le rideau d’air [kg/s];
- ha : enthalpie de l’air extérieur au meuble induit par le rideau d’air[kJ/kg d’air];
- h2 : enthalpie du rideau d’air à la reprise [kJ/kg d’air];
|
Taux d’induction : il caractérise l’efficacité du rideau d’air, soit :
Taux d’induction
X = M*a / M*1
avec :
- M*a : débit massique d’air [kg/s] ambiant induit par le rideau d’air;
- M*1 : débit massique d’air [kg/s] du rideau d’air;
Il peut aussi s’exprimer par les relations suivantes :
taux d’induction X = x2 – x1 / xa – x2
ou encore
taux d’induction X = t 2 – t 1 / ta – t2
avec :
- x : masse d’eau dans de l’air sec [g d’eau / kg d’air sec];
- t :température prise en compte [°C].
|
On voit tout de suite qu’un rideau d’air efficace a une valeur de taux d’induction faible. Des taux d’induction de l’ordre de 0,05 à 0,06 sont couramment rencontrés dans la pratique.
Bilan hygrothermique d’un meuble vertical à flux vertical symétrique
Pour les meubles frigorifiques verticaux, c’est le même principe de raisonnement pour déterminer le bilan hygrothermique :
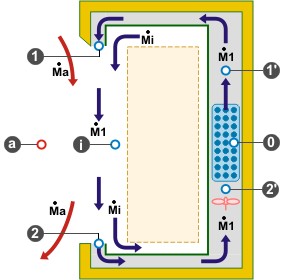
Humidité :
Bilan de l’humidité (sortie bouche = entrée reprise)
M*1 x (x1)+ M*a x (xa) + M*i x (xi)= M*1 x (x2)+ M*a x (x2) + M*i x (x2)
- M*1 : débit massique du rideau d’air [kg/s];
- x1 : humidité absolue du rideau d’air au soufflage [geau/kg d’air sec];
- M*a : débit massique de l’air extérieur au meuble induit par le rideau d’air [kg/s];
- M*i : débit massique de l’air interne au meuble induit par le rideau d’air [kg/s];
- xa : humidité absolue de l’air extérieur au meuble induit par le rideau d’air [geau/kg d’air sec];
- x2 : humidité absolue du rideau d’air à la reprise [geau/kg d’air sec];
- xi : humidité absolue à l’intérieur du meuble [geau/kg d’air sec];
|
Thermique : de même, l’établissement du bilan thermique permet de minimiser les échanges entre l’ambiance et l’intérieur du meuble.
Bilan thermique (sortie bouche = entrée reprise)
M*1 x (h1)+ M*a x (ha) + M*i x (hi)= M*1 x (h2)+ M*a x (h2) + M*i x (h2)
avec :
- M*1 : débit massique du rideau d’air [kg/s];
- h1 : enthalpie du rideau d’air au soufflage [kJ/kg d’air];
- M*a : débit massique de l’air extérieur au meuble induit par le rideau d’air [kg/s];
- M*i : débit massique de l’air interne au meuble induit par le rideau d’air [kg/s];
- ha : enthalpie de l’air extérieur au meuble induit par le rideau d’air[kJ/kg d’air];
- h2 : enthalpie du rideau d’air à la reprise [kJ/kg d’air];
- hi : enthalpie de l’air intérieur au meuble induit par le rideau d’air[kJ/kg d’air];
|
Taux d’induction : il caractérise l’efficacité du rideau d’air, soit :
Taux d’induction
X = M*a / M*1
si M*i = M*a (flux symétrique) ainsi que xi = x1 (denrées emballées)
avec :
- M*a : débit massique d’air [kg/s] ambiant induit par le rideau d’air;
- M*1 : débit massique d’air [kg/s] du rideau d’air;
- M*i : débit massique d’air [kg/s] à l’intérieur du meuble induit par le rideau d’air;
Le taux d’induction peut aussi s’exprimer par les relations suivantes :
Taux d’induction
X = x2 – x1 / (xa – x2) – (x2 – x1)
ou encore
Taux d’induction
X = h 2 – h 1 / (ha – h2) – (h2 – h 1)
avec :
- x : masse d’eau dans de l’air sec [g d’eau / kg d’air sec];
- h : enthalpie de l’air [kJ/kg d’air].
|
Un taux d’induction souvent rencontré dans la pratique se situe aux alentours des 0,1 à 0,2.
Influence de l’évaporateur
Il est important qu’un évaporateur soit bien dimensionné pour combattre les apports thermiques du meuble. Une surface d’échange insuffisante entraîne une saturation de l’évaporateur en température. Pour des applications proche de 0°C, la prise en glace ou le givrage est plus rapide entraînant une surconsommation du meuble.
La figure suivante représente l’évolution des températures, à la fois pour l’air qui passe au travers des ailettes d’échange et le fluide frigorigène au travers des tuyauteries :
- au fur et à mesure que l’air traverse les différents rangs d’ailettes, sa température diminue selon une loi logarithmique et passe de la température t1 à la température t2;
- par contre, le fluide frigorigène se vaporise tout au long du trajet inverse à température plus ou moins constante (suivant le type de fluide utilisé) et ce, jusqu’au moment où la dernière goutte liquide devient gazeuse (point c où le titre du fluide Xr = 1 : 1 correspond à un fluide totalement gazeux). À partir de ce point, le fluide frigorigène entre dans sa phase de surchauffe et voit sa température augmenter (segment c-d).
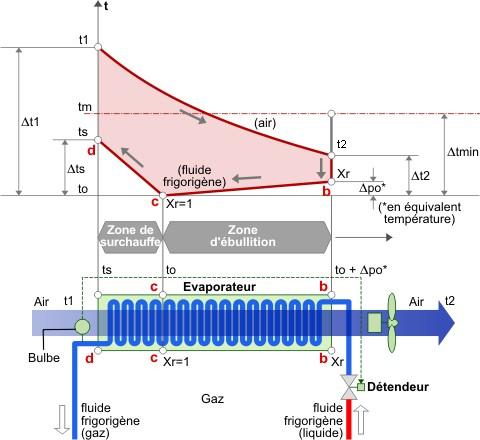
L’évaporateur est principalement caractérisé par sa puissance frigorifique :
Po = K0 x Séchange x Δtmln
|
et dépendant des paramètres suivants :
Le coefficient global d’échange moyen K0[W/m².K) s’exprimant sous la forme :
K0 = f1 / ((Séchange / (Si x αi)) + (1 / (Φ x αe))
avec :
- f1: coefficient tenant compte de la chaleur latente intervenant dans le givrage des ailettes d’échange (soit f1 = 1.25 pour le froid positif et 1,05 pour le froid négatif);
- Φ: rendement global de la surface d’échange Séchange (Φ ~ 0,65 pour la convection forcée et ~0,75 en convection naturelle pour des échangeurs standards);
- αe : coefficient d’échange moyen par convection pour les surfaces externes.Il est difficile à calculer, mais dépend principalement de la vitesse moyenne de l’air au travers des ailettes (0,6 < vm < 1,2 m/s) et du pas des ailettes (espace entre deux ailettes). En écoulement laminaire, αe est compris entre 11 et 23 W/m².K et en écoulement turbulent entre 13 et 45 W/m².K;
- αi : coefficient d’échange moyen interne lors de l’ébullition sèche du fluide frigorigène. Lui aussi est très complexe à déterminer, mais dépend principalement du type de fluide frigorigène, de son débit et du diamètre des conduites de l’évaporateur. On parle de 850 à 1 800 W/m².K.
|
La surface d’échange côté air de l’échangeur Séchange [m²] :
Séchange ~ 2 x VE / pas
avec :
- VE: volume de l’évaporateur [m³];
- pas: espace entre deux ailettes [m].
|
L’écart moyen logarithmique de température Δtmln* corrigé défini par la relation suivante :
Δtmln* = 0,95 x f2 x ((t1 – t2)/ ln ((t1 – tfluide_frigorigène) / (t2 – tfluide_frigorigène))) [K]
avec :
- f2 : coefficient correcteur tenant compte de la surchauffe à la sortie de l’évaporateur
- t1 : température entrée évaporateur [K];
- t2 : température sortie évaporateur [K];
- tfluide_frigorigène ou t0: température entrée évaporateur [K];
|
Influence du givrage
Principe de givrage
L’humidité de l’air ambiant de la zone de vente passant au travers du rideau d’air migre naturellement vers les parties froides du meuble et plus particulièrement vers l’évaporateur. Cette humidité se condense et givre sur les ailettes pour les applications de froid commercial (même pour les applications « positives », la température d’évaporation est négative par exemple -10°C). Dans des applications de congélation, il arrive que l’humidité dans l’air se transforme directement en cristaux de neige qui peuvent se fixer par exemple et malheureusement sur les pales des ventilateurs de manière non homogène pouvant entraîner la destruction des ventilateurs (« balourd »).

Formation de givre.
La formation de givre entraîne une réduction de la puissance frigorifique P0 suite à :
- une réduction du débit d’air passant au travers de l’évaporateur;
- et par conséquent une augmentation des pertes de charge dans le circuit de refroidissement;
- une augmentation de la résistance thermique de la surface de refroidissement;
- une chute de la température du fluide frigorigène.
Aussi, il découle de la réduction de débit que l’efficacité du rideau d’air sera moindre en favorisant l’augmentation des apports par induction, le passage accru de l’humidité de l’air ambiant et l’augmentation de la température de l’intérieur du meuble, … C’est en fait le principe du « chien qui se mange la queue ».
Sur le diagramme psychométrie ci-dessous, le givre qui se forme sur l’évaporateur correspond à l’humidité prise dans l’ambiance de vente et/ou au niveau des denrées non emballées.
Le givrage représente donc une contrainte importante pour le commerçant sachant que :
- l’on risque de briser la chaîne du froid;
- le meuble frigorifique devra être équipé de systèmes de dégivrage pouvant entraîner des consommations énergétiques supplémentaires.
Il est donc nécessaire d’effectuer des dégivrages réguliers.
Poids énergétique du dégivrage
Quel que soit le type de dégivrage (naturel ou électrique principalement), pendant cette opération, de la chaleur est retirée à la résistance chauffante ou à l’ambiance de vente en première approximation :
- pour faire fondre le givre;
- par les masses de l’évaporateur, du meuble et des denrées.
Exemple :
On considère en gros la répartition énergétique suivante pour un meuble frigorifique type gondole (longueur = 2,5 m) pour produits surgelés.
Poste |
Énergie nécessaire par dégivrage [kWh] |
% |
Fusion du givre |
0,18 |
12 |
Réchauffement masse évaporateur |
0,32 |
22 |
Réchauffement masse meuble |
0,38 |
26 |
Réchauffement des denrées |
0,56 |
38 |
Autre |
0,03 |
2 |
Total |
1.43 |
|
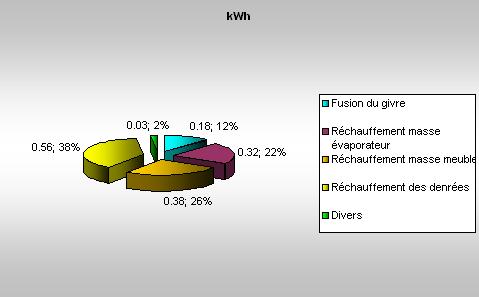
|
Temps du dégivrage
Dans le cas d’un dégivrage électrique et connaissant la puissance de la résistance électrique, il est possible d’évaluer le temps de dégivrage par la relation d’équilibre suivante :
∑énergies absorbées = ∑apports énergétiques
Où les apports énergétiques sont l’énergie fournie par la résistance chauffante pendant le temps de dégivrage et l’énergie apportée par l’ambiance externe au meuble, l’éclairage, les ventilateurs, …
|
Exemple :
En reprenant l’exemple ci-dessus et en considérant une résistance chauffante de 3 kW et des apports internes et externes de l’ordre de 1 kW, le bilan énergétique s’écrit :
1,43 [kWh] = (1 + 3) [kW] x tempsdégivrage [h]
Le calcul du temps de dégivrage donne :
tempsdégivrage [h] = 1,43 [kWh] / (1 + 3) [kW]
tempsdégivrage = 0.36 [h] ou 21 [min]
|
Influence de la protection de l’ouverture
L’ouverture des meubles frigorifiques sur la zone de vente est un enjeu majeur sur la gestion à la fois thermique et énergétique du meuble. Tout serait beaucoup plus simple si ces ouvertures étaient fermées par des portes isolées. Seulement, comme maintes fois signalées, l’ouverture libre des meubles est un argument visiblement de poids pour la vente. Les différentes parades pour limiter les apports par les ouvertures sont reprises dans le tableau suivant en s’inspirant de la littérature (Meubles et vitrines frigorifiques;G. Rigot; PYC édition; 2000) :
Type de meuble |
Type d’application |
Période de jour |
période de nuit |
Réduction des consommations énergétiques |
Horizontal |
négative |
rideau d’air |
rideau de nuit |
8 à 15 % |
couvercle simple |
15 à 30 % |
couvercle isolé |
25 à 45 % |
Vertical |
positif |
rideau d’air |
rideau de nuit |
12 à 30 % |
porte vitrée |
– |
négatif |
porte vitrée |
porte vitrée |
25 à 30 % |
En partant du principe que pour certaines applications l’ouverture du meuble doit rester libre, les constructeurs de meubles ont développé la protection de nuit ou « rideau de nuit ».
Le fait de tirer le rideau de nuit à la fermeture du magasin transforme, en simplifiant, les apports par induction et rayonnement au travers du rideau d’air du meuble en apports par pénétration au travers d’une paroi mince ; la face interne de la paroi étant fortement ventilée (résistance thermique d’échange superficiel Ri de l’ordre de 0,43 m².K/W) et la paroi externe peu ventilée (résistance thermique d’échange superficiel Re de l’ordre de 0,125 m².K/W). Pour une épaisseur de rideau faible (rideau synthétique l’épaisseur e de l’ordre de 3 mm) la résistance thermique du rideau est faible (R1 = e/λ de l’ordre de 1). La résistance thermique totale de la paroi RT est donnée par la relation suivante :
RT = Re + R1 + Ri [m².K/W]
RT = 0,043 + 0.125 + faible
RT ~ 0,125 [m².K/W]
|
Le coefficient de transmise thermique global U de la paroi s’exprime par la relation suivante :
U = 1 / RT
U = 1 / 0,125
U ~ 8 à 10 [W/m².K]
|
La simulation du passage d’un régime d’induction de journée à un régime par pénétration au travers du rideau de nuit en laissant l’éclairage allumé la nuit donne les résultats suivants :

On constate que la réduction des apports par induction est de l’ordre de 37 %. Des monitorings effectués dans le cadre de campagnes de mesures énergétiques menées par
Enertech pour l’Ademe en France (PDF) ont montré que la principale consommation de nuit des meubles frigorifiques ouverts positifs était due à l’induction. En effet, les meubles, à l’époque du monitoring n’étaient pas équipés de rideau de nuit. Leurs estimations de réduction de la consommation énergétique de nuit avec la pose de « couverture de nuit » était de l’ordre de :
- 35 % en période chaude;
- 28 % en période froide.
Ces informations recoupent d’autres résultats de campagne de mesure des consommations énergétiques.
Influence de l’éclairage

L’éclairage intensif des meubles est-il un critère de vente ?
On sait aussi que les apports internes comme l’éclairage régissent la puissance frigorifique nécessaire au maintien des températures au sein des meubles. La présence d’éclairage au sein du meuble non seulement représente une consommation électrique en soi, mais nuit aussi à la consommation énergétique des groupes de production de froid. En simplifiant, le commerçant passe deux fois à la caisse. Si l’efficacité de la production de froid n’est pas optimisée, sa consommation énergétique sera double.
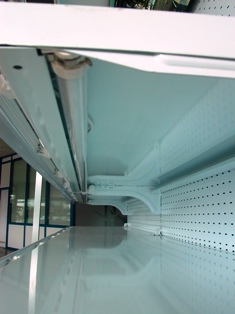
Éclairage de tablette au sein du meuble.
Le placement d’éclairage dans l’enceinte même réfrigérée est une mauvaise chose en soi. En effet, la plupart du temps, les constructeurs de meubles frigorifiques utilisent des lampes fluorescentes. Le problème est que ce type de lampes a une basse efficacité lumineuse aux basses températures comme le montre la figure suivante :
Efficacité lumineuse en fonction de la température ambiant.
Les luminaires placés en dehors de l’enceinte réfrigérée, quant à eux, sont plus efficaces dans le sens où ils n’interviennent pas comme apports internes dans le bilan frigorifique du meuble, mais en plus fonctionnent dans une plage de température où le flux lumineux est meilleur.
Composition fronton.
Actuellement, certaines grandes surfaces effectuent des essais afin de voir quel est l’impact de la suppression de l’éclairage dans les meubles frigorifiques sur la vente. Les résultats ne sont pas encore disponibles.
Extrait d’une étude de cas
En réalisant le monitoring des consommations hebdomadaires essentiellement électriques des installations de froid alimentaire, on peut tout de suite évaluer l’influence de l’éclairage des meubles sur leur bilan énergétique.
L’étude de cas réalisée par
Enertech pour l’Ademe (France) (PDF) sur un supermarché de 1 500 m² nous enseigne un certain nombre de choses par rapport à cet éclairage.
Les courbes hebdomadaires et journalières nous enseignent que les consommations de froid positif sont principalement influencées ici par l’éclairage et le climat. En effet, on voit que l’allumage de l’éclairage perturbe nettement la production de froid. Les fronts raides descendant et montant sur le temps de midi montrent cette influence. Il faut toutefois rester prudent, car on voit nettement que le climat intervient (surtout en période chaude comme c’est le cas ici).
La simulation dynamique réalisée au moyen de TRNSYS nous montre que l’éclairage est responsable de l’augmentation des consommations énergétique à hauteur de ~10 %.
Influence des ventilateurs
Les ventilateurs fonctionnent en permanence afin de maintenir les températures de consigne au sein des meubles. La puissance électrique nécessaire pour faire tourner les pales du ventilateur et, par conséquent, pour déplacer l’air au sein du meuble, est transformée en chaleur et participe au réchauffement de l’ambiance interne du meuble. Cet apport représente de l’ordre de 3 à 5 % de la consommation énergétique de la production de froid à l’évaporateur.
Influence des cordons chauffants
Les cordons servant à éviter la présence de buée sur les portes vitrées et à empêcher les portes des meubles mixtes d’être bloquées par le givre ou la glace. Ce type d’apports influence aussi le bilan énergétique du meuble. On estime sa participation à la dégradation du bilan énergétique à ~1 %.