
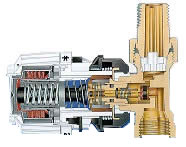
Vanne thermostatique.
Attention, les vannes thermostatiques ne sont pas la « panacée universelle », et ne permettent pas de résoudre toutes les situations de confort et de surconsommation.
Il est important d’en comprendre le fonctionnement pour en cerner l’utilité.
En résumé, une vanne thermostatique permet de limiter la puissance d’un corps de chauffe dans des locaux où les apports de chaleur (ensoleillement, occupation importante, bureautique, éclairage, …) sont supérieurs aux autres, variables et conduisent à des problèmes de surchauffe locale.
Exemple.
Par exemple, il faut préparer de l’eau pour l’ensemble des radiateurs de classes. Si dans un local 8 élèves sont présents, il doit faire bon. Si dans le local voisin 25 élèves sont présents, la température risque de s’élever rapidement (25 élèves x 100 Watts/élève = 2 500 Watts, soit l’équivalent d’un radiateur moyen chauffé à 80° !). Il est impératif de couper le chauffage dans ce local. On arriverait aux mêmes conclusions avec l’apport solaire par de larges baies vitrées.
Et c’est là qu’intervient la vanne thermostatique, comme régulatrice finale des apports.
Attention : elle ne peut agir que dans le sens de la réduction ! Aussi, il sera utile d’ajuster la régulation centrale sur les locaux les plus exigeants (locaux de coin, locaux sous la toiture, …).
|
Il existe sur le marché, des vannes qui peuvent s’adapter à la plupart des publics :
- locaux où les occupants sont capables de gérer eux-mêmes le réglage des vannes (bureaux individuels, de 2 .. 3 personnes),
- locaux où les occupants ne se sentent pas responsable du réglage (classes),
- locaux où les vannes peuvent subir des détériorations (salles de sport, lieux publics, ….).
Il ne faut donc pas systématiquement rejeter cette solution sous prétexte que le public ne saura pas la gérer. Si un doute subsiste quant à la résistance mécanique par rapport au public visé, un essai peut être mené avec une ou deux vannes, avant de se lancer dans l’installation complète.
Il est clair que si on opte pour les vannes les plus simples dont le réglage est laissé à l’occupant, une information de ce dernier sera nécessaire, pour que le résultat escompté soit atteint.
Le gain
Ici aussi, il est impossible de chiffrer précisément le gain énergétique que l’on peut escompter du placement de vannes thermostatiques, ne fut-ce que parce qu’il est impossible de chiffrer précisément la situation de départ.
On peut cependant, par un rapide calcul, estimer l’intérêt de cette amélioration.
Exemple.
Ordre de grandeur : un degré de trop dans un local = 7 .. 8 % de surconsommation !
Prenons un immeuble de bureau de 1 000 m² dont la consommation annuelle est de 15 000 litres de fuel par an.
Dans la salle de réunion de 60 m², occupée 6 h/jour, 250 jours par an, il fait systématiquement 22°C au lieu de 20°C.
Quel est l’ordre de grandeur de l’économie que l’on peut réaliser en plaçant des vannes thermostatiques dans cette salle ?
« A la grosse louche » :
> Consommation de combustible imputable à la salle :
15 000 [litres/an] / 1 000 [m²] x 60 [m²] = 900 [litres/an]
> Estimation du pourcentage d’économie lié au placement de la vanne : réduction de 2 K en journée et de 1 K la nuit et le week-end (après la coupure du chauffage, la température intérieure reste plus chaude la nuit, suite à l’augmentation de la température intérieure le jour). Prenons 1,5 K en moyenne.
Économie réalisable par des vannes thermostatiques : 900 [litres/an] x 8 [%/K] x 1,5 [K] = 108 [litres/an] ou 32 [€/an] (à 0,30 [€/litre fuel]).
Économie à laquelle il faut rajouter l’amélioration du confort.
Le coût d’une vanne est de l’ordre de 12,5 .. 25 € pour une vanne thermostatique traditionnelle ou 25 .. 37,5 € pour une vanne « incassable ». Hors placement.
Le temps de retour réel dépend du nombre de radiateurs à équiper dans le local !
|
Précautions
Le placement de vannes thermostatiques dans un bâtiment demande certaines précautions.
Placement d’une soupape différentielle
Lorsqu’une vanne thermostatique se ferme, le débit d’eau est arrêté dans la branche qui va vers le radiateur. C’est comme lorsqu’un enfant bouche de son pouce l’embouchure du jet d’une fontaine, … les autres jets sortent plus fort ! En fait, c’est la pression qui monte dans le réseau et tous les autres radiateurs voient leur débit augmenter. Toutes les autres vannes vont se fermer un peu plus…
Imaginons que vers midi quelques vannes soient encore ouvertes : elles reçoivent toute la pression de la pompe, elles ne s’ouvrent que d’une fraction de millimètre… et se mettent à siffler !
Une vanne thermostatique ne doit pas sentir si sa voisine vient de se fermer. Il est donc utile de stabiliser la pression du réseau. C’est le rôle de la soupape à pression différentielle. Placée après le circulateur, elle lâche la pression lorsque les vannes se ferment. En quelque sorte, elle « déverse le trop plein vers le retour ».
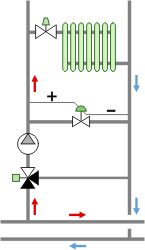
Placement d’une soupape différentielle sur le départ du circuit pour compenser la fermeture des vannes thermostatiques.
Encore faut-il pouvoir calibrer le niveau de pression maintenu entre le départ et le retour… Si l’installation est nouvelle, le bureau d’études connaît la pression nominale nécessaire. Si l’installation est ancienne, on ne pourra y aller que par essai successif en diminuant progressivement la pression. La pression manométrique du milieu de la courbe du circulateur (voir catalogue du fournisseur) est également une indication.
Une solution d’aujourd’hui : le circulateur à vitesse variable
Force est de constater que la solution de la vanne à pression différentielle n’est pas très élégante ! Créer une pression à la pompe et la lâcher juste après, sur le plan énergétique, c’est un peu pousser sur l’accélérateur et le frein en même temps !
Actuellement, il est possible d’installer un circulateur à vitesse variable : la vitesse est régulée de telle façon que la pression du réseau reste constante. Si seulement quelques vannes sont ouvertes, il tournera à vitesse réduite. L’achat d’un circulateur avec régulateur de vitesse intégré est rapidement amorti durant l’exploitation car la consommation évolue en fonction du cube de la vitesse: une vitesse réduite de moitié, c’est une consommation électrique divisée par 8 !
Vannes thermostatiques et thermostat d’ambiance
Un local abritant un thermostat d’ambiance ne peut jamais comporter de vanne thermostatique.
En effet, si la consigne du thermostat d’ambiance est plus élevée que la consigne des vannes, le thermostat ne sera jamais satisfait puisque les vannes thermostatiques se fermeront avant.
Dans le cas d’une installation dans laquelle le thermostat agit directement sur le brûleur, cette demande entraînera le fonctionnement permanent du brûleur jusqu’à ce que la température de la chaudière atteigne sa limite haute. En résumé, la chaudière fonctionnera en permanence à haute température, ce qui est énergétiquement moins efficace.
Si le thermostat agit sur une vanne mélangeuse, celle-ci restera en permanence en position ouverte, alimentant les circuits à température maximale.
Dans les deux cas, il peut en résulter une surconsommation et des surchauffes dans les autres locaux.
À l’inverse, si la consigne du thermostat est plus basse que la température de consigne des vannes thermostatiques, ces dernières resteront en permanence ouvertes en grand et deviennent donc inutiles.
En résumé, si un thermostat d’ambiance et des vannes thermostatiques sont présents dans un même local, ces dernières doivent en permanence être ouvertes au maximum pour permettre au thermostat de jouer son rôle pleinement.
Vannes thermostatiques et circuits corrodés
« Les vannes thermostatiques se bloquent souvent ! »
Voici un des arguments repris par les détracteurs des vannes thermostatiques.
En effet, le faible degré d’ouverture d’une vanne thermostatique (max : 2 mm), les rend sensibles aux dépôts de calcaire ou aux boues de l’installation. Leur application dans une installation existante présentant ces problèmes est donc délicate.
Ce n’est cependant pas pour cela qu’il faut rejeter d’office la solution des vannes thermostatiques. Mais au préalable, les problèmes d’entartrage et de corrosion doivent être combattus. Notons que cela devrait se faire, quels que soient les projets d’amélioration, car c’est l’ensemble de l’installation qui est en péril, y compris les chaudières :
- suppression des fuites,
- vérification ou modification du système d’expansion,
- désembouage,
- analyse et traitement d’eau,
- ….
Vannes thermostatiques bloquées en début de saison de chauffe
Il faut éviter de laisser une vanne complètement fermée durant une longue période (c’est valable aussi bien pour une vanne thermostatique que pour une vanne manuelle), par exemple durant tout l’été.
En effet, la pression exercée sur le clapet de fermeture est telle que la vanne risque de rester « collée » lorsque l’on désirera l’ouvrir à nouveau.
Il est donc conseillé de toujours maintenir une certaine consigne à la vanne, par exemple en la réglant sur la position « antigel ». Dans ce cas, en été, elle se fermera, mais avec une pression nettement moindre que si elle est fermée manuellement.