Principe de base : abaisser la température de condensation
Abaisser la température de condensation, c’est abaisser le niveau de pression à la sortie du compresseur, c’est donc diminuer le travail de celui-ci et l’énergie qu’il consomme. On considère qu’abaisser la température de condensation de 1°C génère environ 3 % d’économie.
Abaisser la température de l’air extérieur
L’emplacement du condenseur doit éviter un réchauffement local de l’air. Par exemple, un condenseur placé sur une toiture couverte de roofing noir entraînera une surchauffe locale de l’air de plusieurs degrés en période d’ensoleillement … Le fait de répandre du gravier blanc sur la toiture et sous le condenseur sera favorable.
L’emplacement du condenseur devra éviter un ensoleillement direct de l’échangeur. Si le placement à l’ombre est impossible, le placement d’un système d’ombrage permettra d’abaisser le niveau de température.
Eviter la recirculation de l’air aspiré
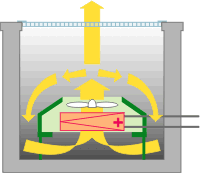
Si le condenseur est situé trop prêt d’une paroi, l’air expulsé par le ventilateur centrifuge risque d’être rebouclé vers l’aspiration : de l’air chaud se mélange à l’air froid, la température de l’air d’aspiration augmente, … de même que la température de condensation.
Comment s’en rendre compte ? En se plaçant entre la paroi et le condenseur lorsque celui-ci est à l’arrêt. Au démarrage du condenseur, on ne peut sentir l’arrivée de chaleur. À défaut, on utilisera la poire à fumée.
Favoriser l’échange de chaleur
Valeur test
Pour un condenseur à eau, si l’écart entre T°condensation et la T°eau sortie condenseur > 6 à 10 K, il y a encrassement et donc chute de rendement. Si le dT° dépasse 15 K, il faut envisager l’extension de la surface du condenseur.
Pour un condenseur à air, l’écart entre la température de condensation et la température de l’air à l’entrée doit être de l’ordre de 15 à 20 K à pleine charge. A charge partielle, le delta T° doit diminuer proportionnellement.
Remarque : pour connaître la température de condensation, lire la haute pression, et se référer tableau de correspondance température/pression du fluide frigorigène (Exemple pour le R22, R134a et R407c). |
- Par un nettoyage régulier des ailettes (condenseurs à air), tout particulièrement à l’automne, avec la chute des feuilles. Nettoyage à l’air comprimé (si l’épaisseur des ailettes est inférieure à 0,15mm), ou à l’eau à faible pression si présence de boues (attention à la fragilité des ailettes, diriger le jet bien perpendiculairement au condenseur).
- Par un détartrage régulier des conduites (condenseurs à eau). Si une tour ouverte est installée, un adoucisseur d’eau s’impose.
Modifier la régulation du condenseur
Nous devrions avoir des excellents rendements dans nos régions où les canicules sont rares ! La température extérieure avoisine les 12 à 20°C lorsque la clim est en route. La température de condensation devrait être de l’ordre 24 à 32°C. Mieux, certains locaux à charges internes importantes (par exemple, les salles informatiques) doivent être aussi climatisés en mi-saison ou encore en hiver. Dans ce cas, lorsque la température de l’air extérieur diminue, la capacité de refroidissement du condenseur augmente.
En théorie, c’est tout bénéfice pour le compresseur qui a moins de mal à travailler !
Et pourtant …
Problème avec les détendeurs thermostatiques
Le constructeur souhaite qu’une différence de pression minimale existe au niveau du détendeur, pour assurer une quantité de débit de fluide frigorifique suffisante dans l’évaporateur. C’est la Haute Pression qui pousse le réfrigérant à travers l’orifice de la vanne du détendeur. Il en résulte, avec une haute pression trop faible, que l’alimentation en réfrigérant est insuffisante, particulièrement au démarrage. Le compresseur aspire mais il est sous-alimenté.
La basse pression devient aussi insuffisante et le groupe se met en sécurité Basse Pression. Mais comme cette sécurité est à réenclenchement automatique, le groupe « pompe », se fatigue et finalement déclenche par son thermique.
Avec un détendeur thermostatique, il est donc nécessaire de maintenir une Haute Pression suffisamment élevée. Dès lors, le constructeur impose une pression minimale, côté HP, à la sortie du condenseur (par exemple 12 bars pour le R22).
Ce problème est renforcé en hiver… Si l’air est à 0°C, la surface d’échange devient excessive. De plus, on n’aura plus besoin de la pleine puissance frigorifique. De sorte que le condenseur sera largement surdimensionné pendant les périodes froides.
S’il fait plus froid dehors, le constructeur va diminuer le débit d’air de refroidissement (en arrêtant l’un ou l’autre ventilateur, par exemple), mais il va maintenir le niveau de pression ! en fait, la régulation des ventilateurs sera réalisée sur base du pressostat HP.
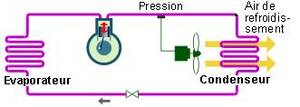
Il y a économie sur le ventilateur… mais pas sur le compresseur !
Première amélioration : travailler avec un ventilateur à vitesse variable ou une cascade de ventilateurs
Supposons que le ventilateur du condenseur fonctionne en tout ou rien, avec l’exigence constructeur de maintenir les 12 bars minimum.
Par exemple, il s’enclenche lorsque la pression monte à 16 bars et déclenche lorsque la pression descend à 12 bars. Ceci entraîne des cycles on-off « rapides » (+/- 2 min.) et une « fatigue » du moteur. En plus la mise en route brutale du ventilateur provoquera une chute soudaine de la pression et de la température de condensation. Ceci provoque à son tour une ré-évaporation du liquide resté à la même température. Les bulles de vapeur provoqués par ce phénomène peuvent perturber le bon fonctionnement du détendeur et donc de l’installation (« flash gaz »).
Si par contre, on utilise un ventilateur à vitesse variable (moteur spécial ou régulateur de vitesse de rotation externe), en plus de la réduction de consommation du ventilateur, on optimisera le fonctionnement du compresseur qui restera régulé à 12 bars (dès que la pression augmente, le ventilateur accélère; et si la charge augmente encore, c’est la pression qui augmente naturellement).
Si le condenseur dispose de plusieurs ventilateurs, on obtient un résultat similaire à partir d’une mise en cascade des ventilateurs, via un pressostat à plusieurs étages. Cette fois, la pression de condensation est stable, ce qui évite la formation de bulles de gaz à l’entrée de l’évaporateur.
Remarque : installer la vitesse variable sur les ventilateurs existants peut demander le remplacement du moteur du ventilateur.
Cas particulier
Comme le condenseur est entièrement à l’extérieur, par très basse température, c’est toute la masse métallique qui est à 0°C et, même clapets complètement fermés, le réfrigérant se condense à trop faible pression. Il faut dans ce cas rendre inopérants un certain nombre de tubes.
Pour les rendre inopérants, il suffit de remplir d’office certains tubes avec du réfrigérant liquide. Ce réfrigérant liquide sera sous-refroidi mais la surface d’échange utile du condenseur ayant fortement diminué, il ne pourra en condenser trop. Ce remplissage est obtenu par une vanne à 3 voies fonctionnant automatiquement et branchée sur un réservoir auxiliaire de réfrigérant.
Comme il faut une certaine quantité de liquide pour remplir ces tubes, il y a lieu de prévoir un réservoir et une quantité de réfrigérant suffisamment grande.
Exemple.
Un climatiseur devant fonctionner pour des températures extérieures inférieures à 17°C doit être équipé d’un ventilateur de condenseur à vitesse variable. La diminution de vitesse du ventilateur est alors commandée par un pressostat ou un thermostat placé sur le condenseur. La puissance d’échange de celui-ci est ainsi maintenue constante quelle que soit la saison.
Au minimum, le fonctionnement du ventilateur sera commandé en tout ou rien. Idéalement la vitesse sera modulée, soit en continu, soit par paliers.
|
Deuxième amélioration : travailler avec un détendeur électronique
Si le détendeur thermostatique travaille généralement avec une température minimale de condensation de 35°C, le détendeur électronique peut travailler avec une température minimale de condensation de 20°C !
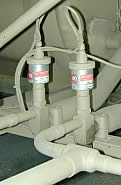
Détendeur électronique.
Il est plus cher à l’investissement, mais ce prix est largement récupéré par l’usage de l’installation.
De plus, la présence d’un détendeur numérique permet d’optimiser la température de condensation en fonction de la charge du compresseur.
Exemple.
Voici la séquence prévue par un constructeur de régulation :
A 100 % de puissance, l’écart « température de condensation – fluide de refroidissement » est choisi à 12 K.
A 0 % de puissance, l’écart est de 4 K : la consommation du compresseur est diminuée par la baisse de pression de condensation et le ventilateur adaptera sa vitesse de rotation pour maintenir cette consigne. L’écart n’est pas de 0 K, car les ventilateurs tourneraient tout le temps.
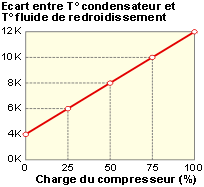
Exemple
si la T°ext = 30°C et Travail compresseur = 25 %, la T°condensation = 36°C
si la T°ext = 30°C et Travail compresseur = 50 %, la T°condensation = 38°C
si la T°ext = 20°C et Travail compresseur = 25 %, la T°condensation = 26°C
si la T°ext = 10°C et Travail compresseur = 25 %, la T°condensation = … 20°C car c’est la valeur minimale de condensation.
|
Remarque.
Adopter une température minimale de condensation de 20°C suppose que le sous-refroidissement soit suffisamment élevé.
A défaut, la moindre perte de charge sur le tracé va provoquer une vaporisation dans le condenseur (« flash-gaz »). C’est parfois un problème rencontré lorsqu’il faut remonter plusieurs mètres avec la tuyauterie.
Pour s’en prémunir, il est possible de sous-refroidir volontairement le liquide par la création d’une zone de sous-refroidissement dans le condenseur (voir figure), ou en plaçant un échangeur à plaques sur le liquide (à la sortie).
Régulation de la tour de refroidissement d’un condenseur à eau
La tour de refroidissement est commandée suivant la même logique : maintenir constante la température de l’eau de refroidissement du condenseur.
Classiquement, on retrouvera une régulation par vanne 3 voies diviseuse : l’eau de sortie du condenseur est partagée entre l’échangeur de la tour et le retour vers le condenseur. Si ce système permet de conserver le débit constant dans le condenseur (ce qui limite le dépôt de sédiments), il est peu efficace au niveau des ventilateurs : ceux-ci tournent en permanence, quels que soient les besoins de refroidissement. Or le coût de fonctionnement des ventilateurs est loin d’être négligeable…
Aussi est-il préférable de concevoir une installation qui régule d’abord sur le nombre et la vitesse des ventilateurs (ventilateur à 2 vitesses, ou idéalement, ventilateur à vitesse variable), pour ensuite affiner en modulant sur la position de la vanne diviseuse.
N’oublions pas que toute l’installation de climatisation est dimensionnée pour les jours de canicule. Hélas, ces jours sont rares dans nos contrées…! Il est donc facile d’imaginer que les besoins réels moyens seront largement en dessous des puissances de dimensionnement.
Réduire la vitesse du ventilateur de moitié, c’est diviser sa consommation par 8 !
Enfin, tout utilisateur d’une tour de refroidissement qui utilise celle-ci en hiver doit se poser la question de la pertinence de refroidir l’eau glacée sans intervention de la machine frigorifique : c’est la technique du free-chilling.