Quelle efficacité en énergie primaire si la PAC fonctionne avec l’électricité du réseau belge ?
A en croire certains fabricants, la pompe à chaleur « crée » de l’énergie gratuite « récupère » l’énergie solaire gratuite et renouvelable…
En analysant le bilan énergétique, on constate en effet que pour 3 kWh thermiques fournis, environ 2 kWh thermiques peuvent provenir de l’air extérieur ou de l’eau d’une rivière, donc des sources d’énergie renouvelable. Néanmoins, pour fonctionner, elle utilise alors 1 kWh d’énergie électrique. Or la production électrique provenant du réseau a un rendement moyen de 35 % (qui provient la production et des pertes de transport et distribution de l’électricité). Il faut donc approximativement 3 kWh en centrale pour donner 1 kWh à la PAC, … qui fournira 3 kWh en chaleur. Sur base de cette analyse, on voit que le potentiel de réduction de consommation en énergie primaire par rapport à un chaudière traditionnelle au gaz ou mazout n’est pas si évident. Sur base de chiffres plus précis, il est effectivement possible de démontrer que les PAC permettent un réduction de la consommation en énergie primaire. Néanmoins, comme montré dans le raisonnement ci-dessus, il faut s’attendre à une réduction de dizaines de pour cent, mais pas une diminution drastique par un facteur 2 ou 3.
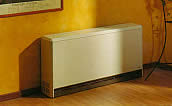
Remarque : Par rapport au chauffage à résistances électriques, le chauffage par pompe à chaleur est donc écologiquement beaucoup plus performant. Mais si le maître d’ouvrage envisage de remplacer ses accumulateurs, il va ouvrir la comparaison à l’ensemble des moyens de chauffage …
Les performances en termes d’énergie primaire dépendent essentiellement de deux facteurs, le coefficient de performance annuel (COPA) ainsi que le facteur de conversion en énergie primaire, que nous appellerons ici « f », de l’électricité disponible sur le réseau belge. Nous reprenons ci-dessous la valeur de COPA pour les différents types de PAC selon trois sources différentes. Dans les deux dernières colonnes, on reprend la valeur minimale et maximale de COPA que l’on considère dans les estimations de performance que nous allons réaliser dans cette page.
Type |
COPA (Source 2009 : EF4, facilitateur PAC de la Région wallonne) |
COPA (Source 2008 : Paul Cobut, Energy Saving Services) |
COPA (Source : rapport Ministerie van de Vlaamse Gemeenschap, ANRE) |
COPA minimum calcul |
COPA maximum calcul |
Air-Air |
|
2.8-3.5 |
2.7 |
2.5 |
3.5 |
Air-Eau |
2.5-3.5 |
3.0-3.5 |
2.7 |
2.5 |
3.5 |
Eau-Eau |
3-4.5 |
|
3.0-3.8 |
3.0 |
4.5 |
Eau glycolée-Eau |
3-4 |
3.2-4.0 |
3.2-3.6 |
3.0 |
4.0 |
Sol-Eau |
3-4 |
3.2-4.0 |
3.2-3.6 |
3.0 |
4.0 |
Sol-Sol |
3-4 |
3.2-4.0 |
3.2-3.6 |
3.0 |
4.0 |
ECS |
|
2.5-3.0 |
|
2.0 |
3.0 |
Synthèse des différentes valeurs de COPA diffusées par différentes sources : le facilitateur PAC de la Région wallonne, EF4, un spécialiste de la PAC en Belgique, Paul Cobut, un rapport du ministère du Ministère de la Communauté flamande sur l’installation des PAC.
La quantité d’énergie primaire consommée par kWh d’énergie thermique utile est calculée pour les différents types de PAC : plus la valeur est faible et plus la technologie est intéressante au niveau de la consommation en énergie primaire. À titre comparatif, les chaudières au gaz et au mazout se situent approximativement autour de 1.2-1.3.
On considère un scénario conservatif avec les valeurs les plus basses de COPA et un scénario positif avec les valeurs maximales. Premièrement, on considère un facteur de conversion pour l’électricité de notre réseau de 3.1. Cela veut dire que pour obtenir 1 kWh électrique en distribution, il faut compter 3.1 kWh en énergie primaire. Cette valeur correspond au cas réel de notre réseau qui produit essentiellement son électricité sur base d’énergie nucléaire (approximativement 60 %). A titre indicatif, on peut considérer la valeur de facteur de conversion prescrite par la PEB qui correspond à la part non nucléaire du réseau.
Type |
COPA minimum calcul |
COPA maximum calcul |
Rapport Eprimaire/Eutile pour f = 3.1 et COPA minimum |
Rapport Eprimaire/Eutile pour f= 3.1 et COPA maximum |
Rapport Eprimaire/Eutile pour f =2.5 (PEB) et COPA minimum |
Rapport Eprimaire/Eutile pour f = 2.5 (PEB) et COPA maximum |
Rapport Eprimaire/Eutile par ANRE |
Air-Air |
2.5 |
3.5 |
1.25 |
0.88 |
1.0 |
0.71 |
0.9 |
Air-Eau |
2.5 |
3.5 |
1.25 |
0.88 |
1.0 |
0.71 |
0.9 |
Eau-Eau |
3.0 |
4.5 |
1.0 |
0.68 |
0.83 |
0.55 |
0.66-0.83 |
Eau glycolée-Eau |
3.0 |
4.0 |
1.0 |
0.77 |
0.83 |
0.62 |
0.76 |
Sol-Eau |
3.0 |
4.0 |
1.0 |
0.77 |
0.83 |
0.62 |
0.73 |
Sol-Sol |
3.0 |
4.0 |
1.0 |
0.77 |
0.83 |
0.62 |
0.73 |
ECS |
2.0 |
3.0 |
1.5 |
1.0 |
1.25 |
0.83 |
|
Rapport entre consommations en énergie primaire et énergie utile pour les différentes technologies de PAC suivant deux scénarios de COPA (conservatif et optimiste) et deux facteurs de conversion de l’électricité du réseau en énergie primaire.
Si on prend l’hypothèse la plus défavorable de COPA minimum avec un facteur de conversion de 3.1 (avec nucléaire), on voit que le rapport entre énergie primaire et énergie thermique utile délivrée est du même ordre de grandeur que pour les chaudières gaz ou mazout. Seule la production d’ECS donne des résultats moins intéressants. Par contre, dès que l’on travaille avec les meilleures performances de PAC (COPA max), les valeurs sont nettement plus intéressantes. Sur base de cette observation, nous proposons la conclusion suivante : avec les COPA attendu les plus faibles, les PAC sont aussi performantes que les chaudières en ce qui concerne l’énergie primaire, par contre, en travaillant sur base des meilleures performances, un gain substantiel est possible.
Cela met aussi clairement en évidence l’intérêt de travailler avec dans les meilleures conditions pour obtenir les meilleures performances : bon matériel, bonne conception, bonne régulation et bon maintien, entretien de l’installation. La qualité est un aspect très important. Il existe un label au niveau wallon pour l’installation des pompes à chaleur, le label PACQUAL : voir
le site internet de RBF (Renewable Buiseness Facilitateur) qui représente les intérêts d’entreprises wallonnes actives dans le renouvelable.
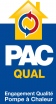
Logo du label PACQUAL (Source :
site internet RBF).
Quelle efficacité en émission de CO2 si la PAC fonctionne avec l’électricité du réseau belge ?
Comme pour l’analyse de la consommation en énergie primaire, le coefficient de performance annuel de la PAC, le COPA, est un paramètre de première importance. Les valeurs introduites dans le tableau ci-dessus, valeurs typiques minimales et maximales, seront reprises pour l’évaluation des émissions de CO2. En ce qui concerne l’électricité du réseau, nous tenons compte de la production des centrales nucléaires. Cela donne une émission de 302 grammes d’équivalents-CO2 par kWh électrique consommé sur le réseau. À titre comparatif, nous avons placé dans le tableau les émissions caractéristiques de CO2 pour un chauffage direct par l’électricité et par une chaudière au gaz (dont on considère que le rendement saisonnier est de 90 %, le cycle complet du combustible avec 232 grammes d’équivalent-CO2 produits par kWh thermique final).
Type |
COPA minimum calcul |
COPA maximum calcul |
Emission de CO2 : COPA mininmum [gramme équivalent CO2/kWh] |
Emission de CO2 : COPA maximum [gramme équivalent CO2/kWh] |
Air-Air |
2.5 |
3.5 |
120 |
86.28 |
Air-Eau |
2.5 |
3.5 |
120 |
86.28 |
Eau-Eau |
3.0 |
4.5 |
100 |
67.11 |
Eau glycolée-Eau |
3.0 |
4.0 |
100 |
75.5 |
Sol-Eau |
3.0 |
4.0 |
100 |
75.5 |
Sol-Sol |
3.0 |
4.0 |
100 |
75.5 |
ECS |
2.0 |
3.0 |
151 |
100 |
Chauffage électrique direct |
|
|
302 |
302 |
Chauffage au gaz naturel |
|
|
257 |
257 |
Émission de CO2 pour les différentes technologies de PAC suivant les deux scénarios de performance COPA.
Le résultat est sans appel : quelque soit le niveau de performance, COPA, considéré, les PAC émettent nettement moins de CO2 que le chauffage traditionnel et, évidemment, que le chauffage électrique direct. C’est parfois un argument qui est avancé pour promouvoir l’installation des pompes à chaleur. Cet argument est correct, mais nous tenons néanmoins à donner une nuance. Le lecteur pourra ainsi se faire sa propre opinion.
Ces performances en émission de CO2 des PAC proviennent essentiellement de la structure de la production électrique en Belgique, essentiellement dominée par les centrales nucléaires. Sur base des analyses de bilan CO2 actuelles, le nucléaire émet très peu de CO2. Dans le débat, il faut savoir aussi que certains groupes remettent en question cette hypothèse de départ. D’après ceux-ci, la production d’énergie par centrales nucléaires contiendrait beaucoup d’ « énergie grise » (pour la construction, démantèlement, gestion des déchets, …). Comme les centrales nucléaires émettent relativement peu de CO2 et que les PAC consomment de l’électricité, les émissions de CO2 sont donc relativement plus faibles, ce qui est tout bénéfice pour éviter le réchauffement climatique. Néanmoins, il ne faut pas perdre de vue que le nucléaire produit des déchets qui peuvent être potentiellement très dangereux pour l’environnement. La problématique des déchets nucléaires est un sujet bien connu. En conclusion, on a, quelques part déplacé le risque du réchauffement climatique (CO2) vers le danger des déchets nucléaires.
Quelle efficacité environnementale si la PAC fonctionne avec l’électricité produite de manière renouvelable ?
Les conclusions données précédemment considéraient que l’électricité consommée par la PAC provenait du réseau, réseau essentiellement dans son état actuel. Les conclusions sont tout à fait différentes si on considère que l’électricité qui alimente la PAC est produite sur base d’énergie renouvelable. Dans ce cas, les performances environnementales des PAC sont remarquables.
Quelle rentabilité financière ? Investissement et coût à l’utilisation
Une installation de chauffage basée sur une PAC est généralement plus chère à l’investissement qu’une installation équivalente basée sur des chaudières traditionnelles. On l’observe du moins clairement dans le secteur domestique. Par contre, pour le domaine du tertiaire, nous manquons d’information.
En ce qui concerne le coût d’utilisation, les frais liés à la consommation d’électricité, le coefficient de performance annuel, COPA est encore central.
Nous allons reprendre notre petite étude avec la plage de valeurs de COPA rencontrées en pratique. Le prix de l’électricité est pris à 192 c€/kWh en heures pleines et 105 c€/kWh en heures creuses. Le prix du gaz est fixé à 70 c€/kWh. Ces valeurs sont caractéristiques du secteur domestique en juin 2009 (Source : Apere, Renouvelle). Les calculs suivants sont bien sûr des instantanés dans la mesure où le prix de l’énergie est amené à évoluer dans le temps.
Type |
COPA minimum calcul |
COPA maximum calcul |
Coût : COPA minimum [c€/kWh] (elec de jour) |
Coût : COPA maximum [c€/kWh] (elec de jour) |
Air-Air |
2.5 |
3.5 |
76.8 |
54.8 |
Air-Eau |
2.5 |
3.5 |
76.8 |
54.8 |
Eau-Eau |
3.0 |
4.5 |
64 |
42.6 |
Eau glycolée-Eau |
3.0 |
4.0 |
64 |
48 |
Sol-Eau |
3.0 |
4.0 |
64 |
48 |
Sol-Sol |
3.0 |
4.0 |
64 |
48 |
ECS |
2.0 |
3.0 |
96 |
64 |
Chauffage électrique direct
(élec. de jour) |
|
|
192 |
192 |
Chauffage électrique accumulation
(élec. de nuit) |
|
|
105 |
105 |
Chauffage au gaz naturel |
|
|
77.8 |
77.8 |
Coût du kWh thermique utile produit pour des PAC fonctionnant avec l’électricité de jour (heures pleines). Le prix de l’énergie est aligné sur le secteur domestique à la date de juin 2009.
Le Tableau ci-dessus considère que les PAC fonctionnent essentiellement sur l’électricité de jour, en heures pleines durant lesquelles les prix sont les plus élevés. C’est donc un cas assez défavorable. Comparé à un système conventionnel comme une chaudière au gaz, on voit que les PAC air-air et air-eau sont comparables au gaz avec les COPA faibles. Pour les autres approches, l’énergie fournie est légèrement moins chère que le gaz. Par contre, en considérant les meilleures performances, on obtient des prix sensiblement plus intéressants que le gaz. Cela met encore une fois en évidence l’importance d’installations de PAC qui fonctionnent de manière optimale, et donc, présentant les meilleurs COPA.
On voit donc l’équilibre qu’il faut atteindre pour réaliser une installation rentable basée sur une PAC. L’investissement sera généralement plus cher que pour une chaudière traditionnelle, mais le coût d’utilisation sera moindre. Ces gains durant la durée d’utilisation du matériel doivent contrebalancer ce surinvestissement. Dans ce genre de calcul, on considère typiquement que la durée d’utilisation d’une pompe à chaleur ou une chaudière est de 20 ans. En d’autres termes, il faut récupérer les surinvestissements sur ces 20 années au maximum pour que le projet soit rentable.
Dans les calculs précédents, nous avons supposé que la PAC fonctionnait avec l’électricité de jour, en heures pleines. En fait, il est possible de stocker en partie la chaleur fournie par la PAC durant la nuit (chauffage par le sol, par ex.) et donc d’avoir une partie substantielle du coût en électricité de nuit. Néanmoins, cette gestion détériore le rendement du système de chauffage (forte inertie, difficulté de régulation en période ensoleillée, air extérieur plus foid la nuit si PAC Air/eau, …). En conclusion, il est difficile d’établir un prix du kWh en travaillant de cette manière.
Pourquoi ne trouve-t-on pas plus de pompes à chaleur dans nos maisons ?…
Supposons une PAC air-air. Elle doit fonctionner avec du courant de jour. Pour le particulier, le prix du kWh électrique est 3 x plus élevé que le prix du kWh thermique (gaz, fuel, …). Avec un COPA inférieur à 3, la rentabilité financière n’existe plus pour la PAC… Malgré un rendement de près de 300 % sur l’énergie électrique fournie, c’est pratiquement aussi cher que de produire la chaleur par un système traditionnel au gaz ou au fuel…
Supposons une PAC air-eau, avec un système de chauffage par le sol. Cette fois, l’inertie du chauffage par le sol permet d’utiliser le courant de nuit dont le prix du kWh est de l’ordre de 2 fois celui du kWh thermique. Ainsi, la PAC se justifie beaucoup mieux. Seul inconvénient : la régulation du chauffage par le sol est difficile (quelle charge du sol durant la nuit ? Quel temps fera-t-il demain ? Si les occupants sont absents toute la journée, pourquoi chauffer ? Si le sol est déjà chaud, l’arrivée des rayons solaires va provoquer une surchauffe…) et le système reperd une part de sa rentabilité par les pertes de régulation …
Bien sûr, l’usage de la PAC est nettement plus logique que le chauffage électrique, direct ou à accumulation. Ces derniers systèmes devraient d’ailleurs être interdits, pour protéger le consommateur(dépendant du choix fait par des promoteurs immobiliers) et la société (bilan écologique désastreux). |